22.5: Reducción de Metales
- Page ID
- 76130
La facilidad con la que se puede obtener un metal de su mineral varía considerablemente de un metal a otro. Dado que la mayoría de los minerales son óxidos o pueden convertirse en óxidos por tostado, el cambio de energía libre que acompaña a la descomposición del óxido forma una medida conveniente de la facilidad con la que se puede obtener un metal de su mineral. Los valores del cambio de energía libre por mol O 2 producido se dan en la tabla para una muestra representativa de metales a 298 y 2000 K. Un alto valor positivo de Δ G m° en esta tabla indica un óxido muy estable del que es difícil eliminar el oxígeno y obtener el metal, mientras que un valor negativo de Δ G m° indica un óxido que se descompondrá espontáneamente en sus elementos. Observe cómo el valor de Δ G m° disminuye con la temperatura en cada caso. Esto se debe a que un gas (oxígeno) es producido por la descomposición, y ΔS es consecuentemente positivo.
Reacción | ΔG m° (298 K) /kJ mol —1 | ΔG m° (2000 K) /kJ mol —1 |
---|---|---|
\(\frac{2}{3} \ce{Al2O3 \rightarrow \frac{4}{3} AlO_2}\) |
+1054
|
+691
|
\(\ce{2MgO -> 2Mg + O2}\) |
+1138
|
+643
|
\(\tfrac{2}{3}\ce{Fe2O3} \rightarrow \tfrac{4}{3}\ce{Fe + O2}\) |
+744
|
+314
|
\(\text{SnO}_2 \rightarrow \text{Sn} + \text{O}_2\) |
+520
|
+42
|
\(\ce{2HgO -> 2Hg + O2}\) |
+118
|
—381
|
\(\ce{2Ag2O -> 4Ag + O2}\) |
+22
|
—331
|
|
||
\(\text{C}(s) + \text{O}_2(g) \rightarrow \text{CO}_2(g)\) |
—394
|
—396
|
Los dos metales de la tabla que son más fáciles de obtener de sus minerales de óxido son Hg y Ag. Dado que el valor Δ G m° para la descomposición de estos óxidos se vuelve negativo cuando se eleva la temperatura, el simple calentamiento hará que se rompan en O 2 y el metal. Los siguientes metales más fáciles de obtener son Sn y Fe. Estos pueden ser reducidos por coque, una forma impura de C obtenida calentando carbón. El coque es el agente reductor más barato fácilmente obtenible que se puede utilizar en metalurgia. Cuando C se oxida a CO 2, el cambio de energía libre es cercano a — 395 kJ mol —1 en un amplio rango de temperaturas. Esta caída en la energía libre no es suficiente para compensar el aumento de energía libre cuando Fe 2 O 3 y SnO 2 se descomponen a 298 K, pero es más que suficiente si la temperatura es de 2000 K. Así, por ejemplo, si Fe 2 O 3 se reduce en C a 2000 K, tenemos, de Ley de Hess,
\({}_{\text{3}}^{\text{2}}\text{Fe}_{\text{2}}\text{O}_{\text{3}}\text{(}s\text{) }\to \text{ }{}_{\text{3}}^{\text{4}}\text{Fe(}l\text{) + O}_{\text{2}}\text{(}g\text{)}\)Δ G m° = +314 kJ mol —1
\(\text{C(}s\text{) + O}_{\text{2}}\text{(}g\text{)}\to \text{ CO}_{\text{2}}\text{(}g\text{)}\)Δ G m° = —394 kJ mol —1
\({}_{\text{3}}^{\text{2}}\text{Fe}_{\text{2}}\text{O}_{\text{3}}\text{(}s\text{) + C(}s\text{) }\to \text{ }{}_{\text{3}}^{\text{4}}\text{Fe(}l\text{) + CO}_{\text{2}}\)Δ G m° = —82 kJ mol —1
Así pues, Δ G m° para la reducción es negativa, y la reacción es espontánea.
Los dos metales de la tabla que son más difíciles de obtener de sus minerales son Mg y Al. Dado que no pueden ser reducidos por C o cualquier otro agente reductor barato fácilmente disponible, deben reducirse electrolíticamente. La reducción electrolítica de bauxita para producir Al (el proceso Hall) se utiliza para producir aluminio.
Reducción de Hierro
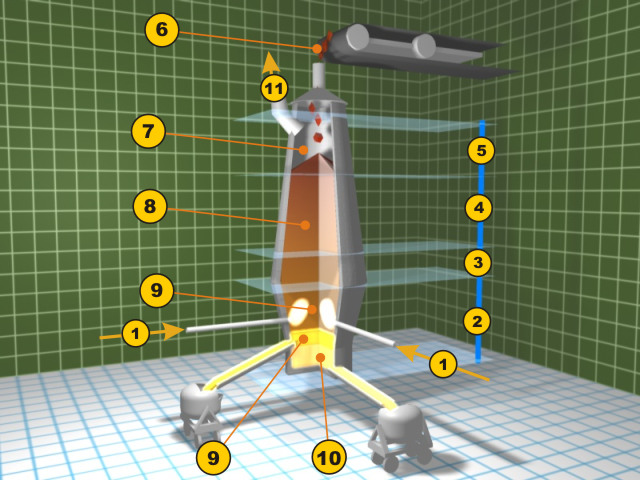
Dado que el hierro es el metal más importante en nuestra civilización industrial, su reducción del mineral de hierro en un alto horno (Figura\(\PageIndex{1}\)) merece una descripción detallada. Los óxidos presentes en la mayoría de los minerales de hierro son Fe 2 O 3 y Fe 3 O 4. Estos óxidos se reducen paso a paso: primero a FeO y luego a Fe. El mineral, el coque y la piedra caliza se cargan al horno a través de un par de válvulas tipo bloqueo de aire en la parte superior. Cerca del fondo entra una ráfaga de aire, precalentada a 900 a 1000 K, a través de sopletes llamados tuyères. El oxígeno de la ráfaga de aire reacciona con el carbono en el coque para formar monóxido de carbono y dióxido de carbono, liberando calor considerable. La ráfaga transporta estos gases a través del mineral, el coque y la piedra caliza, y salen por la parte superior del horno.
Para cuando el mineral trabaja su camino hacia la parte inferior del horno, la mayor parte del Fe 2 O 3 ya se ha reducido a FeO. En esta región, las temperaturas alcanzan los 1600 a 2000 K, lo suficientemente altas como para fundir el FeO y ponerlo en contacto cercano con el coque. La mayor parte del FeO se reduce por reacción directa con carbono, siendo este último oxidado a monóxido de carbono:
\[\text{2C}(s) + \text{2FeO}(l) \rightarrow \text{2Fe}(l) + \text{2CO} \triangle G_m^o(2000 k) = -280 \frac{kJ}{mol} \nonumber \]
El hierro fundido producido por esta reacción gotea al fondo del horno donde se recoge y ocasionalmente se extrae.
Más altas en el horno, las temperaturas caen por debajo de los puntos de fusión de los óxidos de hierro. Debido a que hay poco contacto entre los trozos sólidos de mineral y de coque, la reducción directa por carbono sólido es bastante lenta. Sin embargo, el monóxido de carbono gaseoso entra en contacto con todas las partes del mineral y reacciona mucho más rápidamente:
\[\text{CO}(g) + \text{Fe}_2\text{O}_3(s) \rightarrow \text{CO}_2 (g) \text{2FeO}(s) \nonumber \]
\(\text{CO}(g) + \text{FeO}(s) \rightarrow \text{CO}_2(g) + \text{Fe}(s)\)
Así, gran parte de la “reducción de carbono” en la fabricación de hierro se lleva a cabo en realidad por monóxido de carbono.
La ganga en mineral de hierro consiste principalmente en silicatos y sílice, SiO 2. Estas impurezas se eliminan en escoria. La piedra caliza añadida con coque y mineral es calcinada (descompuesta al óxido) por las altas temperaturas del alto horno:
\[\text{CaCO}_3(s) \underset{\text{1100 K}}{\mathop{\rightarrow}}\, \text{CaO}(s) + \text{CO}_2(g) \nonumber \]
La cal (CaO) sirve como fundente, reduciendo los puntos de fusión (mp) de la sílice (SiO 2) y los silicatos:
\[\underset{\text{mp = 2853 K}}{\mathop{\text{CaO(}s\text{)}}}\,\text{ + }\underset{\text{mp = 1986 K}}{\mathop{\text{SiO}_{\text{2}}\text{(}s\text{)}}}\,\text{ }\to \text{ }\underset{\text{mp = 1813 K}}{\mathop{\text{CaSiO}_{\text{3}}\text{(}l\text{)}}} \nonumber \]
Los silicatos líquidos fluyen rápidamente hacia abajo a través de la parte más caliente del horno. Esto ayuda a evitar la reducción de sílice a silicio, produciendo de ahí un hierro más puro. La escoria es menos densa que el hierro fundido e inmiscible con él. Por lo tanto, la escoria flota en la superficie del hierro y se puede extraer fácilmente.
Aunque la mayoría del hierro de alto horno ahora va directamente a un horno de fabricación de acero en forma fundida, gran parte de él solía funcionar en moldes donde se endureció en pequeños lingotes llamados cerdos debido a su forma. En consecuencia, el hierro de alto horno todavía se conoce como arrabio. Un solo alto horno grande puede producir más de 10 6 kg de hierro por día. Por cada kilogramo de hierro, se requieren 2 kg de mineral de hierro, 1 kg de coque, 0.3 kg de piedra caliza, 4 kg de aire, 63 kg de agua y 19 MJ de energía de combustibles fósiles. El horno produce 0.6 kg de escoria y 5.7 kg, gas de combustión por kg de hierro. Casi el 5 por ciento del mineral de hierro se pierde en forma de pequeñas partículas suspendidas en el gas de combustión a menos que, como en el horno que se muestra en la Figura 1, se instalen controles de contaminación del aire. Estos últimos atrapan partículas de FeO para su reciclaje al horno y también hacen que el gas de combustión (que contiene aproximadamente 12% de CO y 1% H 2) sea adecuado como combustible para precalentar el aire alimentado a las tuyères. Así, el control de la contaminación del aire de alto horno (uno de los principales contribuyentes a la reputación de “ciudad ahumada” de Pittsburgh, Pensilvania y Gary, Indiana) también conserva los suministros de mineral y los recursos energéticos.