7.1: Capítulo 7: Lean Manufacturing
- Page ID
- 153507
\( \newcommand{\vecs}[1]{\overset { \scriptstyle \rightharpoonup} {\mathbf{#1}} } \)
\( \newcommand{\vecd}[1]{\overset{-\!-\!\rightharpoonup}{\vphantom{a}\smash {#1}}} \)
\( \newcommand{\id}{\mathrm{id}}\) \( \newcommand{\Span}{\mathrm{span}}\)
( \newcommand{\kernel}{\mathrm{null}\,}\) \( \newcommand{\range}{\mathrm{range}\,}\)
\( \newcommand{\RealPart}{\mathrm{Re}}\) \( \newcommand{\ImaginaryPart}{\mathrm{Im}}\)
\( \newcommand{\Argument}{\mathrm{Arg}}\) \( \newcommand{\norm}[1]{\| #1 \|}\)
\( \newcommand{\inner}[2]{\langle #1, #2 \rangle}\)
\( \newcommand{\Span}{\mathrm{span}}\)
\( \newcommand{\id}{\mathrm{id}}\)
\( \newcommand{\Span}{\mathrm{span}}\)
\( \newcommand{\kernel}{\mathrm{null}\,}\)
\( \newcommand{\range}{\mathrm{range}\,}\)
\( \newcommand{\RealPart}{\mathrm{Re}}\)
\( \newcommand{\ImaginaryPart}{\mathrm{Im}}\)
\( \newcommand{\Argument}{\mathrm{Arg}}\)
\( \newcommand{\norm}[1]{\| #1 \|}\)
\( \newcommand{\inner}[2]{\langle #1, #2 \rangle}\)
\( \newcommand{\Span}{\mathrm{span}}\) \( \newcommand{\AA}{\unicode[.8,0]{x212B}}\)
\( \newcommand{\vectorA}[1]{\vec{#1}} % arrow\)
\( \newcommand{\vectorAt}[1]{\vec{\text{#1}}} % arrow\)
\( \newcommand{\vectorB}[1]{\overset { \scriptstyle \rightharpoonup} {\mathbf{#1}} } \)
\( \newcommand{\vectorC}[1]{\textbf{#1}} \)
\( \newcommand{\vectorD}[1]{\overrightarrow{#1}} \)
\( \newcommand{\vectorDt}[1]{\overrightarrow{\text{#1}}} \)
\( \newcommand{\vectE}[1]{\overset{-\!-\!\rightharpoonup}{\vphantom{a}\smash{\mathbf {#1}}}} \)
\( \newcommand{\vecs}[1]{\overset { \scriptstyle \rightharpoonup} {\mathbf{#1}} } \)
\( \newcommand{\vecd}[1]{\overset{-\!-\!\rightharpoonup}{\vphantom{a}\smash {#1}}} \)
\(\newcommand{\avec}{\mathbf a}\) \(\newcommand{\bvec}{\mathbf b}\) \(\newcommand{\cvec}{\mathbf c}\) \(\newcommand{\dvec}{\mathbf d}\) \(\newcommand{\dtil}{\widetilde{\mathbf d}}\) \(\newcommand{\evec}{\mathbf e}\) \(\newcommand{\fvec}{\mathbf f}\) \(\newcommand{\nvec}{\mathbf n}\) \(\newcommand{\pvec}{\mathbf p}\) \(\newcommand{\qvec}{\mathbf q}\) \(\newcommand{\svec}{\mathbf s}\) \(\newcommand{\tvec}{\mathbf t}\) \(\newcommand{\uvec}{\mathbf u}\) \(\newcommand{\vvec}{\mathbf v}\) \(\newcommand{\wvec}{\mathbf w}\) \(\newcommand{\xvec}{\mathbf x}\) \(\newcommand{\yvec}{\mathbf y}\) \(\newcommand{\zvec}{\mathbf z}\) \(\newcommand{\rvec}{\mathbf r}\) \(\newcommand{\mvec}{\mathbf m}\) \(\newcommand{\zerovec}{\mathbf 0}\) \(\newcommand{\onevec}{\mathbf 1}\) \(\newcommand{\real}{\mathbb R}\) \(\newcommand{\twovec}[2]{\left[\begin{array}{r}#1 \\ #2 \end{array}\right]}\) \(\newcommand{\ctwovec}[2]{\left[\begin{array}{c}#1 \\ #2 \end{array}\right]}\) \(\newcommand{\threevec}[3]{\left[\begin{array}{r}#1 \\ #2 \\ #3 \end{array}\right]}\) \(\newcommand{\cthreevec}[3]{\left[\begin{array}{c}#1 \\ #2 \\ #3 \end{array}\right]}\) \(\newcommand{\fourvec}[4]{\left[\begin{array}{r}#1 \\ #2 \\ #3 \\ #4 \end{array}\right]}\) \(\newcommand{\cfourvec}[4]{\left[\begin{array}{c}#1 \\ #2 \\ #3 \\ #4 \end{array}\right]}\) \(\newcommand{\fivevec}[5]{\left[\begin{array}{r}#1 \\ #2 \\ #3 \\ #4 \\ #5 \\ \end{array}\right]}\) \(\newcommand{\cfivevec}[5]{\left[\begin{array}{c}#1 \\ #2 \\ #3 \\ #4 \\ #5 \\ \end{array}\right]}\) \(\newcommand{\mattwo}[4]{\left[\begin{array}{rr}#1 \amp #2 \\ #3 \amp #4 \\ \end{array}\right]}\) \(\newcommand{\laspan}[1]{\text{Span}\{#1\}}\) \(\newcommand{\bcal}{\cal B}\) \(\newcommand{\ccal}{\cal C}\) \(\newcommand{\scal}{\cal S}\) \(\newcommand{\wcal}{\cal W}\) \(\newcommand{\ecal}{\cal E}\) \(\newcommand{\coords}[2]{\left\{#1\right\}_{#2}}\) \(\newcommand{\gray}[1]{\color{gray}{#1}}\) \(\newcommand{\lgray}[1]{\color{lightgray}{#1}}\) \(\newcommand{\rank}{\operatorname{rank}}\) \(\newcommand{\row}{\text{Row}}\) \(\newcommand{\col}{\text{Col}}\) \(\renewcommand{\row}{\text{Row}}\) \(\newcommand{\nul}{\text{Nul}}\) \(\newcommand{\var}{\text{Var}}\) \(\newcommand{\corr}{\text{corr}}\) \(\newcommand{\len}[1]{\left|#1\right|}\) \(\newcommand{\bbar}{\overline{\bvec}}\) \(\newcommand{\bhat}{\widehat{\bvec}}\) \(\newcommand{\bperp}{\bvec^\perp}\) \(\newcommand{\xhat}{\widehat{\xvec}}\) \(\newcommand{\vhat}{\widehat{\vvec}}\) \(\newcommand{\uhat}{\widehat{\uvec}}\) \(\newcommand{\what}{\widehat{\wvec}}\) \(\newcommand{\Sighat}{\widehat{\Sigma}}\) \(\newcommand{\lt}{<}\) \(\newcommand{\gt}{>}\) \(\newcommand{\amp}{&}\) \(\definecolor{fillinmathshade}{gray}{0.9}\)OBJETIVO
Después de completar esta unidad, deberías ser capaz de:
- Aplica 5S en cualquier Taller de Maquinas.
- Describir el concepto Kaizen.
- Describir Implementar Lean Manufacturing.
Lean 5S:
“5S” es un método de organización del lugar de trabajo que consta de cinco palabras: Ordenar, Establecer en orden, Brillo, Estandarizar y Sostener. Todas estas palabras comienzan con la letra S. Estos cinco componentes describen cómo almacenar artículos y mantener el nuevo orden. Al tomar decisiones, los empleados discuten la estandarización, lo que hará que el proceso de trabajo quede claro entre los trabajadores. Al hacer esto, cada empleado sentirá la propiedad del proceso.
Fase 0: Seguridad
A menudo se asume que un programa 5S correctamente ejecutado mejorará la seguridad en el lugar de trabajo, pero esto es falso. La seguridad no es una opción; es una prioridad.
Fase 1: Ordenar
Revisar todos los artículos en el lugar de trabajo, conservando solo lo que se necesita.
Fase 2: Enderezar
Todo debe tener un lugar y estar en su lugar. Los artículos deben dividirse y etiquetarse. Todo debe ser arreglado pensadamente. Los empleados no deberían tener que agacharse repetitivamente. Colocar el equipo cerca de donde se utiliza. Este paso es parte de por qué lean 5s no se considera “limpieza estandarizada”.
Fase 3: Brillo
Asegúrese de que el lugar de trabajo esté limpio y ordenado. Al hacer esto, será más fácil estar al tanto de dónde están las cosas y dónde deben estar. Después de trabajar, limpiar el espacio de trabajo y devolver todo a su posición anterior. Mantener limpio el lugar de trabajo debe integrarse en la rutina diaria.
Fase 4: Estandarizar
Estandarizar los procedimientos de trabajo y hacerlos consistentes. Todo trabajador debe ser consciente de cuáles son sus responsabilidades al seguir los tres primeros pasos.
Fase 5: Sostenga
Evaluar y mantener los estándares. Los pasos antes mencionados deberían convertirse en la nueva norma en funcionamiento. No vuelvas poco a poco a las viejas formas. Al tomar parte del nuevo procedimiento, piense en formas de mejorar. Revise los primeros cuatro pasos cuando se presenten nuevas herramientas o requisitos de salida.
Kaizen
Mientras que el proceso lean 5S se enfoca en la eliminación de desechos, Kaizen se enfoca en la práctica de la mejora continua. Al igual que lean 5S, Kaizen identifica tres aspectos principales del lugar de trabajo: M uda (desechos), M ura (inconsistencias) y M uri (tensión en personas y máquinas). Sin embargo, el proceso paso a paso de Kaizen es más extenso que el proceso lean 5S.
Descripción general del proceso Kaizen:
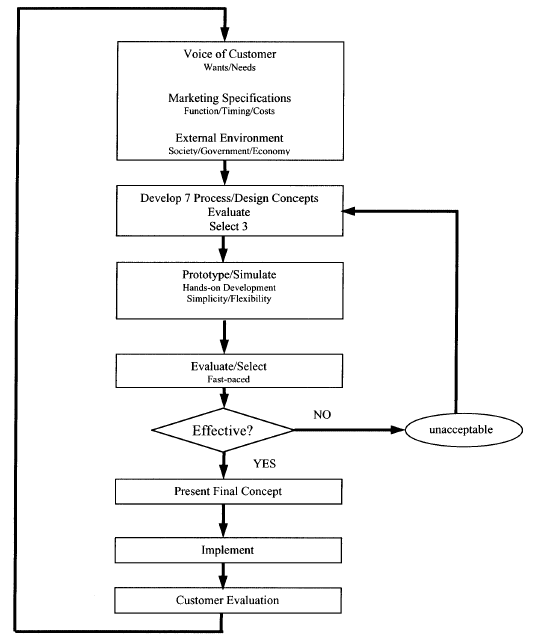
1. Identificar un problema.
2. Formar un equipo.
3. Recopile información de clientes internos y externos, y determine metas para el proyecto.
4. Revisar la situación o proceso actual.
5. Haga una lluvia de ideas y considere siete alternativas posibles.
6. Decidir las tres mejores alternativas de las siete.
7. Simular y evaluar estas alternativas antes de la implementación.
8. Presentar la idea y sugerencias a los directivos.
9. Implementar físicamente los resultados Kaizen y tomar en cuenta los efectos.
Lean manufacturing mejora a medida que pasa el tiempo uno, por lo que es importante continuar la educación sobre el mantenimiento de estándares. Es crucial cambiar los estándares y capacitar a los trabajadores cuando se les presentan nuevos equipos o reglas.
Lean
Piense en un departamento de mantenimiento como al servicio de clientes internos: los diversos departamentos y trabajadores de la empresa.
Lean es diferente del modelo occidental tradicional de producción en masa que se basa en economías de escala para generar ganancias. Cuanto más se haga más barato se volverá el producto, mayor será el margen de beneficio potencial. Se basa en predicciones de las necesidades del cliente, o en la creación de necesidades del cliente. Tiene dificultades para lidiar con cambios inusuales en la demanda.
La producción ajustada responde a la demanda comprobada de los clientes. Procesamiento de extracción: el cliente tira de la producción. En un sistema masivo el productor empuja el producto al mercado, empuja el procesamiento.
Construyendo una cultura a largo plazo que se centre en la mejora.
Respeto a los trabajadores mejor capacitados y educados, más flexibles
Lean es una filosofía que se centra en lo siguiente:
- Satisfacer las necesidades de
- Mejora continua y gradual
- Haciendo continuamente mejores productos
- Valorar el insumo de los trabajadores
- Tomando la visión a largo plazo
- Eliminando errores
- Eliminación de residuos
Desechos: usar demasiados recursos (materiales, tiempo, energía, espacio, dinero, recursos humanos, malas instrucciones)
Desechos:
- Sobreproducción
- Defectos
- Procesamiento innecesario
- Esperando (perdiendo el tiempo)
- Perder el tiempo y el talento humanos
- Demasiados escalones o mudanzas. Transporte excesivo
- Inventario excesivo
La producción ajustada incluye trabajar con proveedores, subcontratistas y vendedores para transmitir la línea de todo el proceso.
El objetivo es que la producción fluya sin problemas evitando costosos arranques y paradas.
A la idea se le llama justo a tiempo “producir sólo lo que se necesita, cuando se necesita, y sólo en la cantidad necesaria”. El proceso de producción debe ser flexible y rápido.
Inventario = justo lo que necesitas
En producción en masa = por si acaso. Los suministros y productos adicionales se almacenan por si acaso son necesarios.
Terminología:
Simplificación de procesos: un proceso fuera del flujo de producción
Defectos: el sistema de producción en masa realiza una inspección al final de la producción para detectar defectos antes de que se envíen. El problema es que los recursos ya se han “gastado” para hacer el producto de desecho” Trate de prevenir problemas de inmediato, como suceden, luego prevenirlos. Inspección durante la producción, en cada etapa de producción.
Seguridad: el tiempo herido es una pérdida de tiempo
Información: necesita la información correcta en el momento adecuado (demasiado, muy poco, demasiado tarde)
Principios:
Poka-yoke: prueba de errores que determina la causa de los problemas y luego elimina la causa para evitar más errores
Errores de juicio: encontrar problemas después del proceso
Inspecciones informativas: análisis de datos de inspecciones durante el proceso
Inspecciones de origen: inspección antes de que comience el proceso para evitar errores.
MEDIA MAGRA
Uno de los términos aplicados a una interpretación simple de corte de costos, corte de trabajo de Lean es Mean Lean. A menudo, los gerentes modernos piensan que están haciendo lean sin comprender la importancia de los trabajadores y las relaciones a largo plazo.
Mantenimiento Centrado en Confiabilidad
El mantenimiento centrado en la confiabilidad es un sistema para diseñar un programa de mantenimiento rentable. Puede ser un complejo detallado, informático, impulsado estadísticamente, pero en sus fundamentos es bastante simple. Sus ideas se pueden aplicar al diseño y funcionamiento de un sistema de PM, y también pueden guiar su aprendizaje mientras realiza tareas de mantenimiento, solución de problemas, reparación y energía.
Estos son principios básicos de RCM. Estos nueve conceptos fundamentales son:
- Las fallas ocurren.
- No todas las fallas tienen la misma probabilidad
- No todas las fallas tienen las mismas consecuencias
- Los componentes simples se desgastan, los sistemas complejos se descomponen
- Un buen mantenimiento proporciona la funcionalidad requerida para el menor costo posible
- El mantenimiento solo puede lograr la confiabilidad inherente del diseño del equipo
- El mantenimiento innecesario quita los recursos del mantenimiento necesario
- Los buenos programas de mantenimiento experimentan una mejora continua.
El mantenimiento consiste en todas las acciones tomadas para garantizar que los componentes, equipos y sistemas proporcionen las funciones previstas cuando sea necesario.
Un sistema RCM se basa en responder a las siguientes preguntas:
1. ¿Cuáles son las funciones y estándares de desempeño deseados de los equipos?
2. ¿De qué manera puede dejar de cumplir con sus funciones? (¿Cuáles son las fallas más probables? ¿Qué tan probable es cada tipo de falla? ¿Serán obvias las fallas? ¿Puede ser una falla parcial?)
3. ¿Qué causa cada falla?
4. ¿Qué sucede cuando ocurre cada falla? (¿Cuál es el riesgo, peligro etc.?)
5. ¿De qué manera importa cada falla? ¿Cuáles son las consecuencias de una falla total o parcial?
6. ¿Qué se puede hacer para predecir o prevenir cada falla? ¿Cuánto costará predecir o prevenir cada falla?
7. ¿Qué se debe hacer si no se puede encontrar una tarea proactiva adecuada (acciones predeterminadas) (ninguna tarea podría estar disponible o podría ser demasiado costosa para el riesgo)?
El equipo se estudia en el contexto de dónde cuándo y cómo se está utilizando
Todas las acciones de mantenimiento se pueden clasificar en una de las siguientes categorías:
- Mantenimiento Correctivo — Restaurar la función perdida o degradada
- Mantenimiento Preventivo — Minimiza la oportunidad de fallar la función
- Mantenimiento alterativo: elimine la condición insatisfactoria cambiando el diseño o el uso del sistema
Dentro de la categoría de mantenimiento preventivo, todas las tareas realizadas pueden describirse como pertenecientes a uno de los cinco (5) tipos principales de tareas:
- Condición dirigida: renueva la vida en función de la condición medida en comparación con un estándar
- Tiempo Dirigido — Renueve la vida independientemente de su condición
- Hallazgo de fallas: determinar si se ha producido una falla
- Servicio — Agregar/reponer consumibles
- Lubricación: aceite, grasa o lubricar de otro modo
Hacemos mantenimiento porque creemos que la confiabilidad del hardware se degrada con la edad, pero que podemos hacer algo para restaurar o mantener la confiabilidad original que se paga por sí misma.
El RCM está centrado en la confiabilidad. Su objetivo es mantener la confiabilidad inherente del diseño del sistema o equipo, reconociendo que los cambios en la confiabilidad inherente solo pueden lograrse a través de cambios de diseño. Debemos entender que el equipo o sistema debe ser estudiado en la situación en la que está funcionando.
Implementando Lean Manufacturing
Analizar cada paso en el proceso original antes de realizar el cambio
Lean Manufacturing se centra principalmente en la reducción de costos y el aumento de la rotación y la eliminación de actividades que no agreguen valor al proceso de fabricación. Básicamente lo que hace el lean manufacturing es ayudar a las empresas a lograr una producción dirigida, así como otras cosas, mediante la introducción de herramientas y técnicas fáciles de aplicar y mantener. Lo que estas herramientas y técnicas están haciendo es reducir y eliminar los desechos, cosas que no son necesarias en el proceso de fabricación.
Los ingenieros de fabricación se propusieron utilizar la metodología DMAIC (Design, Measure, Analyze, Improve, Controle) de seis sigma, junto con la fabricación ajustada, para cumplir con los requisitos del cliente relacionados con la producción de tubos.
Los ingenieros de fabricación se encargaron de diseñar un nuevo diseño de proceso de la línea de producción de tubos. Los objetivos del proyecto fueron:
- Mejora de la calidad
- Disminución de chatarra
- Entrega al punto de uso
- Tamaños de lote más pequeños
- Implementación de un sistema pull
- Mejor retroalimentación
- Aumento de la producción
- Responsabilidad Individual
- Disminución de WIP
- Flexibilidad para cenar
Antes de realizar cambios, el equipo analiza cada paso en el diseño original del proceso de la línea de producción de tubos.
1. Allí se intenta entender el proceso del estado original, identificar el área problemática, paso innecesario y no valor agregado.
2. Después de mapear el proceso, el equipo lean recopiló datos del banco de la Junta de Revisión de Materiales (MRB) para medir y analizar los principales tipos de defectos. Para comprender mejor el proceso, el equipo también realizó un estudio de tiempo para una ejecución de producción de 20 días.
En el estado original, la línea de tubos constaba de un operador y cuatro operaciones, separadas en dos estaciones por una mesa grande mediante un sistema de empuje. La mesa actuó como separador entre la segunda y tercera operación.
El primer problema descubierto fue el desequilibrio de la línea. La primera estación se utilizó alrededor del 70% del tiempo. Los operadores de la segunda estación pasaban gran parte de su tiempo esperando entre tiempos de ciclo. Al combinar las estaciones uno y dos, el margen de mejora se hizo evidente con respecto a la responsabilidad individual, el control del inventario por parte del operador y la retroalimentación inmediata cuando se produjo un problema. El estudio del tiempo y el diseño del departamento reflejan estos hallazgos.
Se reconoció un segundo problema. Debido al flujo del proceso, la tasa de producción no permitió que el cronograma de producción se cumpliera con dos estaciones. Debido a que los operadores perdieron la pista de los ciclos de las máquinas, las máquinas esperaban la atención del Los operadores también intentaron empujar las piezas a través de la primera estación, la operación de cuello de botella en el proceso, y luego continuaron fabricando las piezas en las dos últimas operaciones. Por lo general, se acumularon largas series de WIP y los problemas de calidad no se detectaron hasta que se produjeron muchas piezas defectuosas.
Los datos originales del estado fueron tomados de los últimos 20 días antes del cambio. Los equipos analizan cada paso en el original y realizando cambios. Los hallazgos del estudio de tiempo sobre el proceso original proporcionaron la base para reducir el tiempo del ciclo, equilibrar la línea, diseñar el uso de kanbans y programación Just In Time, mejorar la calidad, disminuir el tamaño del lote y WIP, y mejorar el flujo. Los nuevos datos del proceso se tomaron a partir de un mes después de la implementación. Este retraso dio a los operadores de la máquina la oportunidad de entrenar y llegar al nuevo sistema de diseño de proceso.
Con el diseño de celda en forma de U; Las piezas cumplen con todos los requisitos del cliente. Se eliminó la tabla en el proceso original, casi eliminando WIP. Con la reducción de WIP y el aumento de la producción.
Algunos de los conceptos utilizados para mejorar el proceso incluyeron la participación total de los empleados (TEI), tamaños de lote más pequeños, programación, inventario de punto de uso y diseño mejorado. Todos los empleados y supervisores del departamento estuvieron involucrados en todas las fases del proyecto. Sus ideas y sugerencias fueron incorporadas en el proceso de planeación e implementación para obtener una mayor aceptación de los cambios en el proceso. Se introdujeron tamaños de lote más pequeños para minimizar el número de piezas producidas antes de detectar defectos. Se introdujeron kanbans (en forma de racks de manejo de materiales) para controlar WIP e implementar un sistema de tracción. Y el diseño de las celdas disminuyó el desplazamiento entre operaciones.
Se autorizó a los operadores a detener la línea cuando surgieran problemas. En el estado original, los operadores seguían funcionando partes cuando una operación estaba abajo. Con kanban
control, el diseño eliminó la capacidad de almacenar WIP, requiriendo que el operador cerrara toda la línea. El diseño de celdas brinda excelentes oportunidades para mejorar la comunicación entre operadores sobre problemas y ajustes, para lograr una mejor calidad.
La inspección diaria del proceso de estado original, los operadores pasaron mucho tiempo, ya sea esperando a la persona que manejaba el material, o desempeñándose como un manejo de materiales. Con la celda en forma de U, la entrega al punto de uso es mejor para el operador. El operador coloca cajas de materia prima en seis carros de rodillos móviles, donde es fácil de conseguir. Las seis cajas son suficientes para durar un periodo de 24 horas.
Para reducir los tiempos de configuración, las herramientas necesarias para la reparación y los ajustes de la máquina se encuentran en la celda. Los tornillos no están estandarizados; las herramientas se configuran en orden de aumentar el tamaño para identificar rápidamente la herramienta adecuada.
Durante tres meses se monitoreó el proceso para verificar que estaba en control. La comparación de estudios de tiempo desde el estado original y el diseño implementado demostró un aumento en la producción de 300 a 514 productos terminados por turno. El nuevo diseño eliminó el doble manejo entre la segunda y tercera operación, así como en la etapa de empaque. También se redujo a lo largo del tiempo al facilitar el ciclo de las cuatro operaciones en un orden de sistema de extracción. La demanda de los clientes se cubrió con dos turnos, lo que redujo el costo laboral.
Los resultados del rediseño son los siguientes:
- WIP disminuyó un 97%
- La producción aumentó 72%
- La chatarra se redujo en 43%
- Utilización de la máquina incrementada en un 50%
- Utilización de mano de obra incrementada en 25%
- Los costos laborales se redujeron en 33%
- Se incrementó el nivel de Sigma de 2.6 a 2.8
Este proyecto arrojó menores costos de mano de obra y chatarra, y permitió a la organización hacer un mejor trabajo al hacer entregas a tiempo, al tiempo que permitió un inventario más pequeño de bienes terminados. Los números de producción diaria y el tiempo de ciclo de una sola pieza sirvieron de referencia para monitorear el progreso hacia la meta. Aunque el aumento del nivel sigma, la reducción de 43% en defectos, 97% de reducción en WIP y aumento de producción de 72% contribuyeron al objetivo del proyecto.
Implementar lean es un proceso interminable; esto es lo que es la mejora continua
acerca de. Cuando se implementa un aspecto de lean, siempre se puede mejorar. No te cuelgues, pero no dejes que las cosas vuelvan al punto de partida. Siempre habrá tiempo para volver atrás y refinar algunos de los procesos.
Antes de que se implementara Lean Manufacturing en Nypro Oregon Inc., operaríamos usando la fabricación tradicional. La fabricación tradicional consiste en producir todo un producto determinado para el mercado para nunca dejar que el equipo esté inactivo. Estos bienes deben ser guardados o enviados a un cliente que puede no estar listo para ellos. Si se produce más de lo que se puede vender, los productos se venderán con un descuento profundo (a menudo una pérdida) o simplemente se desecharán. Esto puede sumar una enorme cantidad de desechos. Después de implementar los conceptos de Lean Manufacturing, nuestra empresa utiliza justo a tiempo. Justo a tiempo se refiere a producir y entregar el bien en la cantidad requerida cuando el cliente lo requiere y no antes. En Lean Manufacturing, la manufactura solo produce lo que el cliente quiere, cuando lo quiere. Esta a menudo es una forma mucho más rentable de fabricar en comparación con equipos de alto precio y alto volumen.
Prueba unitaria:
1. ¿Qué es 5S?
2. Por favor explique cada “S” de las 5S.
3. Por favor, explique el concepto Kaizen.
4. ¿Qué es el procesamiento Pull?
5. ¿Qué es el Poka-yoke?
6. ¿Qué es el DMAIC de seis sigma?
7. ¿Cuáles son los objetivos para un nuevo diseño de proceso de la línea de producción de tubos?
8. Antes de realizar cambios, el equipo de ingenieros de Manufactura ¿qué hace primero?
9. Por favor, enumera los resultados del rediseño.
10. La clave para implementar una nueva idea o concepto lean es hacer ¿qué?
INFORMACIÓN DE ATRIBUCIÓN DEL CAPÍTULO
Este capítulo se derivó de las siguientes fuentes.
- Lean 5S derivado de Lean Manufacturing por diversos autores, CC:BY-SA 3.0.
- Kaizen derivado de Un enfoque basado en Kaizen para el diseño de sistemas de fabricación celular: un estudio de caso por VirginiaTech, CC:BY-SA 4.0.
- Kaizen (imagen) derivado de Un enfoque basado en Kaizen para el diseño de sistemas de fabricación celular: un estudio de caso de VirginiaTech, CC:BY-SA 4.0.