1.1: Sistemas de conversión de bioenergía
( \newcommand{\kernel}{\mathrm{null}\,}\)
Sergio Capareda
Departamento de Ingeniería Biológica y Agropecuaria
Universidad A&M de Texas
College Station, Texas, Estados Unidos
Variables
Introducción
Este capítulo introduce la importancia de analizar el balance energético y la viabilidad económica de los sistemas de conversión de biomasa. En principio, la energía utilizada para la producción, conversión y utilización de biomasa debe ser menor que el contenido energético del producto final. Por ejemplo, uno de los mayores componentes energéticos para el cultivo de biomasa es el fertilizante (Pimentel, 2003), por lo que este componente debe ser incluido en los análisis de los sistemas energéticos. Este capítulo también introduce algunas vías de conversión de biomasa y describe los diversos productos y coproductos de las conversiones, con un enfoque en los indicadores tecnoeconómicos para evaluar la viabilidad de un sistema de conversión particular. La evaluación de sustentabilidad de combustibles derivados de biomasa, materiales y coproductos incluye, entre otros, tres componentes clave: balance energético, impacto ambiental y beneficio económico. Este capítulo se centra principalmente en el balance energético y las cuestiones económicas que influyen en los sistemas de bioenergía.
Conceptos
Los principales combustibles comerciales utilizados en el mundo hoy en día son el gas natural, la gasolina (gasolina), el combustible de aviación, el diesel, los fuelóleos y los combustibles sólidos como el carbón. Estos combustibles fósiles comerciales podrían ser reemplazados por biocombustibles y combustibles sólidos derivados de la biomasa mediante el uso de tecnologías de conversión. Existen recursos específicos de biomasa que se adaptan bien a cada tecnología de conversión. Por ejemplo, los cultivos de azúcar (caña de azúcar y sorgo dulce) son buenos materiales de alimentación para la conversión del bioetanol; los cultivos oleaginosos (soja y aceite de canola) son la materia prima ideal para la producción de biodiesel; y la biomasa lignocelulósica (por ejemplo, desechos de madera, estiércol animal o pastos) es el sustrato principal para hacer biogás. Los sistemas de conversión térmica convierten todos los demás recursos de biomasa en productos valiosos.
La sustitución de estos combustibles primarios por alternativas de base biológica es una forma de abordar la sustentabilidad energética. El calor y la energía eléctrica, necesarios en todo el mundo, también se pueden producir a través de la conversión de biomasa a través de procesos de conversión termoquímica como pirólisis y gasificación para producir gas de síntesis (o también llamado gas de síntesis, una versión más corta). El gas de síntesis puede quemarse para generar calor y puede limpiarse a fondo de alquitrán y usarse en un motor de combustión interna para generar energía mecánica o eléctrica. Los futuros requisitos mundiales para otras necesidades básicas de energía y energía se pueden satisfacer utilizando una amplia gama de recursos de biomasa, incluidos cultivos de petróleo y azúcar, estiércol animal, residuos de cultivos, desechos sólidos municipales (RSM), madera combustible, plantas acuáticas como microalgas y agricultura energética dedicada para la producción de energía. Los tres productos principales de la conversión térmica son bio-carbón sólido, líquido y gas de síntesis.
Un sistema de conversión de energía de biomasa puede producir uno o más de cuatro productos principales: calor, electricidad, combustible y materias primas. El objetivo de cualquier proceso de conversión es lograr la mayor eficiencia de conversión posible minimizando las pérdidas. La eficiencia de conversión de energía para cualquier tipo de producto puede calcularse como:
Energy Conversion Efficiency (%)= Energy Output (MJ) Energy Input (MJ)×100%
Existen tres vías fundamentales de conversión de biomasa (Figura1.1.1): fisicoquímica, biológica y térmica. La conversión fisicoquímica es el uso de químicos o catalizadores para la conversión a temperaturas ambiente o ligeramente elevadas. Biológico es el uso de microbios o enzimas específicos para generar productos valiosos. La conversión termoquímica ocurre a temperatura elevada (y a veces presión) para la conversión. Los productos de las conversiones de biomasa pueden reemplazar los productos químicos comunes derivados de recursos fósiles (por ejemplo, ácido láctico), combustible (por ejemplo, diesel) y material (por ejemplo, yeso). Este capítulo se centra en la energía derivada de la bioconversión.
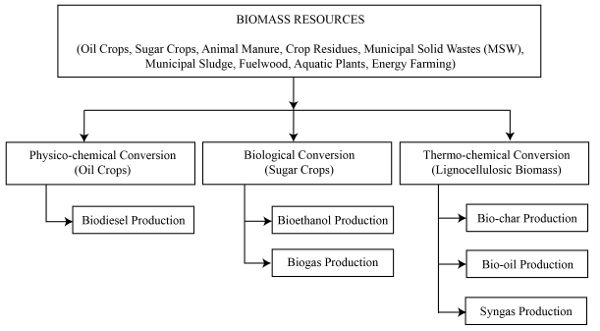
Producción de Biodiesel
Los aceites y grasas vegetales refinados se convierten en biodiesel, el cual es compatible con el combustible diesel, por conversión fisicoquímica usando un proceso catalítico simple usando metanol (CH 3 OH) e hidróxido de sodio (NaOH) a una temperatura ligeramente elevada. El proceso se llama transesterificación. Los aceites vegetales también se llaman triglicéridos porque su estructura química está compuesta por un glicerol unido a tres moléculas de ácidos grasos por enlaces éster. Cuando los enlaces éster son rotos por un catalizador, se produce glicerina y el compuesto de ácido graso se convierte en su forma de éster metílico, que es el término técnico para biodiesel. La combinación de metanol e hidróxido de sodio da como resultado un compuesto llamado metóxido de sodio (CH 3 ONa), que es el catalizador comercial más común para la producción de biodiesel. El balance de masa básico para el proceso es:
100 kg de aceite vegetal + 10 kg de catalizadores → 100 kg de biodiesel + 10 kg de glicerina
El balance energético depende del diseño específico de la instalación. Para que el producto biodiesel sea considerado viable, la energía en el biodiesel debe exceder la energía utilizada para producir el aceite vegetal utilizado para el proceso. En un sistema comercial, el proceso de transesterificación se divide en varias etapas (Figura1.1.2). El metanol y los catalizadores se recuperan después de todas las etapas para minimizar el consumo de catalizador. También se recupera glicerina cruda en cada etapa para minimizar el uso del exceso de metanol. El catalizador restante, la cantidad debe calcularse con precisión, se introduce luego en la última etapa del proceso. Esta reacción de última etapa minimiza los mono-glicéridos sin reaccionar (o glicerol restante que todavía tiene un ácido graso encadenado a él a través de un enlace éster). Si se usa aceite de soya, el producto biodiesel resultante se llama éster metílico de soja, el producto biodiesel más común en Estados Unidos. En Europa, el aceite de canola (colza) es la materia prima más común, que produce éster metílico de colza. El coproducto de glicerina se purifica adicionalmente para mejorar su valor comercial.
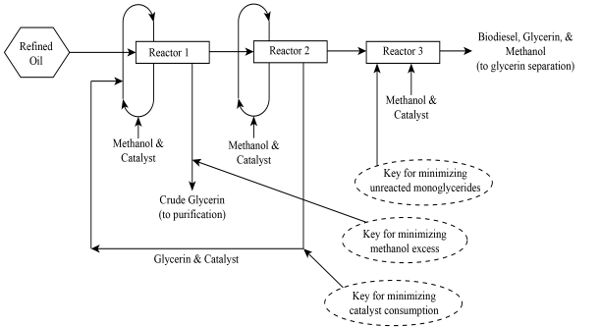
Producción de Bioetanol
El bioetanol, que es compatible con gasolina o gasolina, se produce a partir de cultivos de azúcar, almidón o lignocelulósicos utilizando microbios o enzimas. Los azúcares de los cultivos se convierten fácilmente en etanol usando levaduras (por ejemplo, Saccharomyces cerevisiae) u otros microbios similares, mientras que los cultivos con almidón necesitan enzimas (por ejemplo, amilasas) que conviertan el almidón en azúcar, actuando las levaduras sobre los azúcares para producir bioetanol. Los cultivos lignocelulósicos necesitan enzimas similares (por ejemplo, enzimas producidas por Trichoderma reesei) para descomponer la celulosa en azúcares simples. El balance de masa básico para la conversión de azúcares vegetales de biomasa en etanol (C 2 H 6 O) también produce calor:
C6H12O6+ yeast →2C2H6O+2CO2(+ heat )
La materia prima más común para elaborar bioetanol en Estados Unidos es el maíz molido en seco (maíz; Zea mays). En el proceso (Figura1.1.3), los granos de maíz secos se muele, luego se agrega agua al material en polvo mientras se calienta (o gelatiniza) para cocer el almidón y descomponerlo usando la enzima amilasa (sacarificación). Este proceso convierte el almidón en azúcares. El producto resultante (principalmente glucosa) se convierte luego en bioetanol usando fermentación de levaduras durante 3-5 días con un balance de masa de:
2C6H10O5+H2O+ amylase →C12H22O11
o
C12H22O11+H2O+ invertase →2C6H12O6
En esta representación, las moléculas complejas de almidón están representadas por unidades repetitivas de polímeros de glucosa [(C 6 H 10 O 5) n] siendo n cualquier número de cadenas. La enzima amilasa reduce este polímero en compuestos simples, como la sacarosa (C 12 H 22 O 11), un disacárido que tiene apenas dos moléculas de glucosa. Alternativamente, la enzima invertasa se usa para descomponer la sacarosa en azúcar de glucosa. Una levadura, como la levadura comercial Ethanol Red (distribuida por Fermentis de Lesaffre, Francia y vendida en todo el mundo) actúa sobre el producto azucarero para convertir el azúcar en bioetanol. El producto resultante (un caldo) se llama cerveza debido a que su contenido de alcohol es muy cercano al 10%. La porción sólida se llama grano de destiladores, que generalmente se seca y se alimenta a los animales. La cerveza se destila para producir sólidos (conocidos como fondos o fondos de alambique) y para recuperar 90-95% del bioetanol (usualmente 180-190 de prueba), que luego se purifica usando tamices moleculares. (Un tamiz molecular es una sustancia cristalina con poros de dimensiones moleculares cuidadosamente seleccionadas que permiten el paso de, en este caso, solo moléculas de etanol). El producto final separado y purificado puede entonces ser mezclado con gasolina o usado solo.
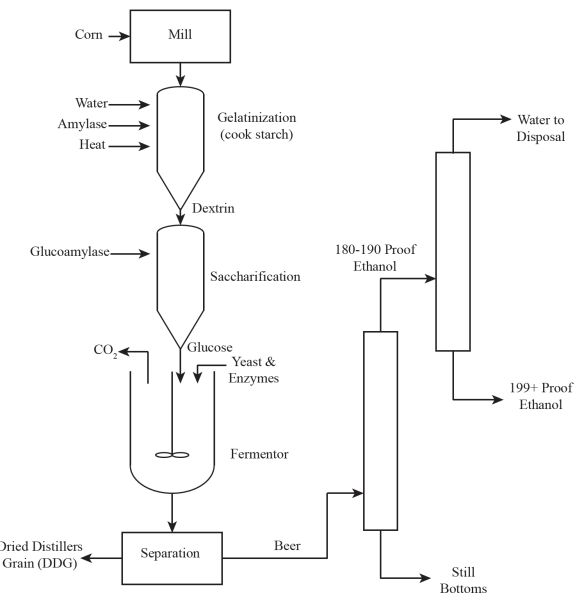
Producción de Biogás
El biogás, que está compuesto principalmente por metano (CH 4; también llamado gas natural) y dióxido de carbono (CO 2), es producido a partir de biomasa lignocelulósica por microbios en condiciones anaeróbicas. Los microbios adecuados se encuentran comúnmente en los estómagos de animales rumiantes (por ejemplo, vacas). Estos microbios convierten materiales celulósicos complejos en ácidos orgánicos mediante hidrólisis o fermentación; estos grandes ácidos orgánicos se convierten aún más en ácidos orgánicos más simples (por ejemplo, ácidos acéticos) y gas hidrógeno. El gas hidrógeno y algunos ácidos orgánicos que incluyen CO 2 se convierten posteriormente en CH 4 y CO 2 como gases respiratorios de estos microbios. El biogás (CO 2 + CH 4) es lo mismo que el gas natural (CH 4) si se elimina el componente CO 2. El gas natural es un combustible común derivado de la refinación de petróleo crudo.
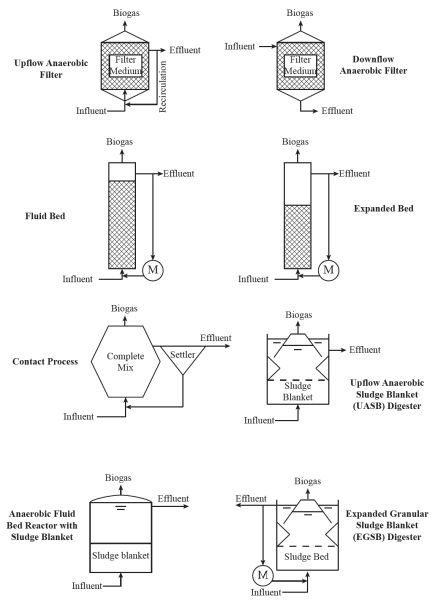
Existen diversos diseños de digestores anaerobios de alta tasa para la producción de biogás (Figura1.1.4), los cuales son comúnmente utilizados en plantas de tratamiento de aguas residuales a nivel mundial. Los digestores más simples utilizan filtros anaeróbicos de flujo ascendente y descendente, lechos fluidizados básicos, lechos expandidos y procesos de contacto anaeróbico. Un diseño popular de los Países Bajos es la manta de lodo anaeróbico de flujo ascendente (o UASB) (Letingga et al., 1980). Las mejoras a la UASB incluyen los diseños de reactores de lecho fluidizado anaeróbico y lecho expandido de manto de lodo granular. Los sistemas de alta tasa se encuentran comúnmente en Europa, pero hay pocos en Estados Unidos. La mayoría de las plantas de biogás en Estados Unidos son simplemente lagunas cubiertas.
Pirólisis de biomasa
La pirólisis es un proceso de conversión térmica a temperaturas elevadas en ausencia completa de oxígeno o un oxidante. La Figura 1.1.5 muestra las salidas y aplicaciones de pirólisis. Los productos primarios son bio-carbón sólido, líquido y gas de síntesis gaseoso. Las proporciones de estos coproductos dependen de la temperatura, el tiempo de retención y el tipo de biomasa utilizada. La calidad y magnitud de los productos también dependen del reactor utilizado. Las reglas simples de los procesos de pirólisis de biomasa son:
- 1. El rendimiento de biocarbón sólido (o carbón) se maximiza a la temperatura de pirólisis más baja y el tiempo de residencia más largo.
- 2. El rendimiento líquido generalmente se maximiza a temperaturas entre 400°C y 600°C.
- 3. El gas de síntesis, o gas de síntesis, se maximiza a la temperatura de funcionamiento más alta. Los principales componentes del gas de síntesis son el monóxido de carbono (CO) y el hidrógeno (H 2). Otros gases componentes incluyen hidrocarburos de bajo peso molecular como CH 4, etileno (C 2 H 4) y etano (C 2 H 6).
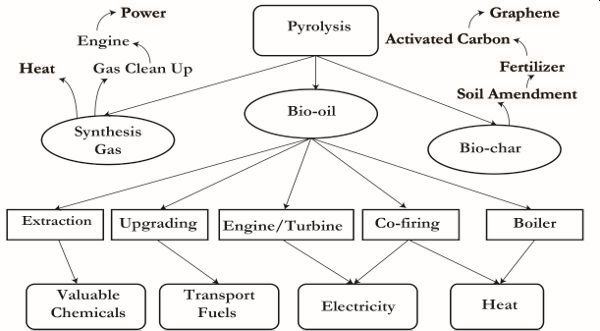
El biocarbón puede ser utilizado como una enmienda del suelo para proporcionar carbono y nutrientes cuando se aplica a tierras agrícolas. Un biocarbón alto en carbono también puede actualizarse en carbón activado, un material adsorbente de muy alto valor para los procesos de tratamiento de agua y aguas residuales. El valor más alto para el bio-carbón se logra cuando el carbono se purifica de todos los inorgánicos para generar productos de grafeno, que se encuentran entre los materiales más duros hechos de carbono.
La calidad del producto líquido (biooil) se mejora o mejora con tiempos de residencia cortos como los de los sistemas de pirólisis de lecho fluidizado pero no con los pirolizadores de barrena. Los pirolizadores de barrena suelen tener largos tiempos de residencia. Los cortos tiempos de residencia dan lugar a bioaceite menos viscoso que es fácil de actualizar a biocombustible (gasolina o diesel) usando catalizadores. El bio-aceite del proceso de pirólisis tiene una amplia gama de aplicaciones (Figura1.1.5). Se pueden extraer productos químicos valiosos; el bioaceite inalterado se puede actualizar mediante procesos catalíticos para generar combustibles de transporte; y puede coencenderse en un motor para generar electricidad o en una caldera para generar calor.
El gas de síntesis puede simplemente quemarse ya que se produce para generar calor. Sin embargo, el gas de síntesis puede necesitar ser limpiado de alquitrán antes de su uso en un motor de combustión interna. Para generar energía eléctrica, este motor de combustión interna se acopla con un generador.
Gasificación de biomasa
La gasificación es una conversión térmica parcial de biomasa para producir gas de síntesis. En los libros de texto más antiguos, este gas también es sinónimo de “gas productor”. El gas de síntesis puede quemarse para generar calor o limpiarse de alquitrán y usarse en un motor de combustión interna para generar electricidad. El gas de síntesis también se puede usar como materia prima para producir bio-butanol usando microbios que también producen coproductos biocombustibles. Existen numerosos tipos y diseños de gasificadores, incluyendo sistemas de lecho fijo (gasificadores de corriente ascendente, corriente descendente o tiro cruzado) y sistemas de lecho móvil (sistemas de gasificación de lecho fluidizado).
Un sistema de gasificación de lecho fluidizado se muestra en la Figura1.1.6. La biomasa se alimenta continuamente a un contenedor grande de biomasa. El reactor de lecho fluidizado contiene un material de lecho, generalmente arena refractaria, para transportar el calor necesario para la reacción. La relación aire-combustible se controla de manera que la cantidad de aire esté por debajo del requisito estequiométrico para la combustión (es decir, la combustión es incompleta) para asegurar la producción de gas de síntesis en lugar de calor y vapor de agua. El sólido que queda después de la conversión térmica parcial es bio-carbón de alto contenido de carbono que se elimina a través de una serie de ciclones. La aplicación más sencilla de este sistema es la producción de calor mediante la combustión del gas de síntesis. Si se necesita energía eléctrica, entonces el gas de síntesis debe limpiarse de alquitrán para ser utilizado en un motor de combustión interna para generar electricidad. Las eficiencias de conversión de los sistemas de gasificación son típicamente menores del 20%. Un valor promedio para usar para una estimación rápida de la producción es de alrededor del 15% de eficiencia de conversión general.
Combustión de biomasa
La combustión directa de biomasa ha sido una práctica tradicional durante siglos; quemar leña para producir calor para cocinar es un ejemplo. La combustión es el proceso de conversión térmica más eficiente para fines de generación de calor y energía. Sin embargo, no muchos productos de biomasa pueden quemarse debido al alto contenido de cenizas y agua de la mayoría de los productos de biomasa agrícola. El componente de ceniza puede fundirse a temperaturas de combustión más altas, lo que resulta en fenómenos llamados escoria y ensuciamiento. La ceniza fundida forma escoria que se acumula en las superficies transportadoras (incrustaciones) a medida que se enfría.
Evaluación Económica de Sistemas de Bioenergía
Las instalaciones comerciales de bioenergía se deprecian cada año. No existe una estimación precisa de los valores de depreciación, pero un posible inversionista puede utilizar este parámetro para ahorrar en costos de capital cada año a partir de los ingresos de la instalación comercial de tal manera que al final de la vida útil de la instalación, el inversionista esté preparado para invertir en proyectos de mayor rendimiento.
Hay una serie de métodos simples que los ingenieros pueden utilizar para los análisis de depreciación económica de las instalaciones de bioenergía. Se requiere una evaluación económica básica al inicio del diseño del sistema para determinar la viabilidad previa a una inversión significativa de capital. La evaluación de la factibilidad económica comienza con el análisis de los gastos fijos (o de capital) y los costos variables (u operativos) (Watts y Hertvik, 2018). Los gastos fijos incluyen el costo de capital de los activos como instalaciones de conversión de biomasa, terrenos, equipos y vehículos, así como la depreciación de instalaciones y equipos, impuestos, vivienda, seguros e intereses sobre el dinero prestado. Los costos variables son los costos operativos diarios o mensuales para la producción de un producto de biomasa. Los costos variables están asociados con materia prima y productos químicos, reparación y mantenimiento, agua, combustible, servicios públicos, energía, mano de obra, manejo y eliminación de desechos. La figura1.1.7 muestra la relación entre estos dos parámetros económicos básicos. Los costos fijos no varían con el tiempo y la producción, mientras que los costos variables aumentan con el tiempo y la producción del producto. El costo total del proyecto es la suma de los costos fijos y variables. Los costos variables por unidad de producción disminuyen con el aumento de la cantidad de producción, por lo que la rentabilidad de un producto puede depender de la cantidad producida.
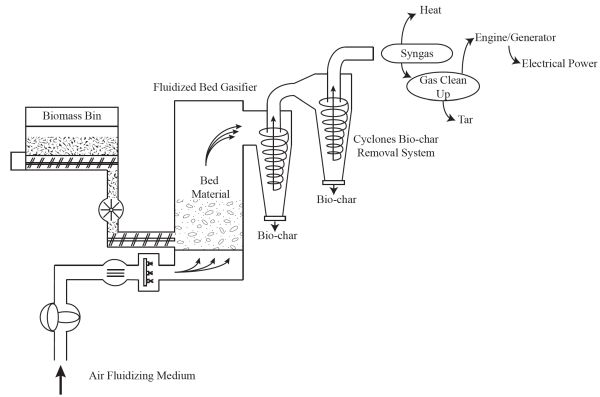
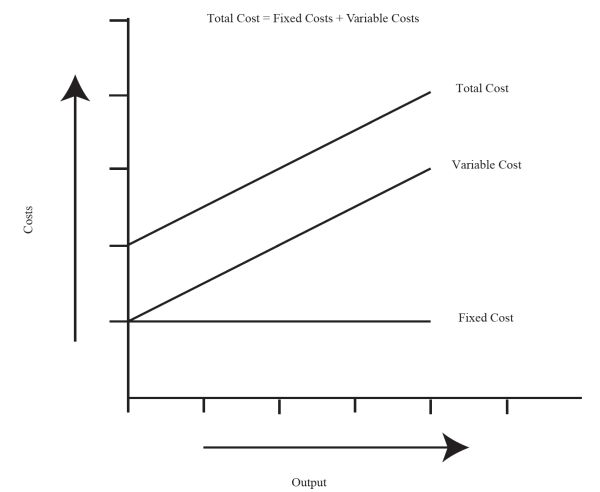
Para evaluar los beneficios económicos de un proyecto de bioenergía, se utilizan comúnmente algunos otros parámetros económicos (Stout, 1984), incluyendo el valor presente neto; relación costo beneficio, período de recuperación, análisis de punto de equilibrio y tasa interna de retorno. Los análisis deben tomar en cuenta la relación entre el tiempo y el valor del dinero. Las ecuaciones básicas para estimar el valor presente y futuro de las inversiones son:
Present Value =PV=FV×1(1+R)n
Future Value =FV=PV×(1+R)n
donde R = tasa de retorno o tasa de descuento (decimal)
n = número de periodos (sin unidades)
La tasa interna de rendimiento es una tasa descontada que hace que el valor presente neto de todos los flujos de efectivo de un proyecto en particular sea igual a cero. Cuanto mayor sea la tasa interna de retorno, más deseable económicamente será el proyecto. El valor actual neto (Ecuación 1.1.4) es la diferencia entre el valor actual de las entradas de efectivo y el valor actual de las salidas de efectivo. Un valor presente neto positivo significa que las ganancias del proyecto superan los costos anticipados. La relación costo beneficio (Ecuación 1.1.5) es la relación entre los beneficios del proyecto y los costos. Son deseables valores mayores a 1. El periodo de amortización (Ecuación 1.1.6) es el tiempo requerido para recuperar el costo de la inversión.
Al estimar el costo fijo de un proyecto, los componentes principales del costo son la depreciación y el interés sobre el dinero prestado. Hay muchas maneras de estimar la depreciación de una instalación. Los dos métodos más comunes y simples son la depreciación lineal (Ecuación 1.1.7) y el método de depreciación de dígitos de suma de años (SYD) (Ecuación 1.1.8).
Straight Line Depreciation ($)= Principal-Salvage Value Life of Unit
SYD Depreciation($) = Depreciation Base × Remaining Useful Life Sum of Years' Digits
En la Ecuación 1.1.8, la base de depreciación es la diferencia entre el costo de capital inicial ($) y el valor de salvamento del activo ($). La suma de los dígitos del año es la serie suma: 1, 2, 3, hasta n, donde n es la vida útil del activo en años, como se muestra en la Ecuación 1.1.9:
Sum of Years' Digits =SYD=n(n+1)2
La otra gran parte del costo de capital son los intereses sobre el dinero prestado. Este suele ser el porcentaje (tasa de interés) que cobra el banco con base en el monto del préstamo. La ecuación gobernante sin incluir el valor de salvamento (Ecuación 1.1.10) es similar al cálculo de amortización para un monto de préstamo:
Annuity =A=P×(r×(1+r)n(1+r)n−1)
donde
A = anualidad o monto de pago por periodo ($)
P = capital inicial o monto del préstamo ($)
r = tasa de interés por periodo (%)
n = número total de pagos o periodo (sin unidades)
Existen muchas herramientas utilizadas para la evaluación económica del sistema energético, pero una de las más populares es el HOMER Pro (o modelo híbrido de optimización para la renovación energética) desarrollado por Peter Lilienthal del Departamento de Energía de Estados Unidos (USDOE) desde 1993 (Lilienthal y Lambert, 2011). El modelo incluye análisis y optimización de sistemas para sistemas de energía conectados fuera de la red para aplicaciones de generación remota, autónoma y distribuida de energías renovables. Cuenta con tres potentes herramientas para simulación de sistemas energéticos, optimización y análisis de sensibilidad económica (Capareda, 2014). El software combina aspectos de ingeniería y economía de los sistemas energéticos. Este tipo de herramienta se utiliza para la planeación y diseño de sistemas comerciales, pero sus ecuaciones simples se pueden utilizar primero para evaluar la viabilidad fundamental de un proyecto de conversión de biomasa.
Temas de sustentabilidad en sistemas de conversión energética de biomasa
El Departamento de Energía de Estados Unidos (USDOE) y el Departamento de Agricultura de Estados Unidos (USDA) definen a los biocombustibles sustentables como aquellos que son “económicamente competitivos, conservan la base de recursos naturales y aseguran el bienestar social”. La conservación de la base de recursos apunta también a la conservación de la energía, es decir, el combustible producido debe tener más energía que la energía total utilizada para producir el combustible. Uno de los indicadores más comunes de sustentabilidad para la utilización de biomasa es el uso de energía a lo largo del ciclo de vida de la producción. Para esta evaluación se utilizan dos medidas: la relación energética neta (NER) (Ecuación 1.1.11) y el balance energético neto (NEB) (Ecuación 1.1.12). La NER debe ser mayor a 1 y la NEB debe ser positiva para que el sistema sea considerado sustentable desde una perspectiva energética.
NER= Energy Content of Fuel (MJ) Energy Required to Produce the Biofuel (MJ)
El valor calorífico del biocombustible se define como la cantidad de calor producido por la combustión completa del combustible medida como una unidad de energía por unidad de masa.
Aplicaciones
Los ingenieros asignados para diseñar, operar y administrar una planta comercial de biodiesel deben decidir qué sistema de trabajo adoptar. El más barato y más común es el uso de la gravedad para separar el biodiesel (generalmente la capa superior) y la glicerina (la capa inferior). Un ejemplo de esta instalación operativa comercial es la planta de biodiésel de 3 millones de galones anuales (MGY) (11.36 ml/año) en Dayton, Texas, operada por AgriBioFuels, LLC. Esta instalación comenzó a operar en 2006 y aún está en funcionamiento. La recuperación de biodiesel para esta instalación es ligeramente inferior a la de los sistemas de separación avanzados controlados por computadora que utilizan centrífugas. Esta instalación tampoco está siguiendo el flujo de proceso ideal (mostrado en la Figura 1.1.2) utilizado por muchas otras instalaciones comerciales. Así, uno esperaría que su eficiencia de conversión y recuperación de biodiesel fueran menores.
La producción de biodiesel es un proceso eficiente de conversión de biomasa. La ecuación ideal del balance de masas, presentada anteriormente, es:
100 kg de aceite vegetal + 10 kg de catalizadores → 100 kg de biodiesel + 10 kg de glicerina
La relación muestra que se produce una masa equivalente de biodiesel por cada masa unitaria de aceite vegetal utilizado, pero hay pérdidas en el camino y los ingenieros deben considerar estas pérdidas al diseñar instalaciones comerciales. En una instalación comercial de biodiesel, el proceso de transesterificación se divide en varios reactores (por ejemplo, Figura1.1.2). Sin embargo, para ahorrar en costos de capital, algunos gerentes de planta simplemente dividen el proceso en dos etapas. Separar la glicerina y el combustible biodiesel también es un tema al que se enfrentará el ingeniero. Los sistemas de separación eficientes que utilizan centrífugas son costosos en comparación con la separación física, y esto afecta la economía general de la instalación. Si el capital inicial disponible es limitado, los inversionistas normalmente optarán por una separación de gravedad física más barata en lugar de usar centrifugadoras. Crown Iron Works (en Blaine, MN) vende instalaciones de biodiesel de bajo costo que emplean separación por gravedad, mientras que GEA Wesfalia (Oelde, Alemania) vende instalaciones de biodiesel más caras que utilizan separación por centrífuga. Este último sistema, costoso, es más eficiente en la separación de glicerina y combustible biodiesel y puede ser beneficioso a largo plazo, permitiendo que la instalación venda productos de glicerina con mínima contaminación. El ingeniero podrá comparar estos sistemas en términos de costos y eficiencias. En última instancia, la Ecuación 1.1.2 se utiliza para diseñar y dimensionar una planta comercial para determinar el requerimiento diario, mensual o anual de aceite vegetal. Esto significa que el ingeniero debe determinar la superficie de tierra agrícola requerida tanto para la instalación como para el suministro de biomasa. Hay tablas estándar de rendimientos de aceite de los cultivos que se utilizan. Por ejemplo, el mayor rendimiento de aceite proviene de los aceites de palma, con más de 7,018 kg de producción de aceite por hectárea en comparación con 2,245 kg/ha para el aceite de soya (Capareda, 2014).
Diseñar, construir y operar una instalación comercial de bioetanol también requiere conocimiento principalmente sobre el tipo de materia prima a usar. A diferencia de una planta de biodiesel, donde el gerente puede tener varias opciones para usar numerosos tipos de aceite vegetal sin cambiar el diseño, una planta de bioetanol está bastante limitada al uso de una materia prima específica. Las principales opciones son los cultivos de azúcar, los cultivos con almidón o la biomasa lignocelulósica. Los diseños para estos tres tipos diferentes de materia prima no son los mismos; el uso de biomasa lignocelulósica como materia prima es el más complejo. Los más simples son los cultivos de azúcar pero el jugo azucarado se degrada muy rápidamente y así la mayoría de las plantas de bioetanol que operan comercialmente en Estados Unidos utilizan cultivos con almidón como el maíz. Los granos de maíz se pueden secar, moler y almacenar en sacos para una conversión futura sin perder su potencia. Ejemplos de plantas comerciales de bioetanol que utilizan materias primas lignocelulósicas son las construidas por POET (Sioux Falls, Dakota del Sur) en Emmetsburg, Iowa, usando mazorcas de maíz (25 MGY o 94.6 ml/año), y otra por Dupont (Wilmington, Delaware) en Nevada, Iowa, usando rastrojo de maíz (30 MGY o 113.6 ml/año).
El bioetanol es un producto biocombustible eficiente. Los ingenieros deben estar al tanto de los balances de energía y masa requeridos para la producción de biocombustibles aunque también se utilicen otros materiales de desecho para los procesos. Como los rendimientos potenciales de bioetanol de los cultivos varían, el diseño es para una materia prima específica. El mayor rendimiento potencial de bioetanol proviene de la alcachofa de Jerusalén (Helianthus tuberosus) (11,219 L/ha). Compare esto con maíz (maíz, Zea mays) con un rendimiento reportado de solo 2,001 L/ha (Capareda, 2014) y sorgo (sorgo spp.) caña (4,674 L/ha) o grano (1,169 L/ha).
Si bien los rendimientos son importantes, la ubicación de un proyecto también es un factor significativo para seleccionar el insumo de recursos para una instalación de producción de bioetanol o biodiesel. Por ejemplo, la alcachofa de Jerusalén tiene el mayor rendimiento de bioetanol pero solo crece en condiciones templadas. Cuando el negocio del bioetanol comenzó a auge en EU alrededor de 2013, hubo un problema con la disposición de un subproducto del proceso, el grano de destiladores. Durante esos períodos iniciales, estos coproductos simplemente se desecharon con un procesamiento secundario muy mínimo (por ejemplo, pienso para animales) o a un relleno sanitario. Ahora han surgido opciones de valorización secundaria (es decir, para mejorar el precio o valor de un producto primario) como una mayor recuperación de energía y como materia prima para productos como películas y membranas. Los temas clave para los ingenieros incluyen el dimensionamiento de las plantas y la determinación de los requerimientos de recursos diarios, semanales y mensuales para la materia prima, los cuales pueden calcularse usando las Ecuaciones 1.1.3, 1.1.4 y 1.1.5, modificadas por ineficiencia en la práctica.
Un número creciente de instalaciones animales han aprovechado la energía adicional recuperada de la digestión anaeróbica del estiércol al convertir sus lagunas en instalaciones de producción de biogás. En EU, la laguna cubierta sigue siendo el diseño predominante del digestor de biogás. La operación es muy sencilla ya que los microorganismos necesarios para la producción de biogás ya existen en los estómagos de los rumiantes. Los temas clave para los ingenieros son el dimensionamiento (basado en números de animales), las tasas de recuperación de energía, el dimensionamiento de las instalaciones de producción de energía (motor), la producción de lodos y la energía restante en el lodo y Existe un interés creciente en diseñar sistemas que utilicen lodos para pirólisis para recuperar la mayor cantidad de energía posible de la materia prima. Cuando se adoptan estos procesos adicionales, se mejora la recuperación de energía de la biomasa residual y hay menos residuos globales. Si bien el lodo es una excelente fuente de nutrientes para los cultivos, su valor energético debe ser juzgado contra su valor fertilizante. Financieramente el caso energético probablemente gane, pero sería necesario un análisis holístico para juzgar la opción más deseable desde una perspectiva de sustentabilidad.
La economía de una instalación de biocombustibles depende del precio de la materia prima inicial utilizada. Por ejemplo, 85% del costo de producción de combustible biodiesel proviene del costo de la materia prima inicial. Como candidato potencial para la producción de biodiesel, si el precio del aceite vegetal refinado es el mismo que el precio del combustible diesel, no es económico convertir el aceite vegetal en un biocombustible. El 15% restante suele ser el costo de los catalizadores utilizados para el proceso de conversión (Capareda, 2014). Si el biodiesel está hecho de cualquier aceite vegetal refinado, el costo de procesamiento es el mayor componente del proceso de conversión. El costo de los químicos y catalizadores juntos generalmente asciende a aproximadamente $0.06/L ($0.22/gal). Los químicos o catalizadores no son los factores limitantes en la fabricación de biodiesel. Esta declaración se aplica a los biocombustibles en general. Estos gastos de producción no son una gran parte del gasto de producción de biocombustibles. Los catalizadores de biodiesel son bastante baratos y abundantes. Por lo general, no se agotan ni se ponen demasiado caros a medida que aumenta la producción.
En el proceso de producción de bioetanol, el costo del combustible de bioetanol también se ve afectado principalmente por el precio de la materia prima inicial utilizada, como el maíz, así como las enzimas utilizadas para el proceso. El proceso también utiliza volúmenes significativos de agua, pero solo electricidad mínima. Por ejemplo, por cada 3.785 L (1 galón) de bioetanol producido, se requieren 1.98 m 3 (70 ft 3) de gas natural y 155.5 L (41 gal) de agua (Capareda, 2014). El consumo de electricidad es de alrededor de 0.185 kWh/l (0.7 kWh/gal). De ahí que si el costo de la electricidad es de $0.10/kWh, entonces uno solo gastaría alrededor de $0.0158/L (0.07/gal). El gas natural se utiliza para calentar la cerveza y recuperar el bioetanol puro. Debido al uso abundante de agua, este aporte de agua debe reciclarse para que el proceso sea efectivo y eficiente. El estándar actual de la industria para la producción de bioetanol a partir de granos es de alrededor de 416.4 a 431.2 L/tonelada (2.8—2.9 gal/bushel). Las nuevas materias primas para la producción de bioetanol deben superar este valor.
La economía de la producción de energía a través de la conversión térmica, como la pirólisis o la gasificación, depende de la venta de energía eléctrica. Si una planta de energía MW que utiliza biomasa se opera continuamente durante un año, la energía eléctrica debería venderse por $0.12/kWh para lograr un ingreso bruto de $1M. Una evaluación económica preliminar del rendimiento económico de una gasificación para instalaciones eléctricas se puede completar ajustando el costo de venta. Finalmente, la economía de la producción de biocombustibles a partir de recursos de biomasa también depende del precio del petróleo crudo de distribuidores e importadores comerciales. El biodiesel y el bioetanol se mezclan con diesel y gasolina comerciales y tienen un precio similar. Con un precio del petróleo crudo por debajo de 100 dólares/barril, el costo de producción de biodiesel y bioetanol también debe ser inferior a 100 dólares/barril.
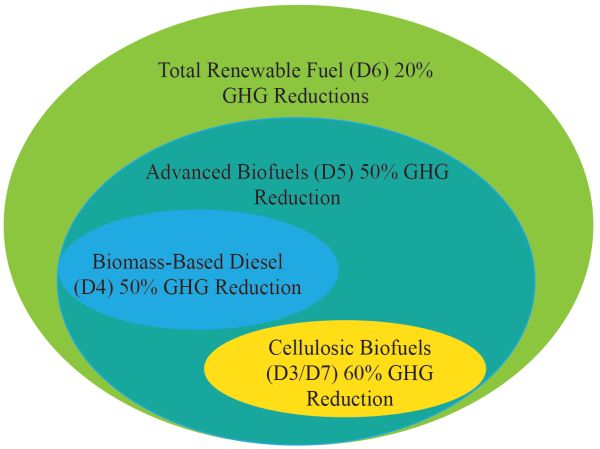
Se debe abordar la cuestión de la sustentabilidad de la producción y el uso de combustibles. Muchos biocombustibles producidos a partir de recursos de biomasa en Estados Unidos ahora se están categorizando de acuerdo con sus posibles reducciones de gases de efecto invernadero y están estandarizados bajo las categorías del estándar de combustibles renovables (RFS) (Figura1.1.8). Como se muestra, los biocombustibles celulósicos, principalmente bioetanol y biodiesel (también codificados como D3/D7, respectivamente) provenientes de biomasa lignocelulósica, tienen una reducción reportada de 60% de gases de efecto invernadero en comparación con el diesel basado en biomasa, que solo tiene un potencial de reducción de gases de efecto invernadero de 50% (también codificado como D4). El biodiesel de aceites vegetales y el etanol del maíz tienen un menor potencial de reducción de GEI que los biocombustibles celulósicos y el diesel a base de biomasa. El código D6 es para combustibles renovables en general, producidos a partir de biomasa renovable y se utiliza para reemplazar la cantidad de combustible fósil presente en el combustible de transporte, combustible para calefacción o combustible para aviones (por ejemplo, etanol de maíz) y tampoco se incluye en ninguna de las otras categorías. El código D5 es para biocombustibles avanzados distintos al etanol derivado del almidón de maíz (etanol de caña de azúcar) y biogás de otros digestores de desechos.
Si bien la relación energética neta (NER) y el balance energético neto (NEB) son importantes, tienen que combinarse con estimaciones de las emisiones de CO 2 y quizás con el uso del suelo para comprender los fundamentos de la sustentabilidad del uso de los recursos de biomasa. Una simple evaluación del ciclo de vida (ACV) de carbón y biomasa para la generación de energía (Mann y Spath, 1999) reportó 1,022 g de emisiones de CO 2 por kWh de energía eléctrica producida por carbón en comparación con solo 46 g CO 2/kWh de energía eléctrica por biomasa. Contrariamente a la percepción de que el uso de biomasa tendría cero emisiones netas de CO 2, en realidad hay algo de CO 2 producido por cada kWh de electricidad generada. También es importante reconocer los usos competitivos de la tierra y la biomasa por parte de la sociedad (Figura1.1.9). Por un lado, la biomasa se utiliza para alimentos y piensos (la cadena alimentaria), y por otro para materiales y energía (la bioeconomía). Todos los usos tienen que considerar el cambio climático, la seguridad alimentaria, el agotamiento de los recursos y la seguridad energética. Los países de todo el mundo necesitan crear un equilibrio del uso de los recursos de biomasa hacia un mejor ambiente. Los futuros ingenieros deben ser capaces de evaluar el uso de los recursos de biomasa para la producción de materiales y biocombustibles, así como relacionarlo con el cambio climático y la seguridad energética sin agotar recursos ya limitados.
El Departamento de Energía de Estados Unidos creó una jerarquía de materiales y productos a partir de recursos de biomasa (Figura1.1.10). En la parte superior de la pirámide se encuentran los productos químicos finos de alto valor, como la vainillina y los derivados de fenol, con un valor superior a $6,500 por tonelada. Los derivados de fenol tienen el potencial de convertirse aún más en lubricantes caros (Maglinao et al., 2019). A continuación están las fibras de carbono de alto valor como el grafeno, seguidas de sustancias fenólicas. También hay nuevos productos como placas de circuito integrado 100% basadas en biomasa desarrolladas por IBM (International Business Machines Corporation, Armonk, NY). Los biocombustibles se encuentran en medio de la pirámide, valorados en torno a los 650 dólares por tonelada, con una simple recuperación de energía por combustión en la parte inferior.
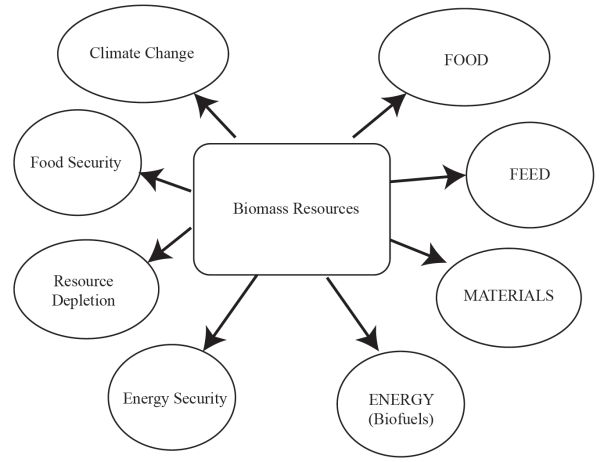
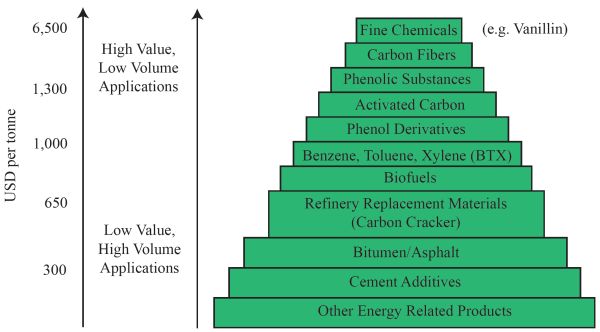
Ejemplos
Los ingenieros que administran biorrefinerías deben estar al tanto de los balances de energía y masa para determinar las asignaciones de recursos, así como las eficiencias de conversión para mejorar las operaciones de la planta. El proceso de estimación incluye cálculos simples de eficiencia de conversión y determinación de la viabilidad económica de la biorrefinería.
Ejemplo1.1.1
Ejemplo 1: Cálculos de eficiencia de conversión
Problema:
El equilibrio ideal de masa y energía es difícil de lograr. Los gerentes de planta deben poder estimar qué tan cerca están sus operaciones comparadas con las condiciones ideales. El problema más común que enfrenta un gerente de planta es determinar la eficiencia de conversión del aceite vegetal refinado en biodiesel. Este ejemplo muestra cómo se opera la planta real y qué tan cerca está del balance de masa ideal. El contenido energético del aceite de canola refinado es de 39.46 MJ/kg y el del biodiesel de aceite de canola se midió en el laboratorio para ser 40.45 MJ/kg. Durante una ejecución real, solo alrededor del 95% de biodiesel se produce a partir de este aporte de aceite de canola refinado en lugar del rendimiento masivo ideal del 100%.
Determinar la eficiencia de conversión de energía de esta instalación a partir de convertir la energía del aceite de canola refinado en energía de combustible en biodiesel.
Solución
- 1. La energía de la unidad de peso del producto biodiesel de salida se calcula utilizando el rendimiento másico del 95% del biodiesel de la siguiente manera:
- Biodiesel Output (MJ)=40.45MJkg×0.95 kg Biodiesel =38.43MJ=36,424Btu
- 2. Usando la Ecuación 1.1.1, la eficiencia de conversión por unidad de peso es:
- Conversion Efficiency (%)=38.43MJ39.46MJ×100%=97.4%
La producción de biodiesel es quizás una de las vías más eficientes para la conversión del aceite vegetal en biocombustible, teniendo una eficiencia de conversión energética muy cercana al 100%.
Ejemplo1.1.2
Ejemplo 2: Dimensionamiento de plantas comerciales de biodiesel
Problema:
Planear construir una instalación comercial de biodiesel requiere realizar un inventario de los recursos de insumos necesarios. En este ejemplo, el ingeniero debe determinar la cantidad de aceite de soya necesario (L/año) para construir y operar una planta de biodiésel de 3.785 millones de litros (1 millón de galones por año, MGY). Las densidades del aceite de soja y su biodiesel equivalente (también llamado éster metílico de soja) son las siguientes:
Calcular los requerimientos de aceite de soya diariamente y mensualmente.
Solución
- 1. 3.785 millones de litros de producto biodiesel se convierten en sus unidades de masa como:
- Biodiesel Mass Requirement ( tonnes year )=3.785×106 L year ×0.88kgL× tonne 1000 kg=3330.8 tonnes year =3,671.6 tonnes year
- 2. Esta masa de biodiesel de 3,330.8 toneladas anuales es entonces equivalente a la masa de aceite de soya requerida para la planta. Esta unidad debe ser convertida en unidades volumétricas para el comercio de aceites vegetales, como:
- Soybean Oil Volume Requirement(L year )=3,330.8 tonnes year ×1,000 kg1 tonne ×L0.917 kg=3,632,279L year =959,651 gallons year
- 3. Así, el requerimiento anual de aceite de soya para esta instalación de biodiesel es de más de 3.6 millones de litros (0.96 millones de galones). Los requerimientos mensuales y diarios se calculan como:
- Soybean Oil Mass Requirement (L month )=3,632,279 L year ×1 year 12 months =302,689L month =79,971 gallons month
Además, este valor de requerimiento de aceite de soya también se puede utilizar para estimar la superficie requerida para el aceite de soya si se tienen datos sobre el rendimiento del cultivo de aceite de soya por acre. Por ejemplo, un rendimiento reportado de aceite de soya de alrededor de 2,245 kg/ha (2000 lb/acre) (Capareda, 2014) resultará en un estimado de 1,483.6 ha (3,664 ac) necesarias para terrenos de soya dedicados para este uso de plantas durante todo el año.
Ejemplo1.1.3
Ejemplo 3: Balance energético en la recuperación de bioetanol
Problema:
El bioetanol se puede producir a partir de sorgo dulce a través de la fermentación de sus azúcares. El jugo de sorgo dulce se fermenta utilizando levaduras (Saccharomyces cerevisiae). El producto fermentado resultante, llamado cerveza, tiene alrededor de 10% de bioetanol. Se requiere un mayor porcentaje de etanol para el uso del motor y puede separarse de este producto fermentado a través de un simple proceso de destilación. El producto fermentado líquido simplemente se calienta hasta que se evapora el vapor de bioetanol (alrededor de 80°C, la temperatura de evaporación del etanol puro) y este vapor se condensa o licua en un condensador simple. En los sistemas a nivel de pueblo, la madera combustible se utiliza para calentar la caldera donde se coloca el material fermentado.
Un esquema de producción de etanol a nivel de pueblo basado en sorgo dulce tiene los siguientes datos para una serie de experimentos. En el primer experimento, el operador no estuvo consciente de la cantidad de madera combustible utilizada para la recuperación de etanol altamente concentrado y utilizó demasiado, alrededor de 20 kg de madera combustible residual para la caldera. Además, la caldera no se aisló durante esta ejecución. En el segundo experimento, el operador aisló la caldera y fue muy cuidadoso en el uso de leña para ajustar la temperatura de la caldera por debajo del punto de ebullición del etanol puro. Sólo se utilizaron alrededor de 10 kg de madera combustible, aproximadamente la mitad del experimento inicial. Supongamos que la energía de la madera combustible es de 20 MJ/kg y el valor calorífico del etanol es de alrededor de 18 MJ/L, en ambos experimentos se utilizaron 120 litros de material fermentado líquido (cerveza) y se recuperaron 13 litros de etanol altamente concentrado. Discutir el balance energético de cada experimento.
Solución
- 1. En el primer experimento, el operador utilizó alrededor de 400 MJ de energía de entrada y produjo 13 litros de etanol con un contenido energético de 234 MJ:
- Energy from the Fuel Wood =20 kg fuel wood ×20MJkg=400MJ
- Energy from the Ethanol =13 L×18MJL=234MJ
- Claramente, el operador utilizó más energía de la madera combustible que la del etanol recuperado, demostrando un proceso insustentable.
- 2. El segundo experimento utilizó solo alrededor de 200 MJ de energía de entrada de madera, la cual es ligeramente menor que la energía del etanol producido de 234 MJ.
- Energy from the Fuel Wood =10 kg fuel wood 20MJkg=200MJ
- Mediante el uso cuidadoso de la madera combustible, se recupera más energía del bioetanol de un proceso de recuperación relativamente eficiente.
Tenga en cuenta que hay otras cantidades de energía gastadas de la siembra, cosecha y transporte de la materia prima de sorgo dulce y este experimento es solo una porción del ciclo de vida de la producción, recuperación y uso de bioetanol.
Ejemplo1.1.4
Ejemplo 4: Producción y uso de biogás a partir de estiércol animal
Problema:
El dimensionamiento de una instalación de biogás es una tarea asignada a un ingeniero que opera una instalación comercial de biogás. Un cálculo común es determinar la energía eléctrica producida a partir del estiércol recolectado en una instalación lechera de 500 cabezas. Por lo general, uno necesitaría energía eléctrica durante 8 horas al día. La eficiencia de conversión térmica de un motor de combustión interna es de aproximadamente 25% con una eficiencia de conversión mecánica a eléctrica de 80%. Se encontró que el rendimiento específico de metano fue de 0.23 m 3 biogas/kg de sólidos volátiles por día (Hamilton, 2012; Norma ASABE D384.2). Cada vaca lechera madura produce un promedio de 68 kg de estiércol por cabeza por día con un porcentaje de 7.5 sólidos volátiles. El contenido energético del biogás fue de 24.2 MJ/m 3 (650 BTU/ft 3).
Dimensionar el generador a utilizar para esta instalación.
Solución
- 1. La cantidad de metano producida en una instalación de 500 cabezas se calcula de la siguiente manera:
- Biogas (m3 day )=500 head ×68 kg wet manure head per day ×0.075 kgVSkg wet manure ×0.23 m3 biogas kgVS=586.5m3 day
- 2. La producción teórica de potencia se calcula de la siguiente manera:
- Power (kW)=586.5 m3 day ×1 day 8hrs×24,200 kJ m3×1hr3600 s×kWkJ/s=492.8 kW
- 3. La potencia real producida en base a 25% de eficiencia del motor y 80% de eficiencia mecánica a eléctrica se calcula de la siguiente manera:
- Actual Power (kW)=492.8 kW×0.25×0.80=98.6 kW
Se requerirá un generador con un tamaño cercano a los 100 kW de potencia de salida.
Ejemplo1.1.5
Ejemplo 5: Balances básicos de energía y masa de pirólisis de biomasa
Problema:
La conversión térmica de la biomasa residual en energía útil es un cálculo común para un ingeniero. Este sencillo ejemplo es la conversión de la cáscara de coco (biomasa residual) en bio-carbón (combustible útil). En el experimento, el ingeniero utilizó 1 kg de cáscara de coco y la pirolizó a una temperatura de 300°C, el contenido de energía medido de esta biomasa de alta densidad energética fue de 20.6 MJ/kg. El experimento de pirólisis produjo alrededor de 0.80 kg de bio-carbón. El valor calorífico del bio-carbón se midió para ser 22 MJ/kg. Se produjeron mínimos sólidos y productos gaseosos en este proceso de pirólisis a baja temperatura. Determinar la eficiencia de conversión general (η e) para el proceso de conversión de bio-carbón y también calcular la cantidad de energía retenida en el bio-carbón y la energía perdida a través del proceso.
Solución
- 1. La ecuación 1.1.1 se utiliza directamente para estimar la eficiencia de conversión para la producción de bio-carbón.
- Energy Conversion Efficiency (%)= Energy Output (MJ) Energy Input (MJ)×100%(Ecuación1.1.1)
- Primero, calcular la energía total del bio-carbón por unidad kg de material pirolizado como:
- Bio-char Energy (MJ)=0.80 kg×22MJkg=17.6MJ
- 2. La eficiencia de conversión global (η e) se calcula entonces de la siguiente manera:
- ηe=17.6MJ20.6MJ×100%=85.4%
- Este valor también indica el porcentaje de energía retenida en el bio-carbón.
- 3. La energía perdida a través del proceso es simplemente la diferencia entre la energía original de la biomasa y la energía retenida en el bio-carbón de la siguiente manera:
- Energy Loss(MJ)=20.6MJ−17.6MJ=3MJ
- 4. Esta pérdida de energía equivale a 14.6%, la diferencia entre 100% y la eficiencia de conversión del proceso de 85.4%.
Observe el alto rendimiento de bio-carbón sólido a esta temperatura de pirólisis, con un rendimiento mínimo de gas de síntesis líquido y gaseoso, los cuales se consideran pérdidas en este punto. Sin embargo, a temperaturas de pirólisis mucho más altas, se producen más gases de síntesis líquidos y gaseosos. El Ejemplo 1.1.6 muestra la singularidad del proceso de pirólisis en la generación de una gama más amplia de coproductos. También se pueden estimar los balances completos de energía y masa del proceso para evaluar las eficiencias de conversión generales.
Ejemplo1.1.6
Ejemplo 6: Balances básicos de energía y masa de pirólisis de biomasa
Problema:
Un ingeniero realizó un experimento para pirolizar 1.23 kg de biomasa de sorgo (valor calorífico = 18.1 MJ/kg) a una temperatura de 600°C en un pirolizador de barrena. El propósito principal del experimento fue determinar la energía contenida en diversos coproductos del proceso. La energía de entrada incluye la del motor de la barrena (5 amperios, 220 V) y el horno tubular (2,400 Watts). El tiempo de prueba fue de 12 minutos. Los datos recopilados durante los experimentos y otros parámetros asociados necesarios para realizar balances completos de energía y masa son los siguientes:
- Cantidad de biocarbón producido = 0.468 kg
- Volumen de bioaceite producido = 225 mL
- Densidad de = 1.3 g/mL
- Volumen de gas de síntesis producido = 120 L
- Valor calorífico del biocarbón = 23.99 MJ/kg
- Valor calorífico de = 26.23 MJ/kg
Los valores de calentamiento del gas de síntesis producido así como su composición se encuentran en la siguiente tabla.
Gases Primarios | |||
---|---|---|---|
H 2 | CH 4 | CO | |
% Rendimiento |
20% |
10% |
15% |
Densidad (kg/m 3) |
0.0899 |
0.656 |
1.146 |
HV (MJ/kg) |
142 |
55.5 |
10.112 |
Determinar un balance de energía y masa para este proceso e informar cuánta energía estaba contenida en cada uno de los coproductos, así como la eficiencia general de conversión.
Solución
- 1. Dibuje un esquema del proceso completo de balance de masa y energía como en la Figura1.1.11.
- 2. Calcular la energía contenida en la biomasa original como:
- Biomass Energy (MJ)=1.23 kg×18.1MJkg=22.26MJ
- 3. Calcule la energía de entrada del horno como:
- Thermal Energy (MJ)=2.4 kW×12hr60×3.6MJ1kWh=1.728MJ
- 4. Calcule la energía de entrada de la barrena como:
- Auger Energy (MJ)=220 V×5 A×kW1,000VA×12hr60×3.6MJ1kWh=0.792MJ
- 5. Calcular la energía contenida en el bio-carbón como:
- Bio-char Energy (MJ)=0.468 kg×23.99MJkg=11.23MJ
- 6. Calcular la energía contenida en el bio-aceite como:
- Energy (MJ)=225 mL×26.23MJkg×1.3 g mL×kg1000 g=7.67MJ
- 7. El contenido energético total del gas de síntesis es la suma de energía en los gases componentes. Según lo indicado, se produjeron alrededor de 120 L de gas de síntesis, con 20% H 2 (24 L), 10% CH 4 (12 L) y 15% CO (18 L). El contenido energético resultante del bioaceite se calcula como:
- H2(MJ)=24 L×0.0899 kg m3×1 m31,000 L×142MJkg=0.306MJ
- CH4(MJ)=12 L×0.0656 kg m3×1 m31,000 L×55.5MJkg=0.437MJ
- CO(MJ)=18 L×1.145 kg m3×1 m31,000 L×10.112MJkg=0.208MJ
- El contenido energético total del gas de síntesis es:
- Syngas (MJ)=0.306MJ+0.437MJ+0.208MJ=0.951MJ
- La mayor parte de la energía aún se retiene en el bio-carbón (11.23 MJ), seguido del biopetróleo (7.67 MJ) y el gas de síntesis (0.951 MJ).
- 8. El balance energético es:
- Input Energy (MJ)=22.2MJ+1.73MJ+0.792MJ=24.722MJ
- Output Energy (MJ)=11.23MJ+7.67MJ+0.951MJ=19.851MJ
- 9. Calcular la eficiencia de conversión como:
- Conversion Efficiency (%)= Output Input ×100%=19.85124.722×100%=80.3%
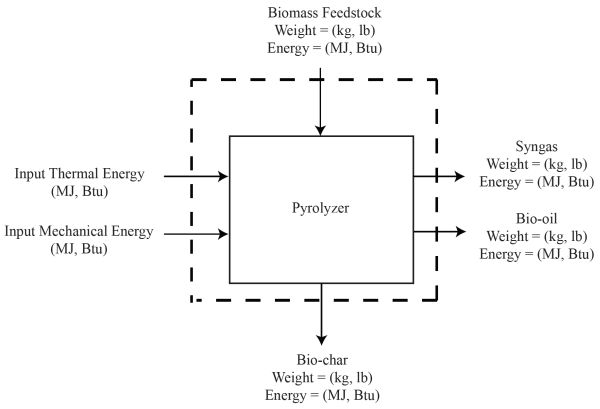
Ejemplo1.1.7
Ejemplo 7: Valor presente y futuro de la inversión en una instalación de sistemas de bioenergía
Problema:
Un inversionista depositó $1,100,000 en un banco en 2007 en lugar de invertirlo en una instalación comercial de biodiesel. Determinar su valor futuro estimado en 2018 utilizando la ecuación del valor presente, asumiendo una tasa de retorno bancaria de 2.36%. Compare esto con invertir el dinero en operar una instalación de biodiesel con un retorno del año 11 de $2M.
Solución
- 1. Este es un cálculo simple del valor futuro usando la Ecuación 1.1.3:
- FV=PV×(1+r)n(Ecuación1.1.3)
donde FV = valor futuro del flujo de caja ($)
PV = valor actual del flujo de caja ($)
r = tasa de retorno o tasa de descuento (decimal)
n = número de periodos (sin unidades)
Future Value =$1,100,000×(1+0.0236)11=$1,421,758
- 2. Si se invierte en un banco, el valor futuro después de 11 años sería de aproximadamente $1.4M en comparación con un retorno de $2M de invertir en la instalación de biodiesel. En este ejemplo, invertir $1.1M en una instalación de biodiesel generó más valor que poner el dinero en un banco.
Ejemplo1.1.8
Ejemplo 8: Depreciación de una planta de biodiesel
Problema:
Se pidió a un ingeniero que reportara la depreciación anual de una instalación de biodiesel cuyo valor inicial de activos es de $1,100,000. La vida útil de la instalación es de 20 años y el valor de salvamento de todos los equipos y activos al final de esta vida es del 10% del valor de capital inicial de la instalación. Utilice el método de línea recta y el método de suma de dígitos para los cálculos de depreciación. Describir las variaciones anuales en la depreciación para cada método.
Solución
El método de línea recta utiliza la Ecuación 1.1.7:
Straight Line Depreciation ($)= Principal-Salvage Value Life of Unit (Ecuación1.1.7)
=$1,100,000−$110,00020=$50,000/ year
La depreciación anual después del año 1 es de $50,000 anuales.
El método de suma de dígitos primero calcula la suma de dígitos de la siguiente manera:
(1 + 2 + 3 + 4 + 5 + 6 + 7 + 8 + 9 + 10 + 11 + 12 + 13 + 14 + 15 + 16 + 17 + 18 + 19 + 20) = 210
El factor para estimar la depreciación para el año 1 utiliza el orden inverso: la vida de la facilidad en el numerador y la suma de dígitos en el denominador con el año 1 teniendo un factor de 20/210 y así sucesivamente.
Year 1 Depreciation ($)=20210×($1,100,000−$110,000)=$94,285
Year 2 Depreciation ($)=19210×($990,000)=$89,571
Year 3 Depreciation ($)=18210×($990,000)=$84,857
Continuar los cálculos para los años 4 al 19 utilizando los años 17 al 2 en el numerador.
Year 20 Depreciation ($)=1210×($990,000)=$4,714
Tenga en cuenta que en ambos métodos, el costo de fin del activo del proyecto es aproximadamente igual al valor de salvamento dado. Si se trazaron los datos, una rápida disminución del valor durante los primeros años utilizando el método de la suma de dígitos generalmente refleja la depreciación real de muchas instalaciones.
Ejemplo1.1.9
Ejemplo 9: Cálculo del valor presente neto, relación costo beneficio, período de amortización y tasa interna de rendimiento para una instalación de biodiesel
Problema:
Se le puede pedir a un ingeniero que evalúe una serie de proyectos para estimar los requisitos de financiamiento. Se pueden utilizar indicadores económicos comparativos para comparar una propuesta de proyecto con otra. Los indicadores comunes son el valor presente neto (VPN), la relación beneficio-costo (BCR), el período de amortización (PBP) y la tasa interna de rendimiento (TIR). Una instalación de biodiésel de 1,892,500 L/año (medio millón de galones por año) con un costo de capital inicial de $1,100,000 y un valor de rescate del 10% tiene los siguientes datos de referencia:
Costo de capital (CC) | 1,100,000 | Costo de Reparación y Mantenimiento | 3% del Costo de Capital | Costo de Planta de Biodiesel por millón de L | $581,241 /ML ($2,200,000/MG) |
---|---|---|---|---|---|
Interés |
7.5% |
Impuestos & Ins. |
2% de CC |
Conv. Eff. |
99% |
Vida |
20 años |
Laboral |
8 hrs/día |
Costo de mano de obra |
$15/hr |
Precio del Aceite Vegetal |
$0.13/L ($0.50/gal) |
Operación |
365 días/año |
Un Gerente |
$60,000/año |
Costo de Procesamiento |
$0.13/L ($0.50/gal) |
Personal |
6 tiempo completo |
Venta |
$0.53/L ($2.00/gal) |
La glicerina |
10% Rendimiento |
La glicerina |
0.18/L ($0.7/gal) |
Biodiesel |
1,873,575 L (495,000 gales) |
Crédito Fiscal |
28% |
Tasa de Descuento |
2.36% |
Depreciación |
Línea Recta |
Valor de Salvamento |
10% del costo inicial de capital |
Los datos pueden ser utilizados para calcular algunos datos de desempeño económico:
- Ingresos brutos anuales promedio para el proyecto con crédito fiscal = $1,314,506
- Ingreso neto promedio anual para el proyecto con crédito fiscal = $279,305
- Promedio de beneficios netos descontados por año = $220,614
- Costos promedio con descuento por año = $817,670
- Promedio de beneficios brutos descontados = $1,038,284
Utilice estos datos para calcular NPV, BCR, PBP e IRR.
Solución
- 1. Calcular el VAN a partir de la Ecuación 1.1.4,
- NPV=∑Nn=1 cash inflow (1+i)n− cash outflow (Ecuación1.1.4)
- o simplemente obtener la diferencia entre los beneficios promedio anuales con descuento y los costos promedio anuales con descuento:
- NPV=$1,038,284−$817,670=$220,614
- El valor de VPN es positivo. De ahí que el proyecto sea económicamente factible.
- 2. El BCR es la relación entre los beneficios descontados y los costos descontados como se muestra:
- BCR= project benefits project costs (Ecuación1.1.5)
- =$1,0.38,284$817,670=1.27
- El BCR es mayor a 1, mostrando también que el proyecto es factible.
- 3. El PBP es la relación entre los costos de capital iniciales y los ingresos netos descontados promedio anual:
- PBP ( years )= project costs annual cash inflows (Ecuación1.1.6)
- =$1,100,000$220,614=5 year
- 4. Para calcular la tasa interna de rendimiento, compare los beneficios netos descontados a lo largo de la vida del proyecto con un factor de descuento supuesto (tasa de descuento). Manualmente, se trata de un método de prueba y error mediante el cual la tasa de descuento asumida da como resultado beneficios netos mayores a cero (positivos) e inferiores a cero (negativos). La tasa de descuento donde el beneficio neto es exactamente igual a cero es la tasa interna de rendimiento para el proyecto.
Por ejemplo, cuando los datos anteriores se codifican en una hoja de cálculo y la tasa de descuento supuesta es del 30%, el beneficio neto descontado se estima en −$173,882, un valor negativo. No obstante, cuando se utiliza la tasa de descuento del 20%, el beneficio neto descontado se calcula como $260,098, un valor positivo. De ahí que la tasa interna de retorno debe estar entre estos valores asumidos (es decir, entre 20% y 30%). Por razón y proporción (trazando estos valores en coordenadas cartesianas X-Y, como flujo de caja, y comparando el triángulo más pequeño con el triángulo más grande, siendo la X el factor descontado por encima del 20% e Y los beneficios netos en $), la tasa interna de retorno se calcula de la siguiente manera:
-
X$260,098=(30%−20%)($260,097+$173,882)
-
X=6%
-
IRR=20%+6%=26%
- Por lo tanto, la TIR debe estar alrededor del 26%, un valor positivo y superior a la tasa de interés bancaria de 7.5%. El proyecto se declara entonces económicamente viable utilizando este parámetro. (Nota: Cuando se calcula mediante hoja de cálculo, los valores de IRR serán ligeramente diferentes de este método manual).
Ejemplo1.1.10
Ejemplo 10: Determinación de la relación energética neta y el balance energético neto para el etanol de maíz con y sin reciclaje de coproductos
Problema:
Para evaluar el mérito de convertir la biomasa en combustible según lo recomendado por el USDA es posible utilizar la relación energética neta (NER) y el balance energético neto (NEB) para una instalación. Numerosos estudios realizados por el USDA para la producción de etanol de maíz a partir de molienda húmeda y molienda en seco han establecido datos basales.
La energía total utilizada para cada proceso, sin considerar el uso de coproductos como fuentes de energía adicional:
- Energía total utilizada para el proceso de molienda en seco = 19.404 MJ/L
- Energía total utilizada para el proceso de molienda en húmedo = 20.726 MJ/L
- Valor calorífico del etanol producido = 21.28 MJ/L
La energía total utilizada para cada proceso cuando todos los productos del sistema se utilizan para abastecer los requerimientos energéticos de la instalación:
- Energía total utilizada para el proceso de molienda en seco = 15.572 MJ/L
- Energía total utilizada para el proceso de molienda en húmedo = 16.482 MJ/L
- Valor calorífico del etanol producido = 21.28 MJ/L
Determinar si es mejor usar molienda húmeda o seca, y si es mejor usar coproductos como fuente de energía dentro de la instalación.
Solución
- 1. La NER se calcula usando la Ecuación 1.1.11:
- NER= Energy Content of Fuel (MJ) Energy Required to Produce the Biofuel (MJ)(Ecuación1.1.11)
Para el proceso de molino seco,NER=21.28MJ/L19.404M/L=1.10
Para el proceso de molino húmedo,NER=21.28MJ/L20.726M/L=1.03
- El proceso de molino seco tiene una NER mayor que el proceso de molino húmedo.
- 2. El NEB se calcula usando la Ecuación 1.1.12:
- NEB = Biofuel Heating Value(MJ) - Energy Required to Produce the Biofuel(MJ) (Ecuación1.1.12)
- Para el proceso de molino seco,NEB=21.28MJL−19.404JL=1.876
- Para el proceso de molino húmedo,NEB=21.28MJL−20.726JL=0.554
- El proceso de molienda en seco es mejor que el proceso de molienda húmeda de acuerdo tanto con la NER como con la NEB cuando no se utilizan coproductos para suministrar energía.
- 3. La NER para el proceso de molino seco con asignación de coproductos es:
- NER=21.28MJ/L15.572M/L=1.37
- La NER para el proceso de molino húmedo cuando se reutilizan los coproductos es:
- NER=21.28MJ/L16.482M/L=1.29
- 4. El NEB para el proceso de molino seco cuando se reutilizan los coproductos para el proceso es:
- NEB=21.28MJL−15.572JL=5.708
- El NEB para el proceso de molino húmedo cuando el coproducto se reutiliza para el proceso es:
- NEB=21.28MJL−16.482JL=4.798
- El proceso de molienda en seco sigue siendo la mejor opción y tanto NER como NEB indican que los coproductos deben ser utilizados como parte del diseño del sistema.
Créditos de imagen
Figura 1. Capareda, S. (CC Por 4.0). (2020). Vías para la conversión de recursos de biomasa en energía.
Figura 2. Capareda, S. (CC Por 4.0). (2020). Esquema del proceso comercial de fabricación de combustible biodiesel.
Figura 3. Capareda, S. (CC Por 4.0). (2020). Esquema del proceso comercial para la elaboración de bioetanol mediante molienda en seco.
Figura 4. Capareda, S. (CC Por 4.0). (2020). Representación esquemática de diversos diseños de digestores de biogás de alta velocidad.
Figura 5. Capareda, S. (CC Por 4.0). (2020). Las salidas y aplicaciones de la pirólisis de biomasa.
Figura 6. Capareda, S. (CC Por 4.0). (2020). Diagrama esquemático de un gasificador de lecho fluidizado.
Figura 7. Capareda, S. (CC Por 4.0). (2020). Las relaciones entre el gasto de capital (CAPEX) y el gasto operativo (OPEX) para un proyecto de bioenergía.
Figura 8. Capareda, S. (CC Por 4.0). (2020). Esquema de las categorías de combustibles renovables anidados en Estados Unidos bajo los estándares de combustibles renovables.
Figura 9. Capareda, S. (CC Por 4.0). (2020). El papel de los recursos de biomasa para un futuro sustentable bajo en carbono.
Figura 10. Capareda, S. (CC Por 4.0). (2020). Jerarquía de utilización de biomasa desde aplicaciones de alto valor y bajo volumen (arriba) hasta aplicaciones de bajo valor y alto volumen (abajo).
Figura 11. Capareda, S. (CC Por 4.0). (2020). Distribución de masa y energía de todos los productos del proceso de pirólisis.
Referencias
Capareda, S. (2014). Introducción a las conversiones de energía de biomasa. Boca Raton, FL: Prensa CRC. https://doi.org/10.1201/b15089.
Hamilton, D. W. (2012). Contenido de materia orgánica de aguas residuales y estiércol, BAE 1760. Stillwater: Servicio de Extensión Cooperativa de Oklahoma.
Lettinga, G., van Velsen, A. F., Hobma, S. W., de Zeeuw, W., & Klapwijk, A. (1980). Uso del concepto de reactor de manto de lodo ascendente (USB) para el tratamiento biológico de aguas residuales, especialmente para el tratamiento anaeróbico. Biotecnología. Bioeng. , 22 (4), 699-734. doi.org/10.1002/bit.260220402.
Lilienthal, P., & Lambert, T. W. (2011). HOMERO. El modelo de optimización de micropotencia. Guía de inicio para el legado de HOMER. Ver. 2.68. Boulder, CO y Golden, CO: Homer Energy y NREL USDOE.
Maglinao, R. L., Resurreccion, E. P., Kumar, S., Maglinao, A. L., Capareda, S., & Moser, B. R. (2019). Vía de hidrodesoxigenación-alquilación para la síntesis de un mejorador sustentable de lubricantes a partir de aceites vegetales y fenoles derivados de lignina. Ind. Ing. Chem. Res., 1-50. https://doi.org/10.1021/acs.iecr.8b05188.
Pimentel, D. (2003). Combustibles de etanol: El balance energético, la economía y los impactos ambientales son negativos. Resour Natural. Res., 12 (2), 127-134. https://doi.org/10.1023/A:1024214812527.
Stout, B. A. 1984. Uso y gestión de la energía en la agricultura. Belmont, CA: Breton Publ.
Watts, S., & Hertvik, J. (2018). CapEx vs OpEx para TI y Cloud: ¿cuál es la diferencia? Blog The Business of IT, número 2 de enero. Recuperado de https://www.bmc.com/blogs/capex-vs-opex/.