5.1: Producción de Plantas en Ambientes Controlados
- Page ID
- 80882
\( \newcommand{\vecs}[1]{\overset { \scriptstyle \rightharpoonup} {\mathbf{#1}} } \)
\( \newcommand{\vecd}[1]{\overset{-\!-\!\rightharpoonup}{\vphantom{a}\smash {#1}}} \)
\( \newcommand{\id}{\mathrm{id}}\) \( \newcommand{\Span}{\mathrm{span}}\)
( \newcommand{\kernel}{\mathrm{null}\,}\) \( \newcommand{\range}{\mathrm{range}\,}\)
\( \newcommand{\RealPart}{\mathrm{Re}}\) \( \newcommand{\ImaginaryPart}{\mathrm{Im}}\)
\( \newcommand{\Argument}{\mathrm{Arg}}\) \( \newcommand{\norm}[1]{\| #1 \|}\)
\( \newcommand{\inner}[2]{\langle #1, #2 \rangle}\)
\( \newcommand{\Span}{\mathrm{span}}\)
\( \newcommand{\id}{\mathrm{id}}\)
\( \newcommand{\Span}{\mathrm{span}}\)
\( \newcommand{\kernel}{\mathrm{null}\,}\)
\( \newcommand{\range}{\mathrm{range}\,}\)
\( \newcommand{\RealPart}{\mathrm{Re}}\)
\( \newcommand{\ImaginaryPart}{\mathrm{Im}}\)
\( \newcommand{\Argument}{\mathrm{Arg}}\)
\( \newcommand{\norm}[1]{\| #1 \|}\)
\( \newcommand{\inner}[2]{\langle #1, #2 \rangle}\)
\( \newcommand{\Span}{\mathrm{span}}\) \( \newcommand{\AA}{\unicode[.8,0]{x212B}}\)
\( \newcommand{\vectorA}[1]{\vec{#1}} % arrow\)
\( \newcommand{\vectorAt}[1]{\vec{\text{#1}}} % arrow\)
\( \newcommand{\vectorB}[1]{\overset { \scriptstyle \rightharpoonup} {\mathbf{#1}} } \)
\( \newcommand{\vectorC}[1]{\textbf{#1}} \)
\( \newcommand{\vectorD}[1]{\overrightarrow{#1}} \)
\( \newcommand{\vectorDt}[1]{\overrightarrow{\text{#1}}} \)
\( \newcommand{\vectE}[1]{\overset{-\!-\!\rightharpoonup}{\vphantom{a}\smash{\mathbf {#1}}}} \)
\( \newcommand{\vecs}[1]{\overset { \scriptstyle \rightharpoonup} {\mathbf{#1}} } \)
\( \newcommand{\vecd}[1]{\overset{-\!-\!\rightharpoonup}{\vphantom{a}\smash {#1}}} \)
\(\newcommand{\avec}{\mathbf a}\) \(\newcommand{\bvec}{\mathbf b}\) \(\newcommand{\cvec}{\mathbf c}\) \(\newcommand{\dvec}{\mathbf d}\) \(\newcommand{\dtil}{\widetilde{\mathbf d}}\) \(\newcommand{\evec}{\mathbf e}\) \(\newcommand{\fvec}{\mathbf f}\) \(\newcommand{\nvec}{\mathbf n}\) \(\newcommand{\pvec}{\mathbf p}\) \(\newcommand{\qvec}{\mathbf q}\) \(\newcommand{\svec}{\mathbf s}\) \(\newcommand{\tvec}{\mathbf t}\) \(\newcommand{\uvec}{\mathbf u}\) \(\newcommand{\vvec}{\mathbf v}\) \(\newcommand{\wvec}{\mathbf w}\) \(\newcommand{\xvec}{\mathbf x}\) \(\newcommand{\yvec}{\mathbf y}\) \(\newcommand{\zvec}{\mathbf z}\) \(\newcommand{\rvec}{\mathbf r}\) \(\newcommand{\mvec}{\mathbf m}\) \(\newcommand{\zerovec}{\mathbf 0}\) \(\newcommand{\onevec}{\mathbf 1}\) \(\newcommand{\real}{\mathbb R}\) \(\newcommand{\twovec}[2]{\left[\begin{array}{r}#1 \\ #2 \end{array}\right]}\) \(\newcommand{\ctwovec}[2]{\left[\begin{array}{c}#1 \\ #2 \end{array}\right]}\) \(\newcommand{\threevec}[3]{\left[\begin{array}{r}#1 \\ #2 \\ #3 \end{array}\right]}\) \(\newcommand{\cthreevec}[3]{\left[\begin{array}{c}#1 \\ #2 \\ #3 \end{array}\right]}\) \(\newcommand{\fourvec}[4]{\left[\begin{array}{r}#1 \\ #2 \\ #3 \\ #4 \end{array}\right]}\) \(\newcommand{\cfourvec}[4]{\left[\begin{array}{c}#1 \\ #2 \\ #3 \\ #4 \end{array}\right]}\) \(\newcommand{\fivevec}[5]{\left[\begin{array}{r}#1 \\ #2 \\ #3 \\ #4 \\ #5 \\ \end{array}\right]}\) \(\newcommand{\cfivevec}[5]{\left[\begin{array}{c}#1 \\ #2 \\ #3 \\ #4 \\ #5 \\ \end{array}\right]}\) \(\newcommand{\mattwo}[4]{\left[\begin{array}{rr}#1 \amp #2 \\ #3 \amp #4 \\ \end{array}\right]}\) \(\newcommand{\laspan}[1]{\text{Span}\{#1\}}\) \(\newcommand{\bcal}{\cal B}\) \(\newcommand{\ccal}{\cal C}\) \(\newcommand{\scal}{\cal S}\) \(\newcommand{\wcal}{\cal W}\) \(\newcommand{\ecal}{\cal E}\) \(\newcommand{\coords}[2]{\left\{#1\right\}_{#2}}\) \(\newcommand{\gray}[1]{\color{gray}{#1}}\) \(\newcommand{\lgray}[1]{\color{lightgray}{#1}}\) \(\newcommand{\rank}{\operatorname{rank}}\) \(\newcommand{\row}{\text{Row}}\) \(\newcommand{\col}{\text{Col}}\) \(\renewcommand{\row}{\text{Row}}\) \(\newcommand{\nul}{\text{Nul}}\) \(\newcommand{\var}{\text{Var}}\) \(\newcommand{\corr}{\text{corr}}\) \(\newcommand{\len}[1]{\left|#1\right|}\) \(\newcommand{\bbar}{\overline{\bvec}}\) \(\newcommand{\bhat}{\widehat{\bvec}}\) \(\newcommand{\bperp}{\bvec^\perp}\) \(\newcommand{\xhat}{\widehat{\xvec}}\) \(\newcommand{\vhat}{\widehat{\vvec}}\) \(\newcommand{\uhat}{\widehat{\uvec}}\) \(\newcommand{\what}{\widehat{\wvec}}\) \(\newcommand{\Sighat}{\widehat{\Sigma}}\) \(\newcommand{\lt}{<}\) \(\newcommand{\gt}{>}\) \(\newcommand{\amp}{&}\) \(\definecolor{fillinmathshade}{gray}{0.9}\)Timothy Shelford
Departamento de Ingeniería Biológica y Ambiental
Universidad de Cornell
Ithaca, NY, Estados Unidos
A. J. Ambos
Departamento de Ciencias Ambientales
Universidad de Rutgers
New Brunswick, Nueva Jersey, Estados Unidos
Términos Clave |
Gráfico psicrométrico | Sombreado | Ventilación |
Calefacción | Refrigeración mecánica | Costo de instalación |
Iluminación | Enfriamiento evaporativo | Costo de operación |
Variables
Introducción
La producción de cultivos en ambiente controlado implica el uso de estructuras y tecnologías para minimizar o eliminar el impacto potencialmente negativo del clima en el crecimiento y desarrollo de las plantas. Las estructuras comunes incluyen invernaderos (que pueden equiparse con una gama de tecnologías dependiendo de la economía, los cultivos cultivados y las preferencias de los productores) e instalaciones de cultivo en interiores (por ejemplo, cámaras de crecimiento, fábricas de plantas, contenedores de envío y granjas verticales en edificios de gran altura). Si bien cada tipo de instalación de cultivo tiene desafíos únicos, muchos de los procesos, principios y soluciones tecnológicas son similares. Este capítulo describe enfoques para el control ambiental en instalaciones de producción de plantas con un enfoque en las tecnologías utilizadas para la producción de cultivos y el control de la luz.
Resultados
Después de leer este capítulo, deberías poder:
- • Enumerar y explicar los desafíos críticos de control ambiental para la producción de plantas en entornos controlados
- • Realizar cálculos de diseño para sistemas utilizados para la producción de plantas en entornos controlados
- • Calcular las estimaciones de costos de instalación y operación de los sistemas de iluminación para la producción de plantas en ambientes controlados
Conceptos
Se desarrollaron invernaderos para extender la temporada de crecimiento en climas más fríos y para permitir la producción de plantas perennes que no sobrevivirían naturalmente a los fríos meses de invierno. Al proporcionar un ambiente óptimo para un cultivo, ya sea en un invernadero o en una instalación de cultivo interior, la temperatura del aire es un factor crítico que impacta el crecimiento y desarrollo de las plantas. Un factor igualmente importante y relacionado es el contenido de humedad del aire (expresado como humedad relativa). El crecimiento de las plantas depende de la transpiración, proceso por el cual el agua y los nutrientes de las raíces se extraen a través de la planta, culminando en la evaporación del agua a través de los estómagos ubicados en las hojas. (Los estómagos son pequeñas aberturas que permiten el intercambio de gases. Ellos son controlados activamente por la planta.) La transpiración del agua a través de los estomas también resulta en enfriamiento. En condiciones de alta humedad relativa, la planta es incapaz de transpirar de manera efectiva, lo que resulta en un crecimiento reducido y, en algunos casos, daños fisiológicos. Los productores buscan crear ambientes de cultivo ideales en invernaderos y otras instalaciones de cultivo en interiores mediante el control de calefacción, ventilación y enfriamiento (Both et al., 2015).
Gráfico Psicrométrico
El conocimiento de la relación entre temperatura y humedad relativa es crítico en el diseño de sistemas de calefacción, refrigeración y ventilación para mantener las condiciones ambientales deseadas dentro de las instalaciones de producción de la planta. La tabla psicrométrica (Figura 5.1.1) es una herramienta conveniente para ayudar a determinar las propiedades del aire húmedo. Con valores de solo dos parámetros (por ejemplo, temperatura de bulbo seco y humedad relativa, o temperaturas de bulbo seco y bulbo húmedo), se pueden leer otras propiedades del aire en la tabla (puede ser necesaria alguna interpolación). A continuación se describen las propiedades físicas fundamentales del aire utilizado en la tabla psicrométrica.
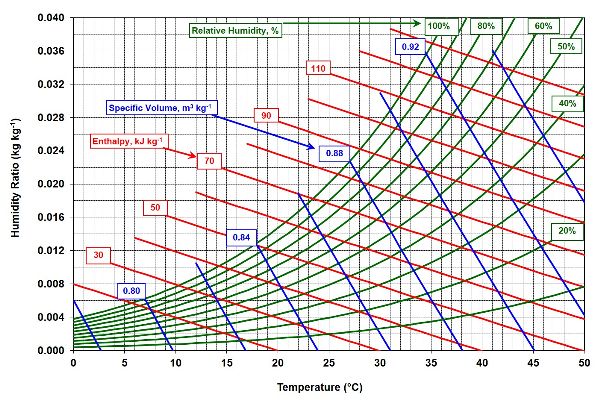
- • La temperatura de la bombilla seca (T db, °C) es la temperatura del aire medida con un termómetro regular. En una gráfica psicrométrica (Figura 5.1.1), la temperatura del bulbo seco se lee desde el eje horizontal.
- • La temperatura de bulbo húmedo (T wb, °C) es la temperatura del aire medida cuando el aire se enfría a saturación (es decir, 100% de humedad relativa) evaporando agua en él. La energía (calor latente) requerida para evaporar el agua proviene del aire mismo. La temperatura del bulbo húmedo se puede medir manteniendo la punta de detección de un termómetro húmeda (por ejemplo, rodeándolo con una mecha conectada a un depósito de agua) mientras el termómetro se mueve rápidamente a través del aire, o soplando aire a través de la punta de detección húmeda (y estacionaria). En un gráfico psicrométrico (Figura 5.1.1), la temperatura de bulbo húmedo se lee desde el eje horizontal siguiendo la línea de entalpía constante desde la condición inicial (por ejemplo, la intersección de la combinación de temperatura de bulbo seco y humedad relativa) hasta la línea de saturación (humedad relativa del 100%).
- • La temperatura del punto de rocío (T d, °C) es la temperatura del aire a la que se produce la condensación cuando se enfría el aire húmedo. En un gráfico psicrométrico (Figura 5.1.1), la temperatura del punto de rocío se lee desde el eje horizontal después de que una línea horizontal de relación de humedad constante se extiende desde la condición inicial (por ejemplo, la intersección de la combinación de temperatura de bulbo seco y humedad relativa) hasta la línea de saturación (100% relativo humedad).
- • La humedad relativa (HR,%) es el nivel de saturación del aire (con vapor de agua). En una gráfica psicrométrica (Figura 5.1.1), las líneas curvas son de humedad relativa constante.
- • La relación de humedad (kg kg −1) es la masa de vapor de agua evaporada en una masa unitaria de aire seco. En una gráfica psicrométrica (Figura 5.1.1), la relación de humedad se lee desde el eje vertical.
- • La entalpía (kJ kg −1) es el contenido energético de una masa unitaria de aire seco, incluyendo cualquier vapor de agua contenido. La gráfica psicrométrica (Figura 5.1.1) presenta típicamente líneas de entalpía constante.
- • Volumen específico (m 3 kg −1) es el volumen de una masa unitaria de aire seco; es el inverso de la densidad del aire. El gráfico psicrométrico (Figura 5.1.1) presenta líneas de volumen específico constante.
Calefacción
Un gasto importante de operar un invernadero durante todo el año en climas fríos es el costo de la calefacción. Por lo tanto, es importante comprender los principales modos de pérdida de calor al diseñar u operar un invernadero. La pérdida de calor se produce desde la estructura directamente a través de la conducción, convección y radiación. Dependiendo de la ubicación, al estimar las pérdidas de calor, puede ser necesario incluir la pérdida de calor alrededor del perímetro exterior, así como el impacto de altas velocidades del viento exterior y/o grandes diferencias de temperatura entre el interior y el exterior del invernadero (Aldrich y Bartok, 1994).
Estimación de las necesidades de calor
Estimar las pérdidas de calor por conducción, convección, radiación e infiltración, requiere tanto las temperaturas del aire interior como exterior. La temperatura del aire interior generalmente se basa en el punto de ajuste nocturno requerido por el cultivo. En ausencia de requerimientos específicos de cultivo, típicamente se pueden usar 16 °C como mínimo. Si el invernadero se va a usar durante todo el año, normalmente se usa la temperatura de bulbo seco de diseño invernal del 99% para la temperatura exterior. La temperatura de la bombilla seca de diseño invernal del 99% es la temperatura exterior que solo se supera el 1% del tiempo (con base en 30 años de datos de los meses de diciembre, enero y febrero recopilados en o cerca de la ubicación del invernadero). El término “excedido” en la frase anterior significa “más frío que”. Tales valores para muchas ubicaciones en todo el mundo son publicados por ASHRAE (2013).
El cálculo del intercambio de calor (por conducción, convección y radiación) es un proceso complejo que generalmente implica hacer muchas suposiciones simplificadoras. Las soluciones a menudo requieren cálculos iterativos que son tediosos sin la ayuda de herramientas informáticas. Los programas informáticos como EnergyPlus™ (Crawley, 2001) y Virtual Grower (USDA-ARS, 2019) están disponibles para los cálculos de pérdida de calor. Sin embargo, incluso los paquetes de software desarrollados para cálculos de pérdida de calor pueden no proporcionar necesariamente resultados precisos.
Otros métodos que simplifican enormemente la realización de cálculos de pérdida de calor utilizando coeficientes de transferencia de calor están disponibles. Los coeficientes de transferencia de calor combinan los efectos de conducción, convección y radiación en un solo coeficiente. Dado que estos procesos dependen de muchos factores distintos del diferencial de temperatura, su precisión no es alta, especialmente cuando las condiciones son extremas, o fuera de los rangos de operación típicos. Sin embargo, para estimaciones rápidas que no son computacionalmente intensivas, los cálculos basados en coeficientes pueden ser útiles para un diseñador u operador. La ecuación 5.1.1 proporciona un medio para resolver las pérdidas de calor conductivo, convectivo y radiativo:
\[ q_{ccr} = UA_{c}(t_{i} - t_{o}) \]
donde q ccr = pérdida de calor por conducción, convección y radiación (W)
U = coeficiente general de transferencia de calor (W m −2 °C −1)
A c = área de la superficie del invernadero (paredes y cubierta) (m 2)
t o = temperatura ambiente (exterior) del aire (°C); la temperatura de diseño del 99% se usa comúnmente para este parámetro (ver texto)
Los coeficientes generales de transferencia de calor para los materiales típicos de invernadero se enumeran en la Tabla 5.1.1.
La ecuación 5.1.2 es para resolver la pérdida de calor debida a la infiltración:
\[ q_{i} = \rho_{i} NV[c_{pi(t_{i}-t_{o})}+h_{fg}(W_{i}-W_{o})] \]
donde q i = pérdida de calor por infiltración (W)
ρ i = densidad del aire del invernadero (kg m −3)
N = tasa de infiltración (s −1)
V = volumen del invernadero (m 3)
c ρi = calor específico del aire del invernadero (J kg −1 °C −1)
t i = temperatura del aire del invernadero (interior) (°C)
t o = temperatura del aire exterior (°C)
h fg = calor latente de vaporización del agua a t i (J kg −1)
W i = relación de humedad del aire del invernadero (kg agua kg aire −1)
W o = relación de humedad del aire exterior (kg agua kg aire −1)
Cubierta de Invernadero | Valor U (W m −2 °C −1) |
---|---|
Un solo vidrio, sellado |
6.2 |
Vidrio simple, baja emisividad |
5.4 |
Doble vidrio, sellado |
3.7 |
Plástico individual |
6.2 |
Policarbonato simple, corrugado |
6.2—6.8 |
Fibra de vidrio simple, corrugada |
5.7 |
Polietileno doble |
4 |
Doble polietileno, IR inhibido |
2.8 |
Acrílico rígido, doble pared |
3.2 |
Policarbonato rígido, doble pared 1 |
3.2—3.6 |
Acrílico rígido, con pellets de poliestireno 2 |
0.57 |
Doble polietileno sobre vidrio |
2.8 |
Cortina individual de vidrio y térmica 3 |
4 |
Polietileno doble y cortina térmica 3 |
2.5 |
1 Dependiendo del espaciamiento entre las paredes.
2 paneles acrílicos rígidos de 32 mm rellenos de pellets de poliestireno.
3 Sólo cuando la cortina está cerrada y bien sellada.
Seleccione los coeficientes de transferencia de calor (valores U; Cuadro 5.1.1) y las tasas de infiltración (Cuadro 5.1.2) con precaución al realizar cálculos de pérdida de calor. Las tasas de infiltración dependen en gran medida de la magnitud y dirección del viento, entre otros factores.
Métodos de enfriamiento y enfriamiento
Durante los periodos más cálidos del año, la temperatura dentro del área de cultivo de una planta de producción podría ser mucho mayor que la temperatura exterior (como ocurre dentro de un automóvil cerrado en un día soleado). Las altas temperaturas dentro de los invernaderos pueden deprimir el crecimiento de las plantas y, en casos extremos, matar un cultivo. Los sistemas de refrigeración son esenciales para instalaciones de producción de plantas que se utilizan durante todo el año.
Tipo y Construcción | Tasa de infiltración (N) 1 | |
---|---|---|
Nueva construcción: | s −1 | h −1 |
Película plástica doble |
2.13 × 10 −4 —4.13 × 10 −4 |
0.75—1.5 |
Vidrio o fibra de vidrio |
1.43 × 10 −4 —2.83 × 10 −4 |
0.50—1.0 |
Construcción antigua: | ||
Vidrios, buen mantenimiento |
2.83 × 10 −4 —5.63 × 10 −4 |
1.0—2.0 |
Vidrio, mantenimiento deficiente |
5.63 × 10 −4 —11.13 × 10 −4 |
2.0—4.0 |
1 Intercambios de volumen de aire interno por unidad de tiempo (s −1 o h −1). Los vientos fuertes o la exposición directa al viento aumentarán las tasas de infiltración; a la inversa, los vientos bajos o la protección contra el viento reducirán las tasas de infiltración
Enfriamiento Mecánico (Aire Acondicionado)
Si bien el aire acondicionado de los invernaderos es técnicamente factible, los costos de instalación y operación pueden ser muy altos, particularmente durante los meses de verano. El momento más económico para usar aires acondicionados en invernaderos es durante la primavera y el otoño cuando la carga de calor es relativamente baja y el cultivo puede beneficiarse del enriquecimiento de CO 2. El aire acondicionado es una alternativa al uso de la ventilación para manejar la humedad y controlar la temperatura. Por definición, el aire acondicionado es un proceso termodinámico que elimina el calor y la humedad de un espacio interior (por ejemplo, el interior de una planta de producción de ambiente controlado) para mejorar sus condiciones. Implica un ciclo de refrigeración mecánica que obliga a un refrigerante a través de un proceso circular de expansión y contracción, resultando en evaporación y condensación, resultando en la extracción de calor (y humedad) del área de cultivo de la planta.
El enfriamiento mecánico puede ser necesario para las instalaciones de cultivo en interiores. Por lo general, las instalaciones de cultivo en interiores operan con tasas de cambio mínimas con el aire exterior, por lo que el aire acondicionado se convierte en una de las formas de eliminar la humedad generada por las plantas durante la transpiración. Es esencial aislar y construir el edificio adecuadamente para minimizar la ganancia de calor solar en instalaciones interiores que pueden aumentar la carga de calor. Adicionalmente, es crucial conocer la carga de calor de las lámparas eléctricas que proporcionan la energía necesaria para la fotosíntesis para dimensionar adecuadamente el aire acondicionado.
Enfriamiento Evaporativo
A veces, durante los cálidos meses de verano, la ventilación regular y el sombreado (por ejemplo, cal o cortinas móviles) no pueden mantener la temperatura del invernadero en el punto de ajuste deseado, por lo que se necesita enfriamiento adicional. Los productores suelen utilizar el enfriamiento evaporativo como un método de enfriamiento simple y relativamente económico. El proceso de evaporación requiere calor. Este calor (energía) proviene del aire circundante, lo que hace que la temperatura del aire baje. Simultáneamente, la humedad del aire aumenta a medida que el agua evaporada se convierte en parte de la masa de aire circundante. La cantidad máxima de enfriamiento posible con los sistemas de enfriamiento evaporativo depende de las propiedades iniciales del aire exterior, es decir, la humedad relativa (cuanto más seco sea el aire, más agua pueda absorber y menor será la temperatura final del aire) y la temperatura del aire (el aire más cálido puede transportar más vapor de agua en comparación con el aire más frío). Dos sistemas de enfriamiento evaporativo diferentes utilizados para administrar las temperaturas del aire interior del invernadero durante períodos en los que el uso del aire exterior para la ventilación no es suficiente para mantener las temperaturas establecidas son el sistema de almohadilla y ventilador y el sistema de niebla.
Sistema de Almohadilla y Ventilador
Los sistemas de almohadilla y ventilador incluyen una almohadilla de enfriamiento evaporativo instalada como un segmento de la pared del invernadero, generalmente en la pared opuesta a los ventiladores de escape. Las almohadillas correctamente instaladas permiten que todo el aire de ventilación entrante pase a través de él antes de ingresar al ambiente del invernadero (Figura 5.1.2). Las almohadillas están hechas de material corrugado (papel impregnado o plástico) pegados entre sí de manera que permite el máximo contacto con el aire que pasa a través del material de la almohadilla húmeda. El agua se introduce en la parte superior de la almohadilla y se libera a través de pequeños orificios a lo largo de toda la longitud de la tubería de suministro. Estos orificios están espaciados uniformemente a lo largo de toda la longitud de la almohadilla para proporcionar una humectación uniforme. El exceso de agua se recoge en el fondo de la almohadilla y se devuelve a un tanque de sumidero para su reutilización. El tanque de sumidero está equipado con una válvula de flotador para manejar el agua de reposición que compensa la porción del agua recirculante perdida por evaporación y diluir la concentración de sal que puede aumentar en el agua restante con el tiempo. Es una práctica común purgar continuamente aproximadamente el 10% del agua que regresa a un drenaje designado para evitar la acumulación excesiva de sal (cristales) en el material de la almohadilla que puede reducir la eficiencia de la almohadilla. Durante la operación de verano, es común “secar las almohadillas”, es decir, detener el flujo de agua mientras se mantienen los ventiladores funcionando por la noche para evitar la acumulación de algas que también pueden reducir la eficiencia de las almohadillas. El aire enfriado (y humidificado) sale de la almohadilla y se mueve a través del invernadero recogiendo calor del interior del invernadero. En general, los sistemas de almohadilla y ventilador utilizados en invernaderos experimentan un gradiente de temperatura entre la entrada (almohadilla) y la salida (ventilador de escape). En sistemas diseñados adecuadamente, este gradiente de temperatura se mantiene bajo (hasta 4°—6°C es posible) para proporcionar un ambiente uniforme para todas las plantas.
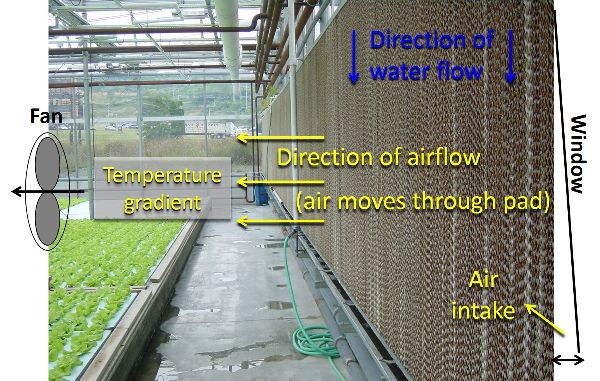
El área de la almohadilla evaporativa requerida depende del grosor de la almohadilla y se puede calcular mediante:
\[ A_{pad} = \frac{\text{total greenhouse ventilation fan capacity}}{\text{recommended air velocity through pad}} \]
Por ejemplo, para almohadillas de 10 cm de grosor, la capacidad del ventilador (en m 3 s −1) debe dividirse por la velocidad recomendada del aire a través de la almohadilla, 1.3 m s −1 (ASAE Standards, 2003). Para almohadillas de 15 cm de grosor, la capacidad del ventilador debe dividirse por la velocidad de aire recomendada a través de la almohadilla, 1.8 m s −1. La capacidad mínima recomendada de bombeo es de 26 y 42 L s −1 por metro lineal de la almohadilla, y la capacidad mínima del tanque de sumidero es de 33 y 41 L por m 2 de área de almohadilla para las almohadillas de 10 y 15 cm, respectivamente. Para las almohadillas de enfriamiento evaporativo, el uso máximo estimado de agua puede ser tan alto como 17—20 L h −1 por m 2 de área de almohadilla.
Sistema de niebla de alta presión
El otro sistema de enfriamiento evaporativo comúnmente utilizado es el sistema de niebla. Este sistema se utiliza típicamente en invernaderos con sistemas de ventilación natural debido a que la ventilación natural no tiene la fuerza para superar la resistencia adicional al flujo de aire resultante de una almohadilla de enfriamiento evaporativo. Las boquillas de un sistema de niebla se instalan típicamente en todo el invernadero para proporcionar un patrón de enfriamiento más uniforme en comparación con el sistema de almohadilla y ventilador. El espaciado recomendado es de aproximadamente una boquilla por cada 5—10 m 2 de área de cultivo. La presión del agua utilizada en los sistemas de niebla de invernadero es relativamente alta (≥3,450 kPa) y suficiente para producir gotitas muy finas que se evaporan antes de llegar a las superficies de la planta. El uso de agua por boquilla es pequeño, aproximadamente 3.8—4.5 L h −1. El agua para los sistemas de nebulización debe estar libre de impurezas para evitar la obstrucción de las aberturas de las boquillas. Por lo tanto, los sistemas de niebla requieren tratamiento de agua (filtración y purificación) y una bomba de alta presión. Por lo tanto, los sistemas de niebla pueden ser más caros de instalar en comparación con los sistemas de almohadilla y ventilador, pero el enfriamiento resultante es más uniforme.
Ventilación
Para mantener las condiciones óptimas de crecimiento, el aire interior cálido y húmedo necesita ser reemplazado por aire exterior más fresco y seco. Las instalaciones de producción de plantas utilizan ventilación mecánica o natural para lograr esto. La ventilación mecánica requiere aberturas de entrada, extractores y energía eléctrica para operar los ventiladores. Cuando se diseña adecuadamente, la ventilación mecánica puede proporcionar enfriamiento y deshumidificación adecuados bajo una amplia gama de condiciones climáticas en muchos lugares con climas templados. La especificación de diseño típica para la capacidad máxima de ventilación mecánica es 0.05 o 0.06 m 3 s −1 por m 2 de área de piso para invernaderos con o sin cortina de sombra, respectivamente. Cuando hay obstrucciones deliberadas en la entrada de aire (como pantallas de exclusión de insectos y una almohadilla de enfriamiento evaporativo), el área de entrada debe dimensionarse cuidadosamente para superar la mayor resistencia al flujo de aire que resultaría en una reducción en la tasa de intercambio de aire total en relación con la apertura total y entradas sin obstrucciones. En ese caso, los ventiladores de ventilación deberían poder superar la resistencia adicional al flujo de aire creada por la pantalla o la almohadilla de enfriamiento evaporativo. Los ventiladores múltiples y escalonados pueden proporcionar diferentes tasas de ventilación según las condiciones ambientales. Los motores de ventilador de velocidad variable permiten un control más preciso de la velocidad de ventilación y pueden reducir el consumo general de electricidad.
La ventilación natural funciona sobre dos fenómenos físicos: la flotabilidad térmica (el aire cálido es menos denso y se eleva), y el efecto viento (el viento que sopla fuera de una estructura crea pequeñas diferencias de presión entre los lados de barlovento y sotavento de la estructura, lo que hace que el aire se mueva hacia el lado de sotavento). Todo lo que se necesita son aberturas de entrada y salida cuidadosamente colocadas, motores de ventanas de ventilación y electricidad para operar los motores. En algunos invernaderos con ventilación natural, las posiciones de las ventanas de ventilación se manejan manualmente (por ejemplo, en un sistema de producción de túneles de plástico de baja tecnología), eliminando la necesidad de motores y electricidad, pero esto aumenta la cantidad de mano de obra, especialmente cuando son necesarios ajustes frecuentes. Los sistemas de ventilación natural operados eléctricamente utilizan mucha menos energía que los sistemas de ventilación mecánica (ventilador). Cuando se utiliza un sistema de ventilación natural, un sistema de niebla puede proporcionar enfriamiento adicional, por ejemplo, siempre que la humedad del aire no sea demasiado alta. Desafortunadamente, la ventilación natural no funciona muy bien en días cálidos cuando la velocidad del viento es baja (menos de 1 m s −1) o cuando la instalación utiliza un sistema de sombra que obstruye el flujo de aire. Cuando se usa solo ventilación natural o forzada, la temperatura interior no se puede bajar por debajo de la temperatura exterior sin capacidades de enfriamiento adicionales (generalmente enfriamiento evaporativo).
Para la mayoría de los invernaderos independientes, los sistemas de ventilación mecánica generalmente mueven el aire a lo largo del invernadero (es decir, los ventiladores de escape y las aberturas de entrada se instalan en paredes extremas opuestas). Para evitar una velocidad excesiva dentro del invernadero, las distancias de entrada al ventilador generalmente se limitan a 70 a 80 m, siempre que los climas locales no sean demasiado calurosos. Los sistemas de ventilación natural para invernaderos independientes suelen proporcionar ventilación cruzada mediante ventanas laterales y rejillas de ventilación en el techo.
En los invernaderos conectados a canalones (Figura 5.1.3), las entradas y salidas del sistema de ventilación mecánica se pueden instalar en las paredes laterales o finales, mientras que los sistemas de ventilación natural suelen consistir únicamente en respiraderos de techo. Los respiraderos laterales tienen una influencia limitada en la ventilación de las secciones interiores en invernaderos más grandes. El sistema de ventilación natural definitivo es el diseño de invernadero de techo abierto que permite que la temperatura interior rara vez supere la temperatura exterior. Este tipo de efecto no es alcanzable con invernaderos ventilados mecánicamente debido a las cantidades sustanciales de aire que dichos sistemas tendrían que mover a través del invernadero para lograr los mismos resultados.
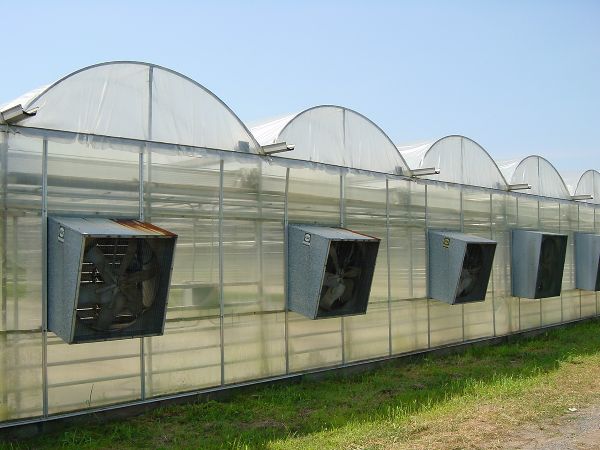
Cualquiera que sea el sistema de ventilación utilizado, la distribución uniforme del aire dentro del invernadero es esencial porque la uniformidad en la producción de cultivos solo es posible cuando todas las plantas experimentan las mismas condiciones ambientales. Por lo tanto, el uso de ventiladores de flujo de aire horizontales es común para asegurar una mezcla de aire adecuada. La capacidad recomendada del ventilador de flujo de aire horizontal es de aproximadamente 0.015 m 3 s −1 por m 2 del área de cultivo.
Iluminación y Sombreado
Dado que la luz es la fuerza impulsora de la fotosíntesis y el crecimiento de las plantas, la gestión del entorno de luz de una instalación de cultivo es de primordial importancia. Para muchos cultivos, el crecimiento de las plantas es proporcional a la cantidad de luz que recibe el cultivo durante todo el período de crecimiento. Tanto la intensidad de luz instantánea como la integral de luz diaria son parámetros importantes para los cultivadores. Los científicos de plantas definen la luz en la banda de onda de 400—700 nm como radiación fotosintéticamente activa (PAR). PAR representa la intensidad de luz (instantánea) y tiene las unidades μmol m −2 s −1 (ASABE Standards, 2017). Al referirse a la cantidad de luz que recibe un cultivo a lo largo de algún tiempo, como una hora o un día, se calcula la suma de las intensidades PAR instantáneas, y los valores resultantes a menudo se denominan integrales de luz. Por lo general, los cultivadores miden integrales de luz durante un día entero (desde el amanecer hasta el amanecer), dando como resultado la integral de luz diaria (DLI), con la unidad mol m −2 d −1. Se pueden usar medidas instantáneas de PAR para activar acciones de control como encender o apagar la iluminación suplementaria. Algunos cultivadores despliegan cortinas de sombra móviles para manejar la intensidad de la luz. Las integrales de luz diaria (DLI) pueden ser utilizadas por los cultivadores para garantizar un nivel constante de crecimiento de los cultivos manteniendo una integral constante de día a día (ya sea de luz natural, iluminación suplementaria o una mezcla), o para rastrear la entrada de radiación acumulada que sirve como fuente de energía para la fotosíntesis. El DLI total recibido por un dosel de una planta es la suma de la cantidad de luz solar recibida más cualquier contribución del sistema de iluminación suplementaria (para la producción de invernadero). La ecuación 5.1.4 determina la intensidad PAR instantánea (μmol m −2 s −1) necesaria para cumplir un objetivo de DLI (mol m −2 d −1) durante un número específico de horas:
\[ \text{intensity}(\frac{\mu mol}{m^{2}s}) = \frac{DLI}{\text{h per day}} \times \frac{1\ h}{3,600\ s} \times \frac{1\times10^{6} \mu mol}{1\ mol} \]
Por ejemplo, usando la Ecuación 5.1.4, se necesita una intensidad de 197 μmol m −2 s −1 para entregar un DLI objetivo de 17 mol m −2 d −1 durante 24 h (un día).
Sensibilidad de las plantas a la
Los ojos humanos tienen una sensibilidad diferente a la luz (o radiación) (natural) en comparación con la forma en que las plantas responden a la luz (Figura 5.1.4). Los ojos humanos son más sensibles a las longitudes de onda verdes (pico a 555 nm), mientras que la mayoría de las plantas presentan sensibilidades máximas en la parte azul (pico a 430 nm) y naranja-roja (pico a 610 nm) del espectro de luz visible. Esta diferencia de sensibilidad significa que el ojo humano no es un “sensor” muy útil en términos de evaluar si un ambiente de luz particular es adecuado para el crecimiento y desarrollo de las plantas. Mientras que PAR es luz a través de la banda de onda de 400—700 nm, como se muestra en la Figura 5.1.4, las plantas también son sensibles a la radiación UV (280—400 nm) y rojo lejano (700—800 nm). Por lo tanto, lo mejor es utilizar sensores especialmente diseñados (sensores PAR y espectrorradiómetros) para evaluar las características de la luz en entornos utilizados para la producción de plantas.
Iluminación Natural y Eléctrica
La luz natural del sol es un aspecto esencial de la producción de invernadero, tanto en términos de crecimiento y desarrollo de las plantas, sino también en términos de balance energético (calentamiento y enfriamiento de invernadero). En las instalaciones de cultivo interiores, la luz es proporcionada únicamente por la iluminación eléctrica, aunque la cantidad de luz natural que incide en la superficie externa del edificio que contiene una instalación de cultivo interior también puede afectar sustancialmente el balance energético de la instalación.
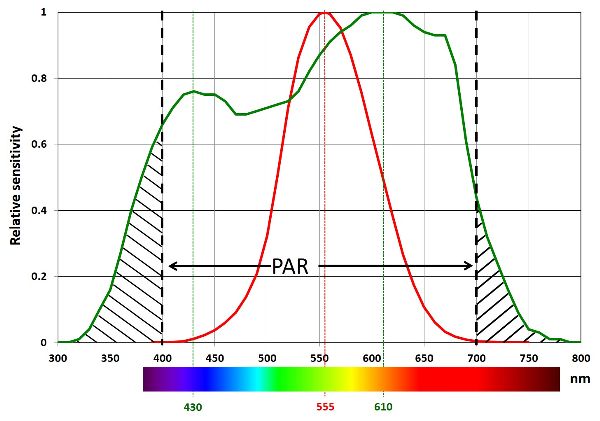
Luz solar directa y difusa
La atmósfera terrestre contiene muchas partículas (moléculas de gas, vapor de agua y materia particulada) que pueden cambiar la dirección de la luz del sol. En un día despejado, hay menos partículas en la atmósfera, y la luz solar viaja sin obstáculos antes de llegar al suelo. Este tipo de luz solar se llama luz directa o radiación directa. En días nublados, la atmósfera contiene más partículas (principalmente vapor de agua), y la interacción de la luz solar con todas esas partículas provoca cambios direccionales que en su mayoría son aleatorios. Como resultado, en días nublados, la luz del sol viene de muchas direcciones. Este tipo de luz solar se llama luz difusa o radiación difusa. Estas frecuentes interacciones luz-partícula también darán como resultado una reducción en la intensidad de la luz en comparación con la radiación directa.
Dependiendo de la composición de la atmósfera (nubosidad), la luz solar llegará a la superficie como radiación directa, radiación difusa o una combinación de ambas. La radiación directa no alcanza las capas inferiores del dosel sombreadas por los tejidos vegetales (principalmente hojas); sin embargo, debido a que la radiación difusa es omnidireccional, puede penetrar más profundamente en el dosel de una planta (particularmente en un dosel de varias capas y más alto). Por lo tanto, aunque la cantidad de radiación difusa puede parecer pequeña, puede impulsar la producción de la planta porque alcanza más superficies vegetales involucradas en la fotosíntesis. Algunos materiales de acristalamiento de invernadero (por ejemplo, película de polietileno) difunden la radiación solar entrante más que otros (Tabla 5.1.3), y aunque la intensidad de luz general suele ser menor en invernaderos cubiertos con un material de acristalamiento difuso, el crecimiento y desarrollo de los cultivos no se reducen necesariamente proporcionalmente porque más de las superficies del dosel están recibiendo luz adecuada para la fotosíntesis.
Las cantidades de radiación difusa se miden con un sensor de luz colocado detrás de un disco que proyecta una sombra precisa sobre el sensor, por lo que bloquea toda la radiación directa. La cantidad de radiación directa se determina mediante el uso de un segundo sensor que mide la radiación total (directa más difusa) (radiación directa = radiación total — radiación difusa).
Material de Acristalamiento | Transmitancia PAR directa (%) |
Transmitancia infrarroja (calor) [a] (%) |
Transmitancia ultravioleta [b] (%) |
Esperanza de vida (años) |
---|---|---|---|---|
Vidrio |
90 |
0 |
60—70 |
30 |
Acrílico [c] |
89 |
0 |
44 |
10—15 |
Policarbonato3 |
80 |
0 |
18 |
10—15 |
Polietileno [d] |
90 |
45 |
80 |
3—4 |
PE, IR y CA [d] [e] |
90 |
30 |
80 |
3—4 |
[a] para longitudes de onda superiores a 3.000 nm
[b] para longitudes de onda entre 300 y 400 nm
[C] pared doble
[d] una sola capa
[e] película de polietileno con barrera infrarroja y tratamiento superficial anticondensado
A medida que la luz solar llega a las superficies externas de la estructura del invernadero, la luz puede reflejarse, absorberse o transmitirse. A menudo estos procesos coinciden. Las cantidades de luz reflejada, absorbida o transmitida dependen de los materiales (acristalados) involucrados, la hora del día, la época del año y si el productor utiliza alguna estrategia de control (por ejemplo, cal o cortinas de sombra). Además, los equipos aéreos pueden bloquear la luz y reducir la cantidad total de luz solar que llega al dosel de la planta. No es raro, incluso en invernaderos modernos, que las plantas reciban alrededor del 50-60% en promedio de la cantidad de luz solar disponible fuera de la estructura del invernadero. Dado que cada porcentaje de luz adicional que recibe el dosel de la planta cuenta, es esencial diseñar invernaderos cuidadosamente teniendo en cuenta la transmisión óptima de la luz.
Efecto de la orientación del invernadero
Otra consideración, particularmente en latitudes más altas, es la orientación del invernadero. En latitudes superiores a 40 grados, orientar las canaletas de un invernadero a lo largo de una dirección este-oeste puede ayudar a capturar la mayor cantidad de luz durante los meses de invierno cuando el sol está bajo en el cielo y la cantidad total de luz solar también es baja. Sin embargo, usando tal orientación, las bandas de sombra creadas por componentes estructurales y equipos aéreos tienden a moverse más lentamente. Esto puede ser un problema particularmente desafiante cuando el cultivo se cultiva en invernadero por solo un corto período de tiempo (por ejemplo, para verduras de hoja verde). En ese caso, es preferible orientar el invernadero norte-sur. Aparte de cualquier sombra, la intensidad de la luz solar se considera uniforme en toda la zona de cultivo.
Sombreado
Durante los días soleados, existe el riesgo de que los cultivos de invernadero estén expuestos a demasiada luz, lo que requiere el uso de cortinas de sombra para ayudar a reducir el estrés de las plantas debido a las altas intensidades de luz. En días variablemente nublados, las condiciones de luz dentro de un invernadero pueden fluctuar rápidamente de condiciones de poca luz a condiciones de luz alta. Tales oscilaciones en condiciones de luz pueden afectar negativamente el crecimiento y desarrollo de las plantas, por lo que los cultivadores pueden tener que desplegar tanto el sistema de iluminación suplementario como las cortinas de sombra para proporcionar condiciones de crecimiento más estables. Administrar el sistema de iluminación suplementario a menudo implica controlar las cortinas de sombra.
El sombreado adecuado es esencial para algunos cultivos. Por ejemplo, la lechuga cultivada en un invernadero está sujeta a tipburn (Figura 5.1.5) si las condiciones de luz, temperatura y humedad no se mantienen dentro de rangos específicos.
Una estrategia es aplicar un tratamiento de cal al invernadero durante los meses pico de radiación solar y lavarlo al final de la temporada de crecimiento natural cuando las condiciones de luz disminuyen. Los inconvenientes incluyen mayores costos de mano de obra y requisitos adicionales para iluminación suplementaria. Las cortinas móviles son otra estrategia efectiva para administrar tipburn, si se diseñan y usan adecuadamente. Desplegar cortinas de sombra demasiado tarde durante el día puede causar quemaduras en la lechuga (demasiada luz aumenta la tasa de crecimiento más allá del punto en el que el transporte de calcio puede mantenerse al día), y desplegarlas demasiado pronto puede resultar en horas adicionales de iluminación suplementaria. Las cortinas de sombra móviles, dependiendo del diseño, también pueden reducir la pérdida de calor durante la noche, pero este doble uso suele ser un compromiso entre las capacidades óptimas de sombreado y la máxima retención de energía. Una solución más completa son dos cortinas diferentes, cada una optimizada para su propósito, pero un sistema de doble cortina de este tipo duplica el costo de instalación.
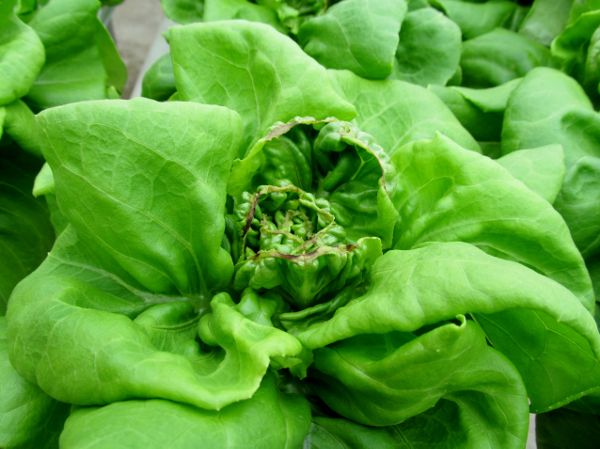
Tipos Comunes de Iluminación Artificial
Los dos tipos más comunes de iluminación de invernadero son las lámparas de descarga de gas y diodos emisores de luz (LED) (Figura 5.1.6). Las lámparas de descarga de gas, como las lámparas fluorescentes (FL), de haluro metálico (MH) y de sodio de alta presión (HPS), producen luz al pasar una corriente a través de un gas ionizado. El espectro de luz producida es una función del gas utilizado y de la composición de los electrodos. Las lámparas MH proporcionan una luz de color más blanco, mientras que la luz HPS es más naranja amarillenta (similar a la luz de farola tradicional).
Las lámparas LED utilizan semiconductores que liberan energía en forma de fotones cuando pasa suficiente corriente a través de ellos. La longitud de onda de la luz emitida está determinada por la banda prohibida del semiconductor y cualquier fósforo utilizado para convertir la luz LED monocromática. A diferencia de las lámparas de descarga de gas, los LED sin fósforo producen luz dentro de una banda de onda relativamente estrecha. Para obtener una salida de amplio espectro, como la luz blanca, los fabricantes suelen utilizar LED azules de alta eficiencia y convierten la salida a luz blanca usando fósforos amarillos. Algunas plantas se benefician de pequeñas cantidades de radiación UV (280—400 nm), pero las personas que trabajan en estos entornos deben usar protección especial para los ojos y la piel para minimizar los efectos nocivos que presenta la radiación UV.
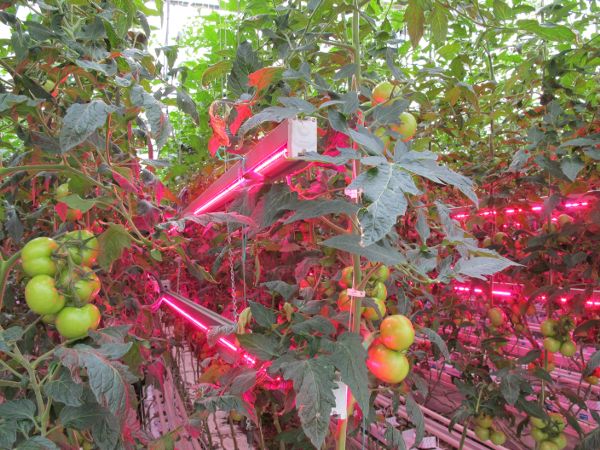
Eficacia de iluminación
Al momento de escribir este artículo (principios de 2020), las lámparas de mayor eficiencia energética disponibles para iluminación suplementaria son los accesorios basados en LED (Mitchell et al., 2012; Wallace y Both, 2016). Sin embargo, no todos los accesorios LED están diseñados para aplicaciones de crecimiento de plantas. Al comparar la eficiencia de las luces, se debe considerar el uso de energía del enchufe de pared del accesorio. Algunos accesorios LED dependen de la refrigeración activa utilizando ventiladores de ventilación (en algunos casos, refrigeración por agua) para evitar el sobrecalentamiento que puede acortar su vida útil. La instalación de refrigeración activa requiere energía adicional, la cual debe considerarse, además de otras pérdidas, como las de transformadores y conductores. Idealmente, los fabricantes publican una medición de eficacia, es decir, salida de luz dividida por entrada de energía, o μmol s −1 de salida PAR (luz) por entrada de W (electricidad) (μmol J −1) para sus accesorios (Both et al., 2017). Las eficacias para lámparas utilizadas en aplicaciones de crecimiento de plantas se muestran en la Tabla 5.1.4. Las eficacias de los dispositivos continúan aumentando con varios accesorios LED que ahora se acercan a 3 μmol J −1. Los accesorios de mayor eficacia utilizan menos energía eléctrica para producir la misma cantidad de luz.
Una nota sobre las unidades de iluminación
En la industria hortícola, todavía es común usar unidades de luz de lux, lúmenes o velas de pie. Sin embargo, esto no es particularmente útil ya que los lux, lúmenes y velas de pie se basan en la sensibilidad del ojo humano, que es más sensible a la parte verde del espectro de luz visible (Figura 5.1.4). Idealmente, la salida de luz total de los dispositivos de iluminación suplementarios debe reportarse en unidades PAR integradas (μmol s −1). Tenga en cuenta que esta unidad no es la misma que la unidad utilizada para la intensidad instantánea de PAR (μmol m −2 s −1). Los usuarios deben ser conscientes de esto al comprar accesorios de iluminación y asegurarse de que se utilizaron los instrumentos adecuados para evaluar la salida de luz.
Tipo de lámpara | Consumo de energía (W) | Eficacia (μmol J −1) |
---|---|---|
Incandescente (bombilla Edison) |
102.4 |
0.32 |
Fluorescente compacto (bombilla grande) |
61.4 |
0.89 |
CMH (base de magnate) |
339 |
1.58 |
HPS (base de magnate) |
700 |
1.56 |
HPS (doble extremo) |
1077 |
1.59 |
LED (barra, refrigerado pasivamente) |
214 |
2.39 |
Ventajas y desventajas de los sistemas de iluminación
Sistema de iluminación HPS
Las lámparas HPS han sido durante mucho tiempo el tipo de lámpara preferido para aplicaciones de iluminación suplementaria (Both et al., 1997).
Ventajas
- • Tanto las lámparas como los accesorios (incluidos los balastos y reflectores) son relativamente económicos y fáciles de mantener (por ejemplo, reemplazo de bombillas y limpieza de reflectores).
- • Antes de que los LED estuvieran disponibles, las lámparas HPS tenían la mayor eficiencia de conversión (eficacia), y producían un espectro suficientemente amplio que era aceptable para una amplia gama de especies de plantas. La reciente introducción de lámparas HPS de doble punta incrementó un poco su eficacia.
Desventajas
- • Un inconveniente importante de las lámparas HPS es la producción de una cantidad sustancial de energía radiante, lo que requiere una distancia adecuada entre las luces y las superficies de la planta expuestas a esta radiación.
- • Requieren un ciclo de calentamiento antes de alcanzar la máxima salida, y una vez apagados, necesitan un período de enfriamiento antes de volver a usarlos.
- • Al igual que con todas las lámparas, la salida de luz de las lámparas HPS se deprecia con el tiempo, requiriendo reemplazos de bombilla cada 10,000 a 15,000 hrs.
Dado que las lámparas HPS han estado en uso durante varias décadas, los investigadores y cultivadores han aprendido la mejor manera de producir sus cultivos con esta fuente de luz. Por ejemplo, si bien la producción de calor radiante puede considerarse un inconveniente, también se puede utilizar como una herramienta de gestión para ayudar a mantener una temperatura deseable del dosel, y este calor radiante puede ayudar a reducir la cantidad de energía térmica (proporcionada por el sistema de calefacción) necesaria para mantener la temperatura del punto de ajuste.
Sistemas de iluminación LED
Las lámparas LED (a menudo consisten en matrices de múltiples LEDs individuales) son una tecnología relativamente nueva para aplicaciones hortícolas, y sus capacidades de rendimiento aún están evolucionando (Mitchell et al., 2015).
Ventajas
- • La eficacia de las lámparas LED cuidadosamente diseñadas ha superado la eficacia de las lámparas HPS, y el calor que producen se puede eliminar más fácilmente por convección natural o forzada.
- • El calor convectivo resultante (aire caliente que emana de la lámpara/accesorio) es más fácil de manejar en instalaciones de ambiente controlado que el calor radiante producido por las lámparas HPS porque el manejo del aire es un proceso común mientras que el bloqueo del calor radiante no lo es.
- • Las lámparas LED se pueden encender y apagar rápidamente y requieren un período de calentamiento mucho más corto que las lámparas HPS.
- • Es posible modular la intensidad de luz producida por las lámparas LED, ya sea ajustando la tensión de alimentación o mediante un proceso llamado modulación por ancho de pulso (PWM; ciclo rápido de encendido/apagado durante intervalos de tiempo ajustables). Al combinar (y controlar) LEDs con diferentes salidas de color en un solo accesorio, los productores tienen mucho más control sobre el espectro que producen estas lámparas, abriendo nuevas estrategias para el cultivo de sus cultivos. Este beneficio en particular requerirá (mucha) investigación adicional para ser completamente entendida o realizada.
- • Las lámparas LED suelen tener una vida útil más larga (hasta 50,000 h), pero se necesitan más pruebas en las instalaciones de producción de plantas para validar esta estimación.
Desventajas
- • Las lámparas LED (accesorios) son más caras en comparación con los accesorios HPS con características de salida similares.
- • Las lámparas LED generalmente vienen como una unidad empaquetada (incluidos los LED, la carcasa y el controlador electrónico), lo que hace que el reemplazo de componentes fallidos sea casi imposible.
- • Debido a que las plantas son más sensibles a la luz azul y roja en términos de fotosíntesis, los cultivadores suelen utilizar accesorios LED que producen una combinación de luz roja + azul = magenta. La luz magenta (Figura 5.1.6) hace que sea mucho más difícil observar el color real del tejido vegetal (que es esencial para la observación de posibles anomalías resultantes de problemas de plagas y/o enfermedades), y puede hacer que trabajar en un ambiente con ese espectro sea más desafiante (ha sido informó para incomodar a algunas personas).
- • Algunas lámparas LED tienen tasas de parpadeo (imperceptibles) que pueden tener efectos sobre la salud en humanos con sensibilidades específicas (por ejemplo, personas con epilepsia).
Aplicaciones
Sistemas de Calefacción en Invernaderos
Los invernaderos se pueden calentar utilizando una variedad de métodos y equipos para manejar las pérdidas de calor durante la estación fría. Por lo general, el combustible se quema para calentar el aire o el agua (vapor en invernaderos más antiguos) que circula a través del ambiente del invernadero. Algunos invernaderos utilizan sistemas de calefacción por infrarrojos que irradian energía térmica a las superficies expuestas del dosel de la planta. El uso de calefacción eléctrica (resistencia) es mínimo debido al alto costo de operación. Sin embargo, a medida que aumentan los costos de los combustibles fósiles, la calefacción eléctrica podría llegar a ser competitiva incluso para amplias operaciones de invernadero en varios lugares.
Calentadores y Hornos de Unidad
Los sistemas típicos de calentamiento de aire incluyen calentadores unitarios y hornos (Figura 5.1.7). Normalmente, el calor generado por el proceso de combustión se transfiere al aire del invernadero a través de un intercambiador de calor, o el aire del invernadero utilizado como fuente de oxígeno para el proceso de combustión y luego se libera al invernadero. El uso de intercambiadores de calor permite que el aire de combustión permanezca separado del ambiente del invernadero (combustión separada), minimizando así el riesgo de liberar pequeñas cantidades de gases potencialmente dañinos (por ejemplo, etileno, monóxido de carbono) en el ambiente del invernadero. Además, aumenta directamente la temperatura del aire sin introducir humedad adicional.
El uso del aire de invernadero como fuente de oxígeno para la combustión requiere un equipo de combustión adecuadamente mantenido y una combustión completa del combustible para garantizar que solo el vapor de agua y el dióxido de carbono (CO 2) sean liberados al ambiente del invernadero. Un enfoque intermedio es usar aire de invernadero para la combustión y ventilar los gases de combustión al aire libre.
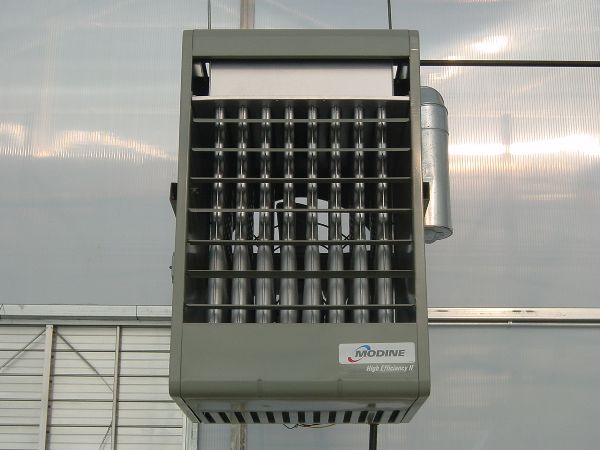
Los ventiladores generalmente se incorporan en los sistemas de calefacción de aire para mover y distribuir el aire caliente para asegurar un calentamiento uniforme del ambiente en crecimiento. Algunos invernaderos utilizan conductos inflables de polietileno (el sistema de tubos de polietileno) colocados arriba o debajo de los bancos o filas de cultivos para distribuir el aire. Algunos utilizan ventiladores de flujo de aire horizontales o verticales estratégicamente colocados. Los sistemas de calefacción de aire son relativamente fáciles de instalar a un costo modesto, pero tienen una distribución de calor inadecuada en comparación con los sistemas de calentamiento de agua caliente.
Sistemas de calentamiento de agua caliente
Los sistemas de calefacción a base de agua consisten en una caldera y un sistema de circulación de agua (bombas, válvulas mezcladoras y plomería) (Figura 5.1.8). La caldera genera el calor para elevar la temperatura del agua circulante. El agua caliente se bombea para calentar el invernadero a través de una red de tuberías o sistema de distribución de tubos. Por lo general, las tuberías de calefacción se instalan en los postes de soporte, alrededor del perímetro y en la parte superior (a veces cerca de canaletas para mejorar el deshielo usando el calor liberado, y espaciadas uniformemente entre canaletas más espaciadas para proporcionar una entrega de calor uniforme). Algunos invernaderos tienen calefacción de piso o de banco con tubos de calefacción adicionales instalados en el piso o en/cerca de los bancos para calentar la zona raíz. Estos sistemas de calefacción de zona radicular tienen la ventaja de proporcionar un control independiente de las temperaturas de la zona radicular y entregar calor uniforme muy cerca del dosel de la planta. Sin embargo, los sistemas de calefacción de la zona raíz normalmente no son capaces de proporcionar suficiente capacidad de calentamiento durante las épocas más frías del año, lo que requiere el uso de calefacción adicional en forma de tuberías de calefacción perimetrales y aéreas. Un beneficio significativo de los sistemas de calefacción a base de agua es la capacidad de “almacenar” calor en grandes tanques de agua aislados. Las calderas se pueden utilizar durante el día para producir CO 2 para el consumo de la planta, con cualquier exceso de calor almacenado para su uso durante periodos más fríos como la noche, cuando no se requiere suplementación con CO 2.
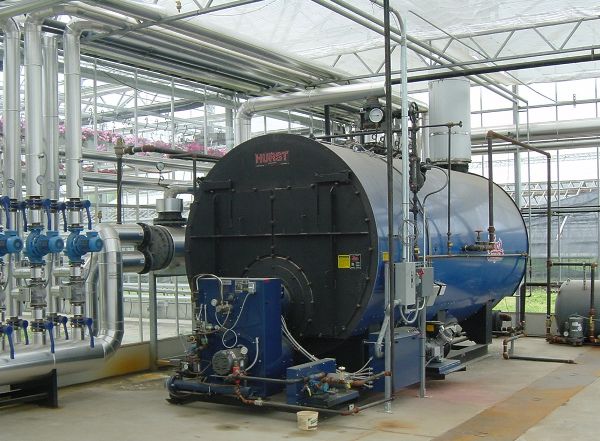
Sistemas de calefacción por infrarrojos
Los sistemas de calefacción por infrarrojos tienen la ventaja de la entrega inmediata de calor una vez encendidos, pero solo las superficies expuestas (en términos de línea de visión) del dosel de las plantas recibirán el calor radiante. El calentamiento por infrarrojos a veces proporciona un calentamiento no uniforme, especialmente en cultivos con un dosel de varias capas. Además, los sistemas de calentamiento por infrarrojos se diseñan típicamente como fuentes de línea y requieren cierta distancia entre la fuente y las superficies radiadas del dosel para lograr una distribución uniforme. Por último, al igual que los sistemas de aire caliente, los sistemas de calefacción por infrarrojos acumulan poco almacenamiento de calor durante la operación, de manera que en caso de un apagado de emergencia, hay poco calor residual disponible para extender el tiempo de calentamiento antes de que la temperatura baje por debajo de los
Fuentes Alternativas de Energía y Conservación de Energía
La volatilidad en los precios de los combustibles fósiles experimentada durante las últimas décadas ha puesto un mayor énfasis en la conservación de energía y en las fuentes alternativas de energía. Las medidas de conservación de energía empleadas incluyen medidas relativamente simples como el sellado de grietas y aberturas no deseadas en el acristalamiento del invernadero, un mejor aislamiento de los componentes estructurales y los sistemas de transporte de calor, y el mantenimiento oportuno de los equipos, así como medidas más avanzadas como los móviles cortinas de aislamiento/sombra, nuevos equipos de calefacción con mayores eficiencias (por ejemplo, calderas de condensación, bombas de calor, sistemas combinados de calor y energía) y nuevas estrategias de control (por ejemplo, integración de la temperatura, donde los productores están más preocupados por la temperatura promedio que recibe un cultivo, dentro de límites establecidos, en lugar de mantener firmemente una temperatura específica de punto de ajuste). Algunos productores retrasan la producción de cultivos a períodos en los que el clima es más cálido, mientras que otros utilizan temperaturas de punto de ajuste más bajas (a menudo requieren períodos de producción más prolongados y con impactos potenciales en la fisiología de las plantas
Las fuentes de calefacción de energía alternativa (es decir, combustibles no fósiles) utilizadas para aplicaciones de invernadero incluyen energía solar eléctrica, solar térmica, eólica, hidroeléctrica, biomasa y geotérmica (cogeneración y fuente de tierra, poco profunda o profunda). Muchas instalaciones de energía alternativa son viables solo bajo condiciones climáticas específicas y pueden requerir inversiones significativas que pueden requerir incentivos financieros (locales o nacionales). Desarrollar estrategias de conservación de energía y energía alternativa para las operaciones de invernadero sigue siendo un desafío debido a las considerables diferencias en tamaño, alcance y circunstancias locales. La selección de un sistema energético alternativo incluye considerar la viabilidad económica para la operación del invernadero así como la protección del medio ambiente.
Sistemas de Enfriamiento Evaporativo
Los productores o administradores de invernaderos suelen utilizar el enfriamiento evaporativo como la forma más asequible de reducir la temperatura del aire más allá de lo que el sistema de ventilación puede lograr solo por el movimiento del aire. La cantidad máxima de enfriamiento proporcionada por los sistemas de enfriamiento evaporativo depende de la temperatura inicial y la humedad del aire ambiente (es decir, exterior). Estos parámetros se pueden medir con relativa facilidad con un termómetro estándar y un sensor de humedad relativa. Con estas mediciones, se puede utilizar la tabla psicrométrica para determinar las propiedades correspondientes del aire, como la temperatura del bulbo húmedo, la relación de humedad, entalpía, etc. Con la conocida temperatura de bulbo húmedo, se puede calcular la depresión de bulbo húmedo para determinar la caída teórica de temperatura posible por enfriamiento evaporativo. Dado que pocos sistemas diseñados son 100% eficientes, es probable que la caída de temperatura real lograda por el sistema de enfriamiento por evaporación sea del 80 al 90% de la depresión teórica del bulbo húmedo.
Diseño de sistemas de iluminación
Los conceptos descritos anteriormente pueden ser utilizados para controlar la intensidad instantánea y las intensidades de luz integradas necesarias para evaluar las condiciones de luz en las instalaciones de crecimiento de las plantas. La información se puede utilizar para determinar los parámetros necesarios para seleccionar accesorios para modificar el ambiente de luz en instalaciones de crecimiento de plantas, por ejemplo, encender o apagar el sistema de iluminación suplementario, abrir o cerrar una cortina de sombra (en invernaderos) y, cuando se utilizan LED multiespectrales, puede incluir el cambio el espectro de luz y/o su intensidad general.
Requerimientos de luz
Al diseñar un sistema de iluminación para un invernadero o una instalación de cultivo interior, el primer paso es determinar los requisitos de luz de un cultivo en particular. Los artículos de investigación o manuales de cultivo para el cultivo de interés pueden proporcionar información sobre la intensidad de luz recomendada y/o la integral óptima de luz diaria (ver, por ejemplo, Lopez y Runkle, 2017). Para cultivos como las hojas verdes cultivadas en un invernadero, la integral objetivo diaria mínima puede ser tan baja como 8 a 14 mol m −2 d −1, o tan alta como 17 mol m −2 d −1 (la integral diaria máxima para lechuga de hoja antes de que se produzca daño fisiológico como resultado de demasiadas luz). Para los cultivos de vid, como los tomates, se tolera típicamente un mínimo de 15 mol m −2 d −1, mientras que el objetivo óptimo puede superar los 30 mol m −2 d −1. Generalmente, como regla general, para los cultivos de hortalizas, un incremento de 1% en el DLI da como resultado un incremento de 1% en el crecimiento (hasta cierto punto; Marcelis et al., 2006). Considerando el alto costo de proporcionar el ambiente de cultivo óptimo, generalmente tiene sentido económico optimizar el crecimiento de las plantas siempre que sea posible (Kubota et al., 2016).
Una vez determinado el DLI para el cultivo, el siguiente paso es determinar cuánta iluminación suplementaria se requiere para compensar cualquier déficit de luz natural. En una instalación de cultivo interior, toda la luz debe ser suministrada por lámparas eléctricas, mientras que en un invernadero, la iluminación natural suele proporcionar la mayor parte del DLI durante todo el año. Incluso en regiones relativamente sombrías, el sol puede proporcionar más del 70% de la luz requerida para un cultivo de lechuga de invernadero durante todo el año.
La iluminación suplementaria para la producción de invernadero se utiliza principalmente durante los oscuros meses de invierno cuando el sol es bajo y los días son cortos. Por lo general, los sistemas de iluminación para invernaderos están diseñados de tal manera que puedan proporcionar suficiente luz durante los meses más oscuros del año. Para estimar la cantidad de luz disponible para la producción de cultivos en un lugar determinado, lo ideal sería promediar varios años de datos para que un año atípico tenga un impacto menor en las tendencias generales. En Estados Unidos, un recurso útil es la Base de Datos Nacional de Radiación Solar mantenida por el Laboratorio Nacional de Energías Renovables (NREL) en Golden, Colorado (https://nsrdb.nrel.gov/).
Los datos de radiación solar (es decir, radiación de onda corta que cubre la banda de onda de aproximadamente 300—3,000 nm) disponibles de NREL no se usan específicamente para la producción de plantas y generalmente se expresan en unidades de J m −2 por unidad de tiempo (por ejemplo, una hora o un día). Para convertir esto en una forma más útil para planear sistemas de iluminación suplementarios, se puede utilizar el siguiente multiplicador (Ting y Giacomelli, 1987):
\[ 1\frac{MJ}{m^{2}\text{day}}\text{short wave radiation}=2.0804\frac{\text{mol}}{m^{2}\text{day}}\text{PAR} \]
La base de datos NREL cubre varias ubicaciones fuera de Estados Unidos. Para datos de ubicación más específicos, otras bases de datos meteorológicas mantenidas por gobiernos nacionales o estaciones meteorológicas locales (por ejemplo, estaciones de radio o televisión, aeropuertos) pueden tener disponibles datos históricos de radiación solar a partir de los cuales se pueden calcular integrales de luz natural diaria promedio.
Para la producción en invernadero, el DLI no tiene que ser exactamente el mismo cada día para maximizar la producción. Durante la etapa de plántula, muchos cultivos pueden tolerar DLI mucho más altos que en etapas posteriores de crecimiento. Por ejemplo, la lechuga de invernadero generalmente se limita a 17 mol m −2 d −1 después de que el dosel se haya cerrado, para evitar daños por tipburn (Albright et al., 2000). Sin embargo, las plántulas pueden estar provistas de 20 mol m −2 d −1 y algunas variedades pueden incluso beneficiarse de hasta 30 mol m −2 d −1. Generalmente, para la lechuga hidropónica, es aceptable desviarse no más de 3 mol m −2 d −1 del DLI objetivo, siempre que cualquier superávit (o déficit) sea compensado en los dos días siguientes.
Una vez que se ha determinado la cantidad de iluminación suplementaria necesaria (ya sea el 100% del DLI para una instalación de cultivo interior o alguna otra fracción del DLI para un invernadero), el siguiente paso es determinar qué intensidad de luz se requiere. Para las instalaciones interiores, determinar el nivel de luz de cultivo requerido es sencillo. Para un cultivo como la lechuga donde no hay necesidad de descanso nocturno, se pueden aplicar 24 horas de luz al día. Para un invernadero, el cálculo es el mismo, sin embargo, una porción del DLI será suministrada por luz natural. Todo se reduce a una decisión del diseñador con respecto a cómo quiere dimensionar el sistema de iluminación, y si quieren sobredimensionar o reducir la capacidad de iluminación para considerar días extremadamente oscuros en los que el sistema de iluminación suplementario necesitaría proporcionar casi toda la luz en un invernadero. La mayoría de los sistemas de iluminación suplementaria para invernaderos comerciales proporcionan una intensidad instantánea entre 50 y 200 μmol m −2 s −1 a nivel de cultivo.
La Figura 5.1.9 muestra el incremento en DLI que se puede lograr agregando iluminación suplementaria a tres intensidades diferentes (50, 100 y 150 μmol m −2 s −1), mientras se operan las lámparas durante 18 horas diarias durante noviembre, diciembre, enero y febrero, durante 12 horas diarias durante Octubre, por 11 horas diarias durante marzo, y 2 horas diarias durante septiembre y abril por un total de 2,993 horas al año. Como se muestra en la Figura 5.1.9, el uso de este programa de iluminación y una intensidad de 150 μmol m −2 s −1 da como resultado una integral de luz más constante en el transcurso de un año.
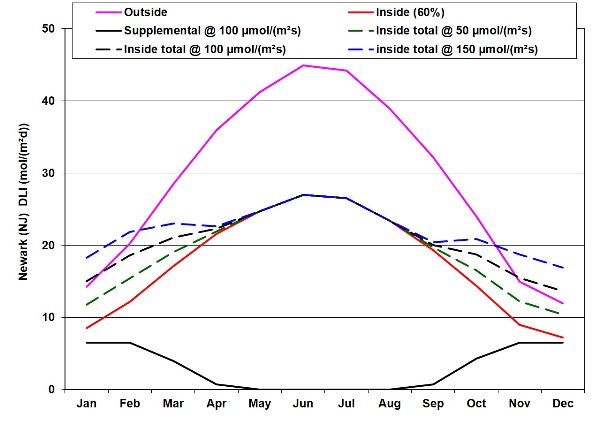
Un factor significativo que afecta las horas por día que se debe suministrar iluminación suplementaria es el precio de la electricidad. Muchos servicios públicos ofrecen incentivos para fomentar el uso de electricidad fuera de las horas pico, para igualar la demanda de electricidad a todos sus clientes. Varía según los proveedores de servicios públicos, pero los ahorros de hasta el 40% en los cargos de suministro de electricidad son comunes para comprar energía fuera de las horas pico. Los periodos típicos de baja actividad corresponden con la noche y la madrugada, por ejemplo de 9:00pm a 7:00am (10 horas). Además de ahorrar en el precio de suministro de electricidad, también puede ser posible evitar cargos por demanda. En las operaciones comerciales que utilizan mucha energía, las empresas eléctricas suelen cobrar cargos por demanda basados en el mayor consumo de 15 minutos en pico (kW) durante un ciclo de facturación mensual. El cargo por demanda puede agregar fácilmente miles de dólares al costo mensual de la factura de electricidad de un productor. Durante los meses de invierno, puede ser inevitable encenderse durante las horas pico de uso, pero durante los meses de hombro cuando aún es necesaria la iluminación suplementaria pero no se usa tanto, puede valer la pena desactivar la iluminación durante las horas pico y suplir cualquier déficit diario al día siguiente durante las horas de menor actividad.
Número de accesorios para lograr una intensidad objetivo
El número de accesorios necesarios para proporcionar la intensidad deseada depende de la salida de luz de cada accesorio y de la altura de montaje. Además, las características de cualquier reflector afectarán tanto la uniformidad como la intensidad de la luz entregada al cultivo (Ciolkosz et al., 2001; Both et al., 2002). La altura de montaje se define como la distancia entre la parte inferior de la lámpara y la parte superior del dosel de la planta.
Idealmente, el fabricante de iluminación tendrá disponible un archivo IES (Illuminating Engineering Society) que contiene datos sobre el patrón de salida de luz específico del dispositivo. Usando el archivo IES y el software disponible comercialmente, es posible diseñar un diseño para lograr una intensidad de luz objetivo a una altura de montaje especificada. Una consideración adicional es la uniformidad de la luz. Idealmente, la luz debe ser lo más uniforme posible para producir un crecimiento consistente en toda la zona de cultivo. Tenga en cuenta que, aunque la intensidad de la luz no cambia mucho una vez que se determina la densidad de la lámpara (Cuadro 5.1.5), la uniformidad de la luz mejora significativamente al aumentar la altura de montaje. Por ejemplo, un invernadero de 0.4 ha (suponiendo una altura de montaje disponible de 2.44 m) necesitaría aproximadamente 383 lámparas HPS (400 W cada una, sin incluir la potencia extraída por el balasto) para una intensidad de luz uniforme de 49 μmol m −2 s −1 y 786 lámparas para la intensidad de 100 μmol m − 2 s −1. Los patrones de montaje adicionales y las intensidades de luz promedio resultantes se muestran en la Tabla 5.1.5.
Número de lámparas por bahía (lámparas por fila, con colocación de lámpara escalonada de fila a fila) |
Área de Piso por Lámpara (m 2) |
Intensidad de luz para una altura de montaje de 2.44 m (μmol m −2 s −1) |
Intensidad de luz para una altura de montaje de 2.13 m (μmol m −2 s −1) |
Intensidad de luz para una altura de montaje de 1.83 m (μmol m −2 s −1) |
Intensidad de luz para una altura de montaje de 1.52 m (μmol m −2 s −1) |
---|---|---|---|---|---|
38 (13-12-13) |
10.6 |
49 |
50 |
51 |
52 |
58 (15-14-15-14) |
6.9 |
75 |
77 |
79 |
80 |
78 (16-15-16-15-16) |
5.15 |
100 |
103 |
105 |
107 |
123 (21-20-21-20-21-20) |
3.26 |
149 |
154 |
158 |
162 |
158 (23-22-23-22-23-22-23) |
2.54 |
202 |
206 |
210 |
213 |
Una consideración adicional en los invernaderos es que aumentar el número de luminarias da como resultado un bloqueo adicional de la luz natural. Además, los cables de alimentación, los balastos y los reflectores pueden bloquear la transmisión de la luz natural, y el invernadero puede requerir una superestructura adicional para proporcionar un lugar para montar los accesorios y ayudar a soportar su peso.
Ejemplos
Ejemplo\(\PageIndex{1}\)
Ejemplo 1: Calefacción de invernadero
Problema:
Determinar la capacidad requerida del sistema de calefacción para un invernadero con las siguientes características:
- • dimensiones del invernadero: 330 por 330 m
- • superficie de invernadero (techo más paredes laterales): 12,700 m 2
- • Volumen de invernadero: 50,110 m 3
- • nivel de humedad exterior: 45%
- • Punto de ajuste de temperatura nocturna: 17°C
- • Nivel de humedad interior: 75%
- • 99% de temperatura de diseño (específica de la ubicación): −15°C
- • Invernadero U -valor: 6.2 W m −2 °C −1
Solución
La capacidad requerida del sistema de calefacción es una función de la pérdida de calor estructural (conducción, convección y radiación), la pérdida de calor por infiltración y la eficiencia de conversión de la fuente de combustible para el sistema de calefacción.
Primero, calcule la pérdida de calor estructural usando la Ecuación 5.1.1:
\( q_{ccr}=UA_{c}(t_{i}-t_{o}) \)(Ecuación\(\PageIndex{1}\))
= 6.2 × 12,700 [17 — (−15)] = 2.519.680 W = 2.519.68 kW
A continuación, determine la pérdida de calor por infiltración usando la Ecuación 5.1.2:
\( q_{i}=\rho _{i}NV[c_{pi}(t_{i}-t_{o})+h_{fg}(W_{i}-W_{o})] \)(Ecuación\(\PageIndex{2}\))
Se requieren algunos supuestos para resolver la Ecuación 5.1.2. Es razonable suponer que la densidad del aire del invernadero es de 1.2 kg m −3. La tasa de infiltración N se puede estimar a partir de los datos incluidos en el Cuadro 5.1.2: se seleccionó un valor de 0.0004 s −1 (un invernadero más antiguo cubierto de vidrio con buen mantenimiento). Para determinar las relaciones de humedad para el aire interior y exterior, necesitamos usar la humedad relativa del aire interior y exterior. Utilizando la tabla psicrométrica (Figura 5.1.1), las relaciones de humedad para el aire interior y exterior son 0.0091 y 0.0005 kg kg −1, respectivamente. El calor específico del aire de invernadero a 17°C es de 1.006 kJ kg −1 K −1 y el calor latente de vaporización del agua a esa temperatura es de aproximadamente 2,460 kJ kg −1. Estos valores se determinaron a partir de calculadoras en línea (Engineering Toolbox, 2004, 2010), pero también se pueden encontrar comúnmente en libros de texto de ingeniería sobre transferencia de calor y masa. Introduciendo estos valores en la Ecuación 5.1.2:
\( q_{i}=\rho _{i}NV[c_{pi}(t_{i}-t_{o})+h_{fg}(W_{i}-W_{o})] \)(Ecuación\(\PageIndex{2}\))
= 1.2 × 0.0004 × 50,110 {1.006 [17 — (−15)] + 2,460 (0.0091—0.0005)}
= 1,283,169 W = 1,283.17 kW
Así, la pérdida de calor resultante es la suma de la pérdida de calor estructural (conducción, convección y radiación) y la pérdida de calor por infiltración: 2,519.68 + 1,283.17 = aproximadamente 3803 kW.
La capacidad del sistema de calefacción es la pérdida total de calor dividida por la eficiencia de conversión de la fuente de combustible. Para el gas natural con una eficiencia de conversión del 85%, la capacidad total requerida del sistema de calefacción es 3803/0.85 = 4,474 kW.
Tenga en cuenta que si estos cálculos se hacen en una hoja de cálculo, es fácil ajustar los supuestos que se hicieron para que se pueda evaluar la sensibilidad de la respuesta final a la magnitud de los supuestos. Además, en climas más fríos, se puede perder calor adicional alrededor del perímetro de un invernadero donde el suelo frío y húmedo está en contacto directo con la pasarela perimetral dentro del invernadero. Para evitar esta pérdida de calor perimetral, se pueden instalar placas aislantes colocadas verticalmente extendiéndose desde el nivel del suelo hasta una profundidad de 50—60 cm.
Ejemplo\(\PageIndex{2}\)
Ejemplo 2: Almohadilla de Enfriamiento Evaporativo
Problema:
Encuentre la caída de temperatura esperada del aire que pasa a través de la almohadilla de enfriamiento evaporativo dada la siguiente información:
- • el ambiente (aire exterior) está a 25 °C de temperatura de bulbo seco y 50% de humedad relativa
- • la eficiencia de la almohadilla de enfriamiento evaporativo es del 80%
Solución
Utilizando el gráfico psicrométrico (Figura 5.1.10) y las condiciones iniciales del aire exterior de 25° C de temperatura de bulbo seco y 50% de humedad relativa, comienzan en la intersección de la línea curva 50% RH con la línea vertical para una temperatura de bulbo seco de 25°C.En esta intersección, determinar lo siguiente parámetros ambientales:
- • temperatura de bulbo húmedo = 17.8°C (desde el punto de partida, seguir la línea de entalpía constante, 50.3 kJ kg −1 en este caso, hasta que se cruza con la curva de humedad relativa del 100%)
- • temperatura del punto de rocío = 13.7°C
- • relación de humedad = 0.0099 kg kg −1,
- • entalpía = 50.3 kJ kg −1
- • volumen específico = 0.858 m 3 kg −1
Por lo tanto, la depresión de bulbo húmedo para este ejemplo es igual a 25 — 17.8 = 7.2°C. El uso de una eficiencia global del sistema de enfriamiento evaporativo de 80% da como resultado una caída de temperatura práctica de aproximadamente 5.8°C (7.2°C × 0.8). A medida que el aire continúa viajando a través del invernadero en su camino hacia los extractores, el aire de salida se calentará y se agregará humedad de la transpiración de los cultivos por lo que el aire que sale tendrá mayor contenido de energía y humedad específica que el aire que se mueve a través de la almohadilla de enfriamiento evaporativo.
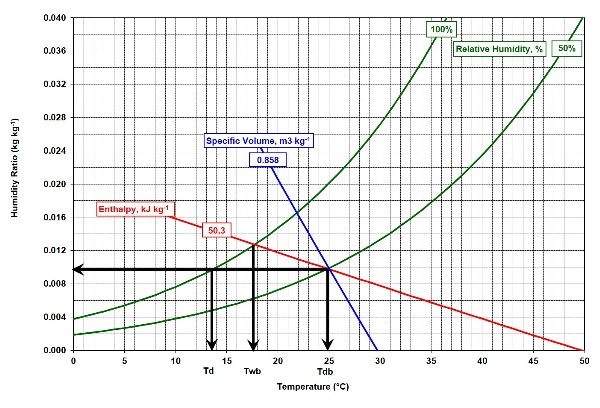
Ejemplo\(\PageIndex{3}\)
Ejemplo 3: Costos de compra y operación de sistemas de iluminación de cultivos
Problema:
Como se mencionó anteriormente, el rendimiento de las lámparas en términos de su eficacia puede variar significativamente incluso al comparar el mismo tipo de lámpara. Por ejemplo, se midieron valores de eficacia del aparato HPS que oscilaban entre 0.94 y 1.7 μmol J −1. Junto con la eficacia, el costo unitario de comprar lámparas también es una consideración importante a la hora de decidir sobre un sistema de iluminación. En este ejemplo, analizamos el costo de comprar y operar dos tipos de sistemas de iluminación, tanto en un invernadero como en una instalación de cultivo interior.
Encuentre el ahorro anual de costos de operar un sistema LED vs HPS, y cuánto tiempo deben ser operados los sistemas para justificar (amortización) el mayor precio de compra del sistema de iluminación LED, tanto en invernadero como en sistema de producción interior (sin luz natural), dado lo siguiente:
- • Sistema de iluminación HPS: 123 accesorios, cada uno de 400 W (más 60 W por cada balasto), costo de $300 por accesorio (excluyendo costo de instalación), eficacia de 0.94 μmol J −1
- • Sistema de iluminación LED: 55 luminarias, cada una de 400 W (más 20 W por cada controlador), costo de $1,200 por accesorio (excluyendo el costo de instalación), eficacia de 2.1 μmol J −1 (estas luminarias LED están pensadas como un reemplazo directo para el sistema de iluminación HPS, lo que significa que entregan la misma intensidad PAR y distribución a nivel de cultivo)
- • Invernadero: 2,200 horas de iluminación suplementaria al año (600 h durante las tarifas de electricidad en pico y 1,600h durante las tarifas de electricidad fuera de pico)
- • Instalación de cultivo interior (sin luz natural): 8,760 horas de iluminación al año (5,100 h en pico y 3,660 h fuera de pico)
- • Precios de la electricidad de $0.14 por kWh en pico y $0.09 por kWh fuera de pico.
Solución
Ahora podemos comparar el costo para comprar y operar los accesorios. El precio de compra de los dos sistemas es simplemente el costo unitario multiplicado por el número de unidades:
\( \text{HPS purchase cost}=\frac{\$ 300}{\text{fixture}}\times 123 \text{ fixtures} = \$ 36,900 \)
\( \text{LED purchase cost}=\frac{\$ 1,200}{\text{fixture}}\times 55 \text{ fixtures} = \$ 66,000 \)
Para el caso del invernadero, el costo de electricidad de los dos sistemas de iluminación se puede determinar tanto para uso en pico como fuera de pico:
\( \text{HPS on-peak cost}= 123 \text{ fixtures} \times \frac{460\ W}{\text{fixture}}\times \frac{1\ kW}{1000\ W}\times \frac{600 \text{ h on-peak}}{\text{year}} \times \frac{\$ 0.14}{kWh} =\frac{\$ 4,753}{\text{year}} \)
\( \text{HPS off-peak cost}= 123 \text{ fixtures} \times \frac{460\ W}{\text{fixture}}\times \frac{1\ kW}{1000\ W}\times \frac{1,600 \text{ h off-peak}}{\text{year}} \times \frac{\$ 0.09}{kWh} =\frac{\$ 8,148}{\text{year}} \)
Sumar estos costos da como resultado un costo anual de electricidad para HPS de $12,901 por año (excluyendo cualquier cargo por demanda potencial).
\( \text{LED on-peak cost}= 55 \text{ fixtures} \times \frac{420\ W}{\text{fixture}}\times \frac{1\ kW}{1000\ W}\times \frac{600 \text{ h on-peak}}{\text{year}} \times \frac{\$ 0.14}{kWh} =\frac{\$ 1,940}{\text{year}} \)
\( \text{LED off-peak cost}= 55 \text{ fixtures} \times \frac{420\ W}{\text{fixture}}\times \frac{1\ kW}{1000\ W}\times \frac{1,600 \text{ h on-peak}}{\text{year}} \times \frac{\$ 0.09}{kWh} =\frac{\$ 3,326}{\text{year}} \)
Sumar estos costos da como resultado un costo anual de electricidad para LED de $5,266 al año (excluyendo cualquier cargo por demanda potencial).
El ahorro anual de costos para el consumo de electricidad al usar el LED en lugar de los accesorios HPS asciende a $12,901 — $5,266 = $7,635.
La prima por comprar LED en lugar de los accesorios HPS es de $29,100 ($66,000 — $36,900). Por lo tanto, tomaría\(\frac{\$ 29,100}{\$ 7,635} = 3.8\text{ years}\) de operación recuperar (pagar) el mayor precio de compra de las luminarias LED en situación de invernadero.
Para el caso de una instalación de cultivo interior, donde toda la iluminación tuvo que ser suministrada por los accesorios de la lámpara, y asumiendo que las luces necesarias para operar las 24 horas del día para cumplir con la integral de luz objetivo, el ahorro anual de costos para el consumo de electricidad al usar el LED en lugar de los accesorios HPS asciende a $34 ,933 ($50,035 — $24,102). Por lo tanto, tomaría\(\frac{\$ 29,100}{\$ 34,933} = 0.83\text{ years}\) de operación recuperar (pagar) el mayor precio de compra de los accesorios LED.
Créditos de imagen
Figura 1. Ambos, A. J. (CC Por 4.0). (2020). Gráfico psicrométrico.
Figura 2. Ambos, A. J. (CC Por 4.0). (2020). Sistema de enfriamiento evaporativo (almohadilla y ventilador).
Figura 3. Ambos, A. J. (CC Por 4.0). (2020). Invernaderos conectados a canaleta.
Figura 4. Ambos, A. J. (CC Por 4.0). (2020). Sensibilidad del ojo humano y de la planta.
Figura 5. Izquierda. Ambos, A. J. (2020). Plantas de lechuga.
Figura 5. Derecha. Universidad de Cornell. (CC Por 4.0). Plantas de Lechuga. Recuperado de https://urbanagnews.com/blog/prevent-tipburn-on-greenhouse-lettuce/. [Uso justo].
Figura 6. Ambos, A. J. (CC Por 4.0). (2020). Luminarias HPS y LED.
Figura 7. Ambos, A. J. (CC Por 4.0). (2020). Calentador de unidad.
Figura 8. Ambos, A. J. (CC Por 4.0). (2020). Sistema de calentamiento de agua caliente.
Figura 9. Ambos, A. J. (CC Por 4.0). (2020). Integrales de radiación solar.
Figura 10. Ambos, A. J. (CC Por 4.0). (2020). Gráfico psicrométrico simplificado.
Referencias
Albright, L. D., Ambos, A. J., & Chiu, A. J. (2000). Controlar la luz del invernadero a una integral diaria consistente. Trans. ASAE, 43 (2), 421—431. https://doi.org/10.13031/2013.2721.
Aldrich, R. A., & Bartok, J. W. (1994). Ingeniería de invernaderos. NRAES Publ. No. 33. Recuperado de https://vdocuments.site/fair-use-of-this-pdf-file-of-greenhouse-engineering-nraes-33-by-.html.
Estándares ASABE. (2017). ANSI/ASABE S640: Cantidades y unidades de radiación electromagnética para plantas (organismos fotosintéticos). San José, MI: ASABE.
Normas ASAE. (2003). ANSI/ASAE EP406.4: Calefacción, ventilación y refrigeración de invernaderos. Nota: Esta es una norma retirada y archivada. San José, MI: ASAE.
ASHRAE. (2013). Estándar ASHRAE 169-2013: Datos meteorológicos para estándares de diseño de edificios. Atlanta, GA: ASHRAE.
Ambos, A. J., Albright, L. D., Langhans, R. W., Vinzant, B. G., & Walker, P. N. (1997). Consumo de energía eléctrica y salida PPF de nueve luminarias de sodio de alta presión de 400 vatios y una aplicación de los resultados en invernadero. Acta Hortic., 418, 195—202.
Ambos, A. J., Benjamin, L., Franklin, J., Holroyd, G., Incoll, L. D., Lefsrud, M. G., & Pitkin, G. (2015). Lineamientos para medir y reportar parámetros ambientales para experimentos en invernaderos. Métodos de Planta, 11 (43). https://doi.org/10.1186/s13007-015-0083-5.
Ambos, A. J., Bugbee, B., Kubota, C., López, R. G., Mitchell, C., Runkle, E. S., & Wallace, C. (2017). Propuesta de etiqueta de producto para lámparas eléctricas utilizadas en las ciencias de las plantas. Horttechnol., 27 (4), 544—549. https://doi.org/10.21273/horttech03648-16.
Ambos, A. J., Ciolkosz, D. E., & Albright, L. D. (2002). Evaluación de la uniformidad de la luz bajo sistemas de iluminación suplementarios. Acta Hortic., 580, 183—190.
Ciolkosz, D. E., Ambos, A. J., & Albright, L. D. (2001). Selección y colocación de luminarias de invernadero para mayor uniformidad. Appl. Ing. Agric., 17 (6), 875—882. https://doi.org/10.13031/2013.6842.
Comisión Internacional de l'Eclairage. (1931). Proc. Octava Sesión. Cambridge, Reino Unido: Cambridge University Press.
Crawley, D. B., Lawrie, L. K., Winkelmann, F. C., Buhl, W. F., Huang, Y. J., Pedersen, C.O.,. Glazer, J. (2001). EnergyPlus: Creación de un programa de simulación de energía de edificios de nueva generación. Construcción Energética., 33 (4), 319—331. http://dx.doi.org/10.1016/S0378-7788(00)00114-6.
Engineering ToolCaja de Herramientas. (2004). Aire: calor específico a presión constante y temperatura variable. Recuperado de https://www.engineeringtoolbox.com/air-specific-heat-capacity-d_705.html.
Engineering ToolCaja de Herramientas. (2010). Agua: calor de vaporización. Recuperado de https://www.engineeringtoolbox.com/water-properties-d_1573.html.
Kubota, C., Kroggel, M., Ambos, A. J., Burr, J. F., & Whalen, M. (2016). ¿Tiene sentido la iluminación suplementaria para mi cultivo? —Evaluaciones empíricas. Acta Hortic., 1134, 403—411. http://dx.doi.org/10.17660/ActaHortic.2016.1134.52.
Lopez, R., & Runkle, E. S. (Eds.). (2017). Gestión de la luz en ambientes controlados. Willoughby, OH: Meister Media Worldwide.
Marcelis, L. F. M., Broekhuijsen, A. G. M., Meinen, E., Nijs, E. M. F. M., & Raaphorst, M. G. M. (2006). Cuantificación de la respuesta de crecimiento a la cantidad ligera de cultivos de invernadero. Acta Hortic., 711, 97—103. https://doi.org/10.17660/ActaHortic.2006.711.9.
Mitchell, C. A., Ambos, A. J., Bourget, C. M., Burr, J. F., Kubota, C., López, R. G.,. Runkle, E. S. (2012). LEDs: ¡El futuro de la iluminación de invernaderos! Crón. Hortic., 52 (1), 6—12.
Mitchell, C. A., Dzakovich, M. P., Gómez, C., López, R., Burr, J. F., Hernández, R.,. Ambos, A. J. (2015). Diodos emisores de luz en horticultura. Hortic. Rev., 43, 1—87.
Sager, J. C., Smith, W. O., Edwards, J. L., & Cyr, K. L. (1988). Eficiencia fotosintética y determinación de fotoequilibrios de fitocromo mediante datos espectrales. Trans. ASAE, 31 (6), 1882—1889. https://doi.org/10.13031/2013.30952.
Ting, K. C., & Giacomelli, G. A. (1987). Disponibilidad de radiación solar fotosintéticamente activa. Trans. ASAE, 30 (5), 1453—1457. https://doi.org/10.13031/2013.30585.
USDA-ARS. (2019). Cultivador virtual 3.0. Washington, DC: Departamento de Agricultura de Estados Unidos. https://www.ars.usda.gov/research/software/download/?softwareid=309.
Wallace, C. & Ambos, A. J. (2016). Evaluación de las características de operación de fuentes de luz para aplicaciones hortícolas. Acta Hortic., 1134, 435—443. https://doi.org/10.17660/ActaHortic.2016.1134.55.