4.3: Diagramas de Tubería e Instrumentación - Ubicación de Controles y Estructuras de Control Estándar
- Page ID
- 85506
Introducción
Un diagrama de tuberías e instrumentación (P&ID) es un diseño esquemático de una planta que muestra las unidades que se van a usar, las tuberías que conectan estas unidades y los sensores y válvulas de control. Las estructuras estándar ubicadas en un P&ID incluyen tanques de almacenamiento, tanques de sobretensión, bombas, intercambiadores de calor, reactores y columnas de destilación. Estos tres últimos comprenden la mayoría de los problemas de control de una sola unidad de la industria de procesos químicos.
Los P&ID tienen una serie de usos importantes en el diseño y operación exitosa de plantas de proceso químico. Una vez que se realiza un diagrama de flujo del proceso, los P&ID ayudan a los ingenieros a desarrollar estrategias de control que garantizan que se cumplan los objetivos de producción y cumplan con todos los estándares ambientales Estos diagramas también son muy importantes para localizar válvulas y componentes de proceso durante el mantenimiento y la solución de problemas.
Cada página de un P&ID debe ser fácil de leer y corresponder a una acción específica de la planta. Además, los símbolos utilizados en el P&ID son uniformes en todas partes. Los diagramas para intercambiadores de calor, reactores de tanque agitado continuamente (CSTR) y columnas de destilación que se muestran en secciones posteriores de este wiki representan una pequeña muestra de símbolos estándar para estas estructuras. Para obtener una lista y una explicación de los símbolos relacionados con los controles estándar, consulte la notación estándar PID.
Estrategias generales para la implementación de buenos sistemas de control
Hay varias pautas a seguir al diseñar P&ID para una planta. La primera consideración es la operación estable de la planta para que se cumplan todas las normas de seguridad y ambientales. Mantener la calidad del producto también debe ser un objetivo principal de diseño. Además, los sistemas deben diseñarse para responder rápidamente a cambios rápidos en la tasa y la calidad del producto. Por lo general, los sistemas de control deben ejecutarse en modo automático para que el sistema se corrija por sí mismo, a diferencia de un modo manual, que requiere la supervisión del operador.
Al configurar un sistema de control, es útil enfocarse primero en el control del balance de masa, que puede ser monitoreado por bucles de control de nivel y presión que utilizan caudales de gas o líquido. Adicionalmente, se debe establecer una estructura de control del producto para garantizar una operación eficiente del proceso. Para evitar que los controles entren en conflicto entre sí, se debe realizar un examen final de los arroyos controlados. Luego se puede instalar instrumentación adicional para evitar conflictos entre controladores. Finalmente, se deben establecer tolerancias adecuadas para controladores que afecten directamente la acción de otros controladores. La determinación de la colocación óptima del control es esencial para una operación exitosa de la planta.
Estructuras estándar y ubicación de las características de control
Como se mencionó anteriormente, el control de intercambiadores de calor, reactores y columnas de destilación representa la mayoría de los problemas de control de una sola unidad. En la siguiente tabla se resumen los esquemas de control derivados en los siguientes ejemplos. Los esquemas de control más comunes se enumeran en la siguiente tabla.
Tabla 1: Resumen de estructuras comunes de P&ID
Para la mayoría de los equipos, primero se realiza un análisis de grados de libertad y luego se diseña un esquema de control basado en los grados de libertad.
Intercambiador de calor
Para monitorear el rendimiento de un intercambiador de calor, la corriente de producto es importante. Por lo general, la corriente de producto debe estar dentro de algún rango de temperatura antes de continuar hacia las unidades de proceso aguas abajo. La temperatura de salida de esta corriente se puede utilizar para calcular la transferencia de calor. El vapor se controla con el fin de obtener la temperatura deseada de la corriente del producto. Una forma de influir en la temperatura del producto es controlando el flujo del vapor calentado. Este control basado en el flujo puede tardar algún tiempo en implementarse y, por lo tanto, provocar fluctuaciones en el proceso. Dependiendo del proceso, estas fluctuaciones pueden o no ser aceptables. En lugar de monitorear el caudal, se puede monitorear la presión del vapor, logrando un control más estricto de la temperatura. Un cambio en la presión es mucho más fácil de monitorear y se correlaciona directamente con un cambio en la temperatura del vapor. Esto ofrece una manera efectiva de controlar las temperaturas del proceso. El control de presión también permite monitorear el estado físico de las tuberías, ya que los cambios de presión ocurren a medida que avanza el ensuciamiento. La presión, combinada con el caudal y la temperatura del vapor calentado, se puede utilizar para calcular este ensuciamiento que ocurre dentro de un equipo. Es importante recordar que el vapor siempre debe ser controlado en el lado de entrada del intercambiador de calor por un mejor control de la presión y razones de seguridad, como se muestra en la figura 1 a continuación.
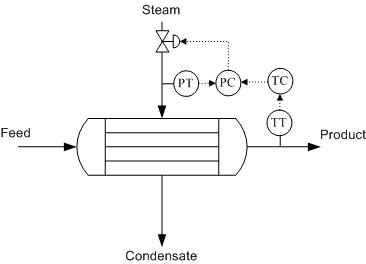
Columna de Destilación
Debido a que la viabilidad económica de un proceso global se basa significativamente en la pureza del producto, es importante que las columnas de destilación mantengan un funcionamiento estable. Los cambios en la composición y el caudal de la corriente de alimentación son perturbaciones comunes en el funcionamiento de la columna de destilación. El mal funcionamiento de los controladores puede socavar la efectividad de la composición del producto. Un análisis de grados de libertad puede ayudar a colocar sensores y actuadores en lugares apropiados, sin incluir demasiados sensores y actuadores, para obtener un sistema de control eficiente.
Análisis Grados de Libertad
Un simple análisis de grados de libertad puede facilitar el diseño de un esquema de control, así como mejorar el esquema de control en general. Un enfoque de control de procesos a grados de libertad, adaptado del Módulo 3.1 ECOSSE, requiere tabulación de flujos y fases adicionales.
DOF = Flujos − ExtraFases + 1
Una columna de destilación típica contiene las siguientes corrientes: alimentación (1), fondos (2), destilado (3), reflujo (4), producto (5), mezcla vapor-líquido (6), agua de enfriamiento (7) y vapor (8). También hay tres localizaciones donde hay dos fases, vapor y líquido, presentes en equilibrio. Estos se denotan como una “fase extra”, ya que la temperatura y la presión no son independientes en un sistema bifásico.
DOF = 8 − 3 + 1 = 6
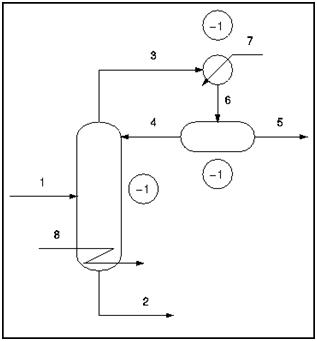
En la práctica típica, la presión del condensador y el calderín se especifican como presión atmosférica. Una vez especificada la presión en el condensador y calderín (ambos sistemas bifásicos), se especifica la temperatura y por lo tanto los grados de libertad se reducen en dos. El total de grados de libertad, en la práctica, es de seis.
DOF = 8 − 5 + 1 = 4
Un simple análisis de grados de libertad, en cualquier sistema, puede ayudar a definir las variables y revelar dónde deben ubicarse los sensores críticos para el control de procesos. Este tipo de análisis también minimiza el diseño de demasiados sensores, actuadores y válvulas, que en teoría pueden controlar y regular la misma variable.
Opciones de sensores y actuadores
Las corrientes de producto, el vapor del calderín y la corriente de reflujo deben tener sensores/transmisores de flujo para que cada flujo pueda ajustarse para cumplir con los objetivos de control de la columna. También se debe colocar un sensor de flujo en la corriente de alimentación porque las perturbaciones en el caudal de alimentación son comunes. Cada sensor de flujo debe estar conectado a una válvula de flujo para controlar la corriente correspondiente.
También se deben usar sensores/transmisores de nivel de presión diferencial para el acumulador (el recipiente que recoge el destilado condensado) y el fondo de la columna porque mantener estos niveles es esencial para un funcionamiento confiable de la columna. Si la inundación es un problema, un diferencial de presión a través de la columna debería indicar el inicio de las inundaciones. Se debe instalar un indicador de presión en la parte superior del acumulador para monitorear la presión de la columna. La temperatura en una columna de destilación se controla típicamente manipulando el flujo de vapor al calderín.
Esquemas de Control
Hay una serie de esquemas de control comunes para columnas de destilación. De manera óptima, una columna de destilación debe funcionar con doble control de composición porque ahorra energía. En el control de composición dual, se controla la temperatura de ambos productos químicos en una destilación binaria. El sistema es más complejo de configurar y las mediciones necesarias para el control pueden ser difíciles. Como resultado, muchas columnas de destilación utilizan control de composición única en su lugar. Las configuraciones de control comunes para las columnas de destilación incluyen reflujo, hervimiento y destilado.
En la configuración de reflujo-hervido, la composición del destilado y la composición del fondo son las variables control. El flujo de reflujo y el control de entrada de calor (hervido de vapor) son las variables manipuladas, que permiten controlar los caudales de líquido y vapor en la columna. Con este sistema de control, es posible una respuesta rápida a los cambios en la composición del alimento. En la configuración de control de destilado-hervido, el flujo de destilado y el hervido de vapor se utilizan para controlar la composición. Esta configuración es una mejor opción para columnas donde la relación de reflujo es alta.
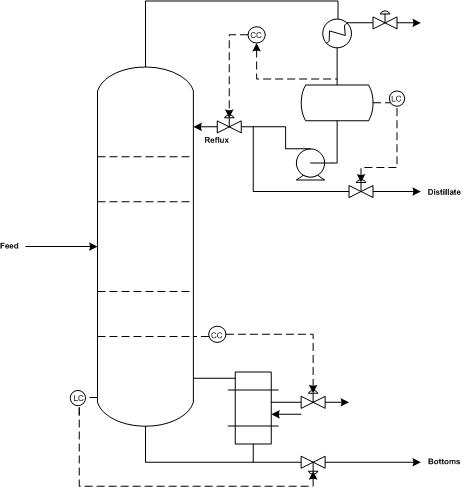
Reactor (Reacción Exotérmica en CSTR)
Al implementar controles en sistemas reactivos, la temperatura es un buen indicador para el rendimiento de la unidad. La temperatura suele estar relacionada con la velocidad de reacción y varía con el tiempo en la mayoría de los reactores. Sin embargo, a menudo se desea una corriente de salida del reactor con una temperatura constante aguas abajo en el proceso.
En una reacción exotérmica en un CSTR, las temperaturas iniciales más bajas dan como resultado menores velocidades de reacción y baja generación de calor. A medida que avanza la reacción, la generación de calor aumenta rápidamente debido a mayores velocidades de reacción y altas concentraciones de reactivos. A medida que disminuye la concentración de reactivos, la generación de calor vuelve a ser baja. Las temperaturas exotérmicas del reactor deben controlarse para asegurar un funcionamiento estable del reactor.
Para eliminar el calor de una reacción exotérmica, se emplean principios básicos de transferencia de calor. Un refrigerante se bombea a través de una carcasa fuera del reactor. Dado que la eliminación de calor es lineal, se debe controlar la temperatura del refrigerante. Al hacer esto, es posible aumentar la fuerza impulsora para la transferencia de calor para ralentizar una reacción, o por el contrario, permitir que la reacción avance aún más al disminuir la fuerza impulsora para la transferencia de calor.
Análisis Grados de Libertad
Para determinar dónde colocar controles, sensores y válvulas en una operación de reacción exotérmica, puede ser útil un análisis de grados de libertad, similar al realizado en la sección 3.2 de destilación.
Un CSTR típico contiene las siguientes corrientes: reactivo A (1), reactivo B (2), producto (3) y refrigerante a la camisa (4). No hay localizaciones donde haya dos fases, vapor y líquido, presentes en equilibrio -suponiendo que la reacción sea fase líquida sin evaporación o sublimación simultáneas.
DOF = Flujos − ExtraFases + 1
DOF = 4 − 0 + 1 = 5
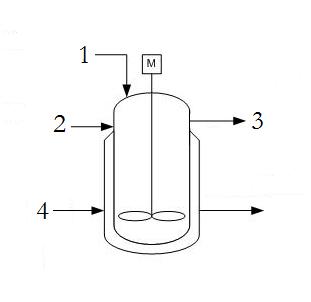
Dado que en la mayoría de las aplicaciones prácticas los reactivos (1 y 2) así como los caudales del producto (3) están definidos por la demanda del producto, solo hay 2 grados de libertad que permiten la colocación de 2 válvulas o controladores en la corriente de refrigerante (4) así como una de las corrientes de reactivos (1 o 2). Solo es necesario especificar una de las corrientes de reactivos, ya que la otra puede ser determinada por un controlador de relación usando coeficientes estequiométricos.
Esquemas de Control
Como se discutió anteriormente, se puede colocar una válvula en la corriente de entrada de refrigerante para garantizar un control adecuado de la temperatura del reactor. Al controlar la corriente de refrigerante en función de las condiciones de entrada de las corrientes de reactivos, el control puede responder rápidamente. Pero, si el refrigerante se controla en función de las condiciones de salida de la corriente de producto, hay un retraso en la respuesta, pero es fácil monitorear el rendimiento de la transferencia de calor.
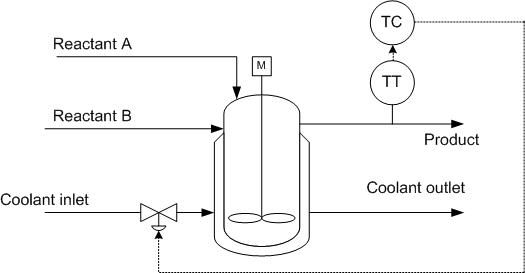
Para traducir este ejemplo en una reacción endotérmica, el flujo de refrigerante simplemente se traduciría en flujo de vapor con el fin de proporcionar calor a la reacción a través de la camisa CSTR.
Otros equipos de proceso comunes
Más allá de los intercambiadores de calor, reactores y columnas de destilación, muchos otros equipos de proceso, incluidos hornos, compresores, decantadores, refrigeradores, extractores líquido-líquido (LLs) y evaporadores, están sujetos a perturbaciones y requieren un control cuidadoso.
Hornos
Por ejemplo, los hornos pueden estar sujetos a frecuentes cambios de carga ya que un proceso o cliente requiere más energía. Para hacer frente a estas demandas, la temperatura de la corriente de salida debe ser monitoreada y manipulada. La información de un controlador de temperatura en la corriente de salida se puede utilizar para efectuar cambios en las válvulas que controlan el caudal de aire y combustible al horno. En este punto, se debe considerar la mejor configuración del sistema de control a la luz de factores como la seguridad, el tiempo de retraso para que ocurran cambios y el desgaste del equipo. Para un horno, los controles generalmente deben establecerse de manera que un exceso de aire sea más probable que un exceso de combustible. Esto reduce el riesgo de explosión debido al llenado del horno con combustible sin combustión.
Extractores Líquido-Líquido
En los extractores líquido-líquido, el nivel de interfaz y la presión son las variables controladas. Las perturbaciones en el caudal de la corriente entrante pueden afectar el nivel de la interfaz y evitar la separación completa de los componentes pesados y ligeros. A partir de esto, es obvio que debe haber controles de válvula en ambas corrientes de salida. El mejor esquema de control depende de la operación del proceso. Cuando la fase pesada es continua (la fase ligera fluye hacia arriba a través de la fase pesada), los cambios en el nivel de la interfaz deben controlarse ajustando el caudal del producto ligero, mientras que la presión se controla ajustando el caudal del producto pesado fuera de la columna. La Figura A es una representación de lo que ocurre en un extractor de una sola etapa. Generalmente, los extractores de una sola etapa se utilizan en laboratorios químicos, donde como extractores multietapa se utilizan en la industria. Un extractor multietapa utiliza la corriente de líquido inmiscible de la etapa anterior como alimentación en la siguiente etapa. La Figura 6 representa el esquema de control descrito anteriormente.
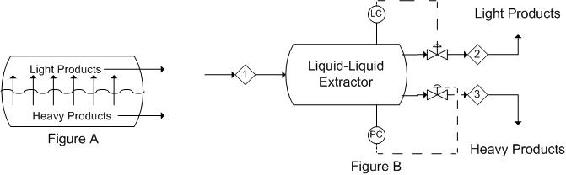
Cuando la fase ligera es continua, el sistema de control debe estar configurado de manera opuesta. La Figura C es nuevamente una representación de lo que ocurre en un extractor de una sola etapa. La Figura D es una representación de un esquema de control que podría implementarse. Esto es lo contrario del esquema de control en la Figura 6.
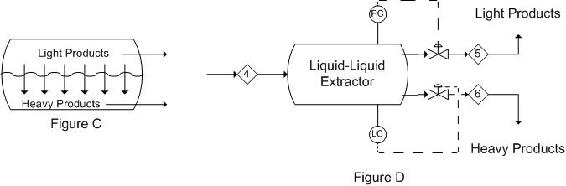
Estas representaciones son solo dos posibilidades para esquemas de control básicos que pueden implementarse en un proceso ya que existen varios controladores y aspectos de los procesos específicos que pueden necesitar ser controlados o monitoreados.
Compresores
Los compresores son otro componente valioso en el diseño de procesos. Permiten la reducción del volumen de una corriente entrante al aumentar la presión a la que se mantiene la corriente. También se pueden utilizar para bombear líquidos a través del proceso, ya que los líquidos son compresores altamente incompresibles no se pueden usar para la reducción de volumen. Para ello, debe existir un sistema de control específico como para evitar efectos adversos debidos a presiones extremadamente altas o bajas. Existen varios tipos de compresores, entre ellos: dinámicos, axiales y rotativos [1] por nombrar algunos. Debido a que el aumento de presión se rige por la ley de gas ideal, hay más a menudo y aumento de temperatura también. Esto se puede dejar tal cual, o enviar a un intercambiador de calor para la reducción de la temperatura. Los intercambiadores de calor se discutieron anteriormente.
Un ejemplo de ello es el uso de un compresor centrífugo para reducir el volumen de una corriente de combustible para almacenamiento. El uso de un compresor permitirá la reducción de volumen ya que los gases se comprimen fácilmente, esto también es económicamente amigable ya que reduce el tamaño del tanque necesario para almacenar la corriente de combustible. El tanque también debe estar equipado con una válvula reductora de presión, para devolver la corriente a la presión deseada, dependiendo del proceso. Un diagrama de este esquema es el siguiente:
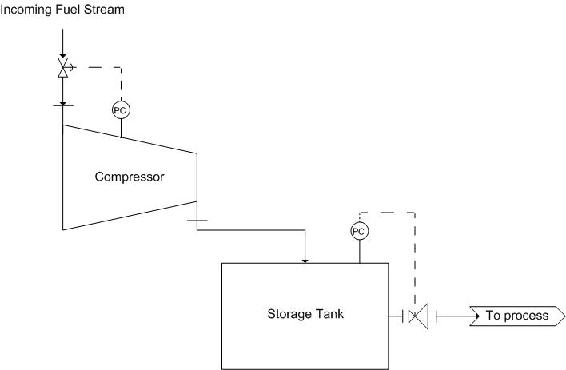
El controlador de presión en el compresor controla la válvula en la corriente de combustible entrante. Esto asegura que si hay una acumulación de presión, el flujo hacia el sistema se detendrá a tiempo. Además, se debe colocar un controlador de presión en el tanque de almacenamiento. Esto es controlado por la válvula reductora de presión mencionada anteriormente.
Decánters
Los decantadores, al igual que los extractores líquido-líquido, utilizan la solubilidad como principio de separación. A diferencia de la extracción líquido-líquido, estas requieren algún tiempo para que se produzca la separación. Generalmente, la separación es una separación líquido-líquido o líquido-sólido. Los decantadores son ampliamente utilizados en la industria del vino para separar los sedimentos del vino. Utilizando el ejemplo de separación de vino, un posible esquema de control es el siguiente. Aquí, solo hay un sensor de nivel en el decantador ya que es una separación líquido-sólido. Tenga en cuenta que existe una corriente de liberación, utilizada para eliminar los sedimentos recolectados. También se podría utilizar aquí un sensor analítico o de pH para mantener la química o el pH correctos, ya que el vino es el producto final. También es importante señalar que la colocación exacta del sensor de nivel variaría dependiendo del nivel deseado en el tanque. Aquí, el sensor de nivel no se muestra en su ubicación exacta.
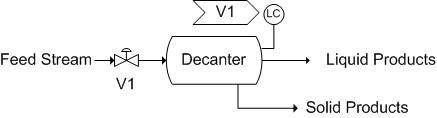
Otro buque que es muy similar a los decantadores son los tambores nocaut. Estos recipientes generalmente se localizan después de intercambiadores de calor u otros equipos que resultan en un sistema multifásico. Estos recipientes se utilizan para separar las dos fases, generalmente la separación de gas y líquido. A continuación se representa un posible esquema de control. La corriente entrante es una mezcla líquido-gas procedente de un intercambiador de calor. Por lo tanto, hay un sensor de presión en el tambor de extracción. Se podría usar un controlador de nivel, pero esto está midiendo efectivamente lo mismo, por lo que se ha omitido. Además, debido a que proviene de un intercambiador de calor, se ha incluido un controlador de temperatura para controlar la cantidad de enfriamiento que tiene lugar en el intercambiador de calor.
El controlador de presión (PC) controla V2, la corriente hacia el tanque. El controlador de temperatura (TC) controla V1, la válvula en la corriente de refrigerante al intercambiador de calor.
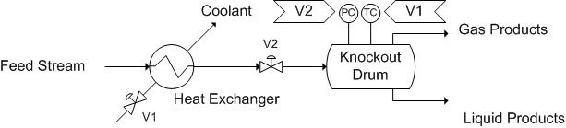
Estos ejemplos ilustran el método típico de localización de sistemas de control para equipos de proceso. Después de elegir la ubicación de las válvulas en función de las restricciones del proceso, aún quedan varias posibilidades para la manera real en la que controlar las válvulas. El tiempo de retraso para los cambios puede ser más largo para ciertas configuraciones, mientras que el peligro de dañar el equipo es menor. La configuración de los controles dependerá en gran medida de las preocupaciones de seguridad asociadas con un proceso específico.
Selección de controles y sus ubicaciones para un proceso de unidades múltiples
Se deben seguir los siguientes pasos al configurar controles para procesos multiunitarios. Para obtener descripciones más detalladas, consulte el Método paso a paso para describir los controles y su propósito.
- Determinar los objetivos del proceso, tomando en consideración las especificaciones del producto, las limitaciones económicas, las regulaciones ambientales y de seguridad, etc.
- Identificar límites para el funcionamiento normal. Estos pueden basarse en limitaciones de equipos, preocupaciones de seguridad, regulaciones ambientales y los objetivos económicos de los procesos.
- Identificar unidades y arroyos en el proceso que sean susceptibles a perturbaciones significativas. Estas perturbaciones ocurren comúnmente en corrientes de alimentación, corrientes de producto y recipientes de reactor, pero pueden estar presentes en cualquier lugar donde la temperatura o la presión u otras variables estén cambiando.
- Seleccione los tipos y ubicaciones de los sensores para medir y monitorear adecuadamente las variables críticas del proceso.
- Determinar los tipos y ubicaciones apropiados para las válvulas de control con el fin de ajustar adecuadamente las variables de proceso para que permanezcan dentro de los límites normales de operación. Deben establecerse controles para minimizar el tiempo de respuesta entre detectar un cambio y tomar acciones correctivas. La ubicación ideal para cualquier control dado depende de la unidad o unidades de proceso que afecte.
- Realizar un análisis de grado de libertad.
- Consideraciones Energéticas. Se debe realizar un balance energético para el proceso. Este paso implica el transporte de energía hacia y desde las unidades de proceso. Esto puede incluir eliminar el calor generado por un reactor y usarlo en otra parte del proceso. Las válvulas de control ayudarán a regular el flujo de tales corrientes.
- Controle la tasa de producción del proceso y otros parámetros operativos. Ajustar las entradas del proceso, como las velocidades de alimentación de los reactivos, puede alterar otras variables en el proceso. Los controles de proceso deben ser capaces de responder a estos ajustes para mantener el sistema dentro de los límites operativos.
- Configure el sistema de control para manejar las perturbaciones y minimizar sus efectos. (Consulte Controles de procesos químicos > Control PID)
- Monitorear Balanzas de Componentes. La acumulación de materiales dentro de un sistema no es deseable y puede conducir a ineficiencia en el proceso o falla catastrófica.
- Controlar las operaciones de las unidades individuales. Cada unidad de un proceso multiunidad necesita ser controlada individualmente para que el control de todo el sistema sea posible.
- Optimizar el proceso. Si el sistema tiene grados de libertad, las variables de proceso pueden ser manipuladas para crear producto de manera más eficiente o económica.
Considere la siguiente reacción en un reactor semi-discontinuo:
\[\ce{(CH3CO)2O + H2O -> 2CH3COOH} \nonumber \]
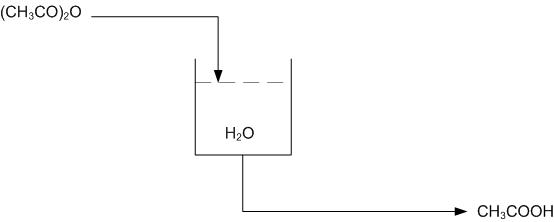
El objetivo es producir\(\ce{CH3COOH}\) a una concentración dada, es decir 15-20%. El tanque también se debe drenar una vez que se logre la concentración dada y la reacción haya llegado a su finalización. El tanque solo puede contener un volumen especificado y el 80% está lleno de agua. La reacción debe realizarse en exceso de agua. Una vez que una cantidad dada de anhídrido acético ha entrado en el reactor, se debe dejar en el tanque hasta que la reacción haya llegado a su finalización. La finalización de la reacción se puede determinar por la temperatura, ya que la reacción es exotérmica.
Usando el diseño del controlador de unidades múltiples desde arriba, determine la ubicación de los sensores y válvulas necesarios en el diagrama de flujo.
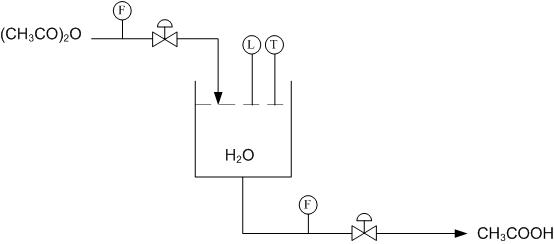
Utilizando la Figura E-2 se determina cómo usar los sensores de nivel y temperatura para limitar la cantidad de anhídrido acético que ingresa al reactor y también cómo drenar el sistema una vez que la reacción ha llegado a su finalización.
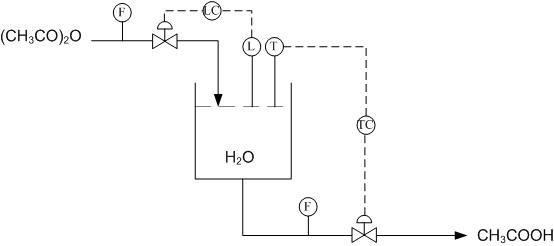
Usando el sistema anterior, cuando la cantidad correcta de anhídrido acético haya entrado en el reactor, el sensor de nivel detendrá el flujo hacia el reactor. Una vez que la reacción ha llegado a su finalización y se ha activado el sensor de temperatura, debido a un pico de temperaturas de la reacción exotérmica, el tanque drenará.
Examine la siguiente figura, que muestra dos esquemas de control diferentes para un intercambiador de calor. La temperatura de la corriente de salida debe permanecer constante. ¿Cómo se logra este objetivo utilizando los sistemas de control que se muestran a continuación? ¿Qué corriente es la corriente manipulada? ¿Cuáles son las ventajas y desventajas de cada configuración?
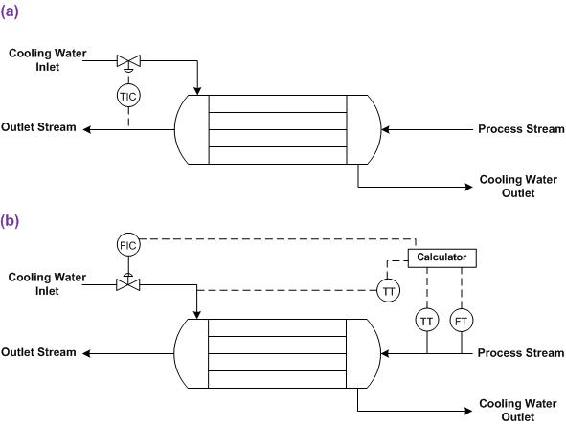
Solución
En ambas configuraciones, el flujo de agua de refrigeración se manipula para controlar la temperatura de la corriente de salida. La estrategia de control para cada intercambiador de calor es diferente.
La Figura E-4 (a) muestra un intercambiador de calor donde el flujo de agua de refrigeración se ajusta en función de la temperatura de la corriente de salida. La ventaja de esta configuración es que es bastante sencilla y no se tiene que identificar la causa del cambio en la temperatura de la corriente de salida. La desventaja es que ya se ha producido un cambio de temperatura antes de tomar medidas, y si el tiempo de retraso para que el agua de enfriamiento adicional enfríe la corriente del proceso es largo, la temperatura de la corriente de salida puede ser inconsistente.
La Figura E-4 (b) muestra un intercambiador de calor donde el flujo de agua de refrigeración se ajusta en función del caudal y la temperatura de la corriente de entrada y la temperatura de la corriente de refrigerante. En base a un conjunto de cálculos que utilizan el coeficiente de transferencia de calor del intercambiador de calor, se puede predecir la temperatura de la corriente de salida. La ventaja de este sistema es que se toman medidas antes de que ocurran cambios en la temperatura de la corriente de salida. La desventaja es que si la capacidad real de intercambio de calor difiere del valor esperado debido a incrustaciones o problemas mecánicos, la temperatura de salida no será correcta.
Esto presenta una notación alternativa de controles. Las flechas sobre el controlador indican qué partes del proceso controla el controlador.
\[\ce{A + B -> AB} \nonumber \]
- B se añade lentamente en una carga completa de A
- La temperatura se mantiene a TR (temperatura RXN)
- Una vez finalizada la reacción, el AB se enfría a TP
- Se agrega C a AB para hacer el producto final, que sale del tanque
Solución
- LC1: Esto controla M1 y V1.
Este controlador se utiliza para mantener el nivel de A en el tanque A por encima de un mínimo preestablecido.
- LC2: Esto controla M2 y V2.
Este controlador se utiliza para mantener el nivel de B en el tanque B por encima de un mínimo preestablecido.
- LC3: Esto controla M3 y V3.
Este controlador se utiliza para mantener el nivel de C en el tanque C por encima de un mínimo preestablecido.
- FC1: Esto también controla M1 y V1.
Este controlador totaliza la cantidad de A que ha fluido fuera del tanque A, y apaga el flujo cuando la cantidad de flujo ha alcanzado un valor preestablecido.
- FC2: Esto también controla M2 y V2.
Este controlador totaliza la cantidad de B que ha fluido fuera del tanque B, y apaga el flujo cuando la cantidad de flujo ha alcanzado un valor preestablecido.
- FC3: Esto también controla M3 y V3.
Este controlador totaliza la cantidad de C que ha fluido fuera del tanque C, y apaga el flujo cuando la cantidad de flujo ha alcanzado un valor preestablecido.
- LC4: Esto controla V1, V4, M4 y M5.
V1 - Si el nivel de líquido en el tanque de reacción supera un máximo preestablecido, V1 se cierra.
V4 - Si el nivel de líquido en el tanque de reacción pasa por debajo de un mínimo preestablecido, V4 está cerrado.
M4 - Si el nivel de líquido en el tanque de reacción pasa por debajo de un mínimo preestablecido, M4 se apaga.
M5 - Si el nivel de líquido en el tanque de reacción pasa por debajo del nivel del agitador, M5 se apaga.
- TC1: Esto controla V3, V5 y M3.
M3, V3 - Si la temperatura en el tanque de reacción está en TP, M3 se enciende y V3 se abre.
V5 - Para mantener la temperatura en el tanque de reacción en TP, V5 se abre y cierra en consecuencia.
Referencias
- Bequette, W.B. Control de Procesos Modelado Diseño y Simulción. , Nueva Jersey: Prentice Hall, pp 466-477
- Luyben, W.L. Control de Procesos en Toda la Planta. , Nueva York: McGraw-Hill, pp 53-69, pp 201-203, pp 235-247
- Módulo 3.1: Control de Columnas de Destilación. El HyperCourse ECOSSE IGDS Controls. Universidad de Edimburgo, Escocia.
- Ogunnaike, Babatunde A. Dinámica, modelado y control de procesos, Nueva York: Oxford University Press 1994, pp 1149-1153
- Riggs, James B. Control de Procesos Químicos y Bioprocesos. , Ferret Publishing, pp 491-504
- Turton, Richard. Análisis, síntesis y diseño de un proceso químico, New Jersey: Prentice Hall, pp 408-409
- Junta de Investigación de Riesgos y Seguridad Química de Estados Unidos; “Morton International Explosion”. www.csb.gov/completed_investigations/docs/mortondigest.pdf. Última Actualización 07/17/2003.
- Tompkins, Bill. “Reacción y acción.” www.ehponline.org/members/2004/112-6/focus.html. Última actualización 09/09/2007
- Wikipedia. “Compresores de Gas” http://en.Wikipedia.org/wiki/Gas_compressor. Última actualización 11/27/2008
- Wikipedia. “Extracción líquido-líquido” es.wikipedia.org/wiki/Extracción líquido-líquido-líquido. Última actualización 20/11/2008
Colaboradores y Atribuciones
- Autores: Christopher Bauman, Jennifer DeHeck, Merrick Miranda, Evan Leonard
- Administradores: Robert Chockley, Chloe Sweet, Irene Brockman, Scott Dombrowski
- Anclajes: Megan Boekeloo, Stacy Young