3.3: Cosecha y Manejo de Granos
- Page ID
- 80907
\( \newcommand{\vecs}[1]{\overset { \scriptstyle \rightharpoonup} {\mathbf{#1}} } \)
\( \newcommand{\vecd}[1]{\overset{-\!-\!\rightharpoonup}{\vphantom{a}\smash {#1}}} \)
\( \newcommand{\id}{\mathrm{id}}\) \( \newcommand{\Span}{\mathrm{span}}\)
( \newcommand{\kernel}{\mathrm{null}\,}\) \( \newcommand{\range}{\mathrm{range}\,}\)
\( \newcommand{\RealPart}{\mathrm{Re}}\) \( \newcommand{\ImaginaryPart}{\mathrm{Im}}\)
\( \newcommand{\Argument}{\mathrm{Arg}}\) \( \newcommand{\norm}[1]{\| #1 \|}\)
\( \newcommand{\inner}[2]{\langle #1, #2 \rangle}\)
\( \newcommand{\Span}{\mathrm{span}}\)
\( \newcommand{\id}{\mathrm{id}}\)
\( \newcommand{\Span}{\mathrm{span}}\)
\( \newcommand{\kernel}{\mathrm{null}\,}\)
\( \newcommand{\range}{\mathrm{range}\,}\)
\( \newcommand{\RealPart}{\mathrm{Re}}\)
\( \newcommand{\ImaginaryPart}{\mathrm{Im}}\)
\( \newcommand{\Argument}{\mathrm{Arg}}\)
\( \newcommand{\norm}[1]{\| #1 \|}\)
\( \newcommand{\inner}[2]{\langle #1, #2 \rangle}\)
\( \newcommand{\Span}{\mathrm{span}}\) \( \newcommand{\AA}{\unicode[.8,0]{x212B}}\)
\( \newcommand{\vectorA}[1]{\vec{#1}} % arrow\)
\( \newcommand{\vectorAt}[1]{\vec{\text{#1}}} % arrow\)
\( \newcommand{\vectorB}[1]{\overset { \scriptstyle \rightharpoonup} {\mathbf{#1}} } \)
\( \newcommand{\vectorC}[1]{\textbf{#1}} \)
\( \newcommand{\vectorD}[1]{\overrightarrow{#1}} \)
\( \newcommand{\vectorDt}[1]{\overrightarrow{\text{#1}}} \)
\( \newcommand{\vectE}[1]{\overset{-\!-\!\rightharpoonup}{\vphantom{a}\smash{\mathbf {#1}}}} \)
\( \newcommand{\vecs}[1]{\overset { \scriptstyle \rightharpoonup} {\mathbf{#1}} } \)
\( \newcommand{\vecd}[1]{\overset{-\!-\!\rightharpoonup}{\vphantom{a}\smash {#1}}} \)
\(\newcommand{\avec}{\mathbf a}\) \(\newcommand{\bvec}{\mathbf b}\) \(\newcommand{\cvec}{\mathbf c}\) \(\newcommand{\dvec}{\mathbf d}\) \(\newcommand{\dtil}{\widetilde{\mathbf d}}\) \(\newcommand{\evec}{\mathbf e}\) \(\newcommand{\fvec}{\mathbf f}\) \(\newcommand{\nvec}{\mathbf n}\) \(\newcommand{\pvec}{\mathbf p}\) \(\newcommand{\qvec}{\mathbf q}\) \(\newcommand{\svec}{\mathbf s}\) \(\newcommand{\tvec}{\mathbf t}\) \(\newcommand{\uvec}{\mathbf u}\) \(\newcommand{\vvec}{\mathbf v}\) \(\newcommand{\wvec}{\mathbf w}\) \(\newcommand{\xvec}{\mathbf x}\) \(\newcommand{\yvec}{\mathbf y}\) \(\newcommand{\zvec}{\mathbf z}\) \(\newcommand{\rvec}{\mathbf r}\) \(\newcommand{\mvec}{\mathbf m}\) \(\newcommand{\zerovec}{\mathbf 0}\) \(\newcommand{\onevec}{\mathbf 1}\) \(\newcommand{\real}{\mathbb R}\) \(\newcommand{\twovec}[2]{\left[\begin{array}{r}#1 \\ #2 \end{array}\right]}\) \(\newcommand{\ctwovec}[2]{\left[\begin{array}{c}#1 \\ #2 \end{array}\right]}\) \(\newcommand{\threevec}[3]{\left[\begin{array}{r}#1 \\ #2 \\ #3 \end{array}\right]}\) \(\newcommand{\cthreevec}[3]{\left[\begin{array}{c}#1 \\ #2 \\ #3 \end{array}\right]}\) \(\newcommand{\fourvec}[4]{\left[\begin{array}{r}#1 \\ #2 \\ #3 \\ #4 \end{array}\right]}\) \(\newcommand{\cfourvec}[4]{\left[\begin{array}{c}#1 \\ #2 \\ #3 \\ #4 \end{array}\right]}\) \(\newcommand{\fivevec}[5]{\left[\begin{array}{r}#1 \\ #2 \\ #3 \\ #4 \\ #5 \\ \end{array}\right]}\) \(\newcommand{\cfivevec}[5]{\left[\begin{array}{c}#1 \\ #2 \\ #3 \\ #4 \\ #5 \\ \end{array}\right]}\) \(\newcommand{\mattwo}[4]{\left[\begin{array}{rr}#1 \amp #2 \\ #3 \amp #4 \\ \end{array}\right]}\) \(\newcommand{\laspan}[1]{\text{Span}\{#1\}}\) \(\newcommand{\bcal}{\cal B}\) \(\newcommand{\ccal}{\cal C}\) \(\newcommand{\scal}{\cal S}\) \(\newcommand{\wcal}{\cal W}\) \(\newcommand{\ecal}{\cal E}\) \(\newcommand{\coords}[2]{\left\{#1\right\}_{#2}}\) \(\newcommand{\gray}[1]{\color{gray}{#1}}\) \(\newcommand{\lgray}[1]{\color{lightgray}{#1}}\) \(\newcommand{\rank}{\operatorname{rank}}\) \(\newcommand{\row}{\text{Row}}\) \(\newcommand{\col}{\text{Col}}\) \(\renewcommand{\row}{\text{Row}}\) \(\newcommand{\nul}{\text{Nul}}\) \(\newcommand{\var}{\text{Var}}\) \(\newcommand{\corr}{\text{corr}}\) \(\newcommand{\len}[1]{\left|#1\right|}\) \(\newcommand{\bbar}{\overline{\bvec}}\) \(\newcommand{\bhat}{\widehat{\bvec}}\) \(\newcommand{\bperp}{\bvec^\perp}\) \(\newcommand{\xhat}{\widehat{\xvec}}\) \(\newcommand{\vhat}{\widehat{\vvec}}\) \(\newcommand{\uhat}{\widehat{\uvec}}\) \(\newcommand{\what}{\widehat{\wvec}}\) \(\newcommand{\Sighat}{\widehat{\Sigma}}\) \(\newcommand{\lt}{<}\) \(\newcommand{\gt}{>}\) \(\newcommand{\amp}{&}\) \(\definecolor{fillinmathshade}{gray}{0.9}\)Tim Stombaugh
Biosistemas e Ingeniería Agropecuaria
Universidad de Kentucky
Lexington, Kentucky, Estados Unidos
Términos Clave |
Rendimiento | Eficiencia | Disociación |
Productividad | Procesos funcionales | Separación |
Calidad | Compromiso | Transporte |
Variables
Nota sobre las unidades: En esta lista de variables se dan las dimensiones de las variables. En el texto, las definiciones de variables incluyen dimensiones así como unidades SI de ejemplo para ilustración.
Introducción
Una habilidad única que los ingenieros de biosistemas deben desarrollar es la capacidad de comprender cómo los sistemas mecánicos interactúan con los sistemas biológicos. Esta interacción es muy prevalente en el diseño de maquinaria y sistemas para cosechar granos como maíz (maíz, Zea mays), soya (Glycine max), trigo (Triticum) o canola (Brassica napus). Las máquinas deben atravesar un campo en un suelo biológicamente activo para involucrar a las plantas que crecen en ese campo. La variabilidad en las propiedades de las plantas y del suelo (por ejemplo, madurez, contenido de humedad e integridad estructural) dentro de un campo puede ser extensa. Esta variabilidad presenta un desafío para los ingenieros de diseño para concebir máquinas que puedan adaptarse a esta variabilidad y proporcionar al operador de la máquina la flexibilidad necesaria para enganchar adecuadamente las plantas. El objetivo de este capítulo es sentar las bases de ingeniería necesarias para diseñar sistemas de maquinaria para cosechar granos.
Conceptos
Una clave para convertirse en un gran ingeniero es la capacidad de identificar y comprender el problema central a resolver. Con demasiada frecuencia, los ingenieros se enfocan en mejorar las soluciones actuales a los problemas en lugar de buscar mejores soluciones. En el caso de la cosecha de granos, el ingeniero podría verse tentado a enfocarse en formas de mejorar la cosechadora de granos (Figura 3.3.1), que es la máquina más utilizada para cosechar grano. Las soluciones de ingeniería más singulares y creativas a menudo llegarán solo cuando el ingeniero se centre en identificar el problema fundamental a resolver.
Con la cosecha de granos, el reto central es recuperar una determinada fracción o fracciones de las plantas en un cultivo de grano que se cultiva en campos grandes. La fracción que se va a recuperar puede variar según la planta y por la situación. En la cosecha de maíz (maíz, Zea mays), por ejemplo, la fracción vegetal más comúnmente cosechada es el grano, que se utiliza en una variedad de productos que incluyen alimentos, azúcar y producción de biocombustibles. Para la cosecha de maíz dulce de mercado fresco, se recupera toda la mazorca con las cáscaras intactas. En algunos sistemas de producción animal, se recupera toda la oreja sin cáscara para alimentación animal; en otros sistemas de producción animal, se cosecha toda la planta y se ensila para su alimentación. En estos ejemplos, la madurez y el contenido de humedad del material vegetal pueden ser drásticamente diferentes si el maíz se está recuperando para la producción de azúcar, alimentación animal o consumo humano. Un desafío adicional puede existir cuando se cosechan múltiples fracciones de plantas para diferentes propósitos. En la producción industrial de cáñamo (cannabis), por ejemplo, las semillas de la planta podrían recuperarse para la producción de petróleo o alimentos, y los tallos de la planta podrían recuperarse por separado para la producción de fibra. La pluralidad de corrientes de producción no serán independientes entre sí y deben ser consideradas en el diseño de la solución de mecanización. Este capítulo se centra en los sistemas donde solo se recupera el grano.
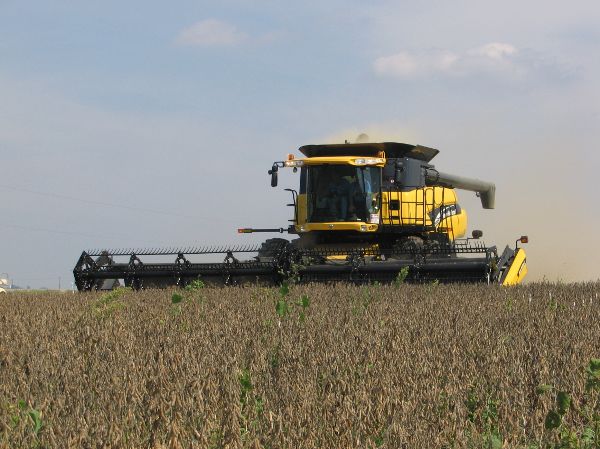
Rendimiento
El rendimiento de una máquina o sistema de cosecha de granos se puede medir utilizando tres métricas generales: productividad, calidad y eficiencia.
Productividad
La productividad de una máquina cosechadora u operación es una medida de cuánto trabajo útil se logra. Como se describe en la Norma ASABE EP496.3 (2015a), se puede cuantificar usando dos métricas primarias. Primero, se puede medir sobre una base de área indicando qué parte del área de un campo se cubrió por unidad de tiempo. Esta métrica se expresa como la capacidad efectiva de campo (C a) y se puede calcular como:
\[ C_{a}=swE_{f} \]
donde C a = capacidad efectiva de campo en área por unidad de tiempo (m 2 h −1)
s = velocidad de campo en distancia por unidad de tiempo (m h −1)
w = ancho de la máquina (m)
E f = eficiencia de campo (decimal)
En segundo lugar, la productividad se puede medir sobre una base material indicando la cantidad de grano que se recupera por unidad de tiempo. La capacidad material (C m) está relacionada con la capacidad del área por:
\[ C_{m}=C_{a}y \]
donde C m = capacidad del material en peso o volumen por unidad de tiempo (m 3 h −1)
y a = rendimiento de cultivo recuperado (cosechado) en peso o volumen por unidad de área (m 3 m −2)
Commodity | Contenido de humedad (%) |
Peso (lb/bushel) |
Peso (kg/bushel) |
---|---|---|---|
Maíz (Zea mays) |
15.5 |
56 |
25.40 |
Soja (Glycine max) |
13 |
60 |
27.22 |
Girasol (Helianthus annuus) |
10 |
100 |
45.36 |
Trigo (Triticum aestivum) |
13.5 |
60 |
27.22 |
La capacidad del material se puede reportar sobre una base de volumen o masa con una conversión de densidad apropiada. En el comercio internacional, la cantidad de granos se reporta típicamente en toneladas métricas. En la producción de granos en Estados Unidos, la cantidad de grano se mide comúnmente usando unidades de bushels. Si bien un bushel es técnicamente una medida de volumen igual a 35.239 L, en la producción de grano es una unidad que refleja un peso estandarizado de grano con un contenido de humedad particular especificado para ese grano. Los pesos estandarizados de un bushel de grano para algunos cultivos comunes se enumeran en el Cuadro 3.3.1.
Calidad
La segunda medida de desempeño de un sistema de cosecha de granos mecanizados es la calidad del producto. Idealmente, el producto (grano) que se recupera está libre de cualquier materia extraña y daño, pero esto rara vez es el caso. Pequeñas piezas de material vegetal y otras materias extrañas a menudo se capturan con el grano. La maquinaria también puede causar daños físicos a los granos a medida que pasan por los diferentes mecanismos. El diseño de la máquina, así como las condiciones de cultivo y operación, pueden tener un efecto sobre las materias extrañas y los daños, que a menudo se conocen colectivamente como atraque. El término atraque se utiliza porque los productores generalmente incurren en una sanción económica (atracado alguna cantidad) del valor de mercado del grano por parte del comprador si el grano está dañado, contiene materia extraña excesiva, o no está en el contenido de humedad adecuado.
Eficiencia
La tercera medida de desempeño, la eficiencia, se puede cuantificar de dos maneras. El primero es una eficiencia de campo basada en el tiempo (E f) que relaciona el tiempo real requerido para completar una operación de campo con el tiempo teórico de finalización si no hubiera habido demoras, como dar la vuelta al final del campo, reparación de la máquina y roturas del operador. La eficiencia de campo se calcula como:
\[ E_{f} = \frac{T_{t}}{T_{a}} \]
donde T t = tiempo de finalización teórica
T a = tiempo real de finalización
La eficiencia también se puede medir en función de la integridad de la operación de cosecha. Esta eficiencia de cosecha (E h) es una medida de la cantidad de producto deseable que realmente se recupera en relación con la cantidad de producto que originalmente estaba disponible para la máquina cosechadora. Se calcula como:
\[ E_{h} = \frac{y_{a}}{y_{p}} \]
donde y a = rendimiento real de grano recuperado medido en peso por unidad de área (kg m −2)
y p = rendimiento potencial de grano en campo medido en peso por unidad de área (kg m −2)
La antítesis de la eficiencia de cosecha es la pérdida de cosecha (L h), que es la cantidad de grano perdido por la máquina cosechadora por unidad de área expresada como porcentaje del rendimiento potencial. Se puede calcular como:
\[ L_{h} = 1-E_{h} \]
Al enfocarse en la operación de cosecha, se considera que el rendimiento potencial del cultivo es el grano cosechable que aún está adherido a las plantas. El rendimiento potencial no considera los granos que han caído de las plantas antes de que la máquina los acople. Si la cosecha se retrasa después del tiempo óptimo, el rendimiento potencial a menudo disminuirá debido a las fuerzas naturales que hacen que las semillas caigan de las plantas. Esta pérdida de rendimiento previo a la cosecha (y ph) es la cantidad de grano que se pierde antes de la cosecha expresada sobre una base por área. Es la diferencia entre el rendimiento total que las plantas realmente produjeron (y t) y el rendimiento potencial cosechable:
\[ y_{ph} = y_{t}-y_{p} \]
A menudo hay fuertes interrelaciones entre la productividad, la calidad del grano y la eficiencia de la cosecha de granos. Por ejemplo, un aumento en la productividad podría realizarse mediante un aumento en la velocidad o la eficiencia del campo; sin embargo, la calidad del grano y la eficiencia de la cosecha pueden verse comprometidas. Encontrar el punto de operación fiscalmente óptimo es un desafío que debe ser abordado tanto por el ingeniero de diseño como por el operador de la máquina. El ingeniero debe comprender las necesidades del operador e incorporar la flexibilidad de control adecuada en el diseño de la máquina.
Procesos Funcionales
Al considerar el diseño de cualquier sistema de mecanización, el ingeniero debe primero considerar cuidadosamente los procesos potenciales que se tendrán que emprender para completar la tarea. Srivastava et al. (2006) amplían un número de procesos funcionales que podrían ocurrir en la cosecha de grano. Estos procesos pueden simplificarse a cuatro procesos principales:
- • Involucrar el cultivo para establecer el control mecánico del grano.
- • Disociar o romper la conexión entre los granos individuales y la planta.
- • Separar el grano de todo el resto del material vegetal.
- • Transportar el grano a la instalación receptora adecuada.
Dependiendo del sistema específico, estas funciones podrían tener lugar en orden variable, y algunos procesos pueden repetirse varias veces. Históricamente, antes de que se desarrollaran las cosechadoras móviles de granos, un proceso de cosecha implicaba recolectar toda la planta de un campo y transportarla a una ubicación central donde los granos se separaban (trillaban) del material vegetal ya sea a mano o con una máquina estacionaria. Con las máquinas cosechadoras modernas, la disociación y separación del grano se logra a medida que la máquina se mueve por el campo, y el único material que se transporta lejos del campo es el grano. Del mismo modo, algunas funciones pueden realizarse varias veces. Por ejemplo, a menudo hay varias etapas de separación en una sola máquina, y el producto puede transportarse varias veces entre diferentes mecanismos, unidades de almacenamiento temporal y vehículos de transporte antes de llegar al destino final.
Compromiso
El proceso de enganchar el cultivo puede ocurrir de muchas maneras diferentes dependiendo del cultivo particular y la configuración de la máquina. A menudo hay algún tipo de mecanismo que agarrará o jalará el cultivo en pie hacia la máquina a medida que avanza. El mecanismo de agarre podría ser mecánico, como un brazo giratorio o cadena, o podría involucrar otras fuerzas como la neumática o la gravedad. El acoplamiento puede incluir una acción de corte que corta la parte de la planta que contiene el grano del resto de la planta. Las acciones de agarre y corte generalmente dan como resultado que el material quede atrapado en alguna superficie donde luego se puede mover a la máquina.
Disociación
La función de disociación de un proceso de cosecha de grano implica romper físicamente la conexión entre la partícula deseada y la planta. El término trilla se usa a menudo para describir la función de disociación, pero en algunos contextos, la trilla también podría incluir algunas funciones de separación y limpieza. El rendimiento de disociación de una máquina cosechadora se cuantifica por la pérdida por trilla, L th, que es la cantidad de grano que permanece conectado a las plantas expresada como porcentaje de la cantidad total de grano que se presentó al mecanismo de trilla.
Los ingenieros que diseñan mecanismos para disociar el grano necesitan comprender los principios básicos de la falla por tracción y flexión. La mayoría de los granos están unidos a la planta por algún tipo de tallo y/o tejido conectivo. El tejido conectivo a menudo se puede entender como un haz cilíndrico de tejido conectivo. La mayoría de los mecanismos de disociación aplican una fuerza de tracción, una fuerza de flexión o una combinación de las dos sobre la semilla en relación con la planta (Figura 3.3.2). El objetivo de la aplicación de fuerza es provocar una falla del tejido conectivo entre el grano y el tallo o planta. La falla ocurrirá cuando la tensión en el tejido conectivo supere su límite elástico final, que es la tensión a la que se romperá el material. Obviamente, es deseable que la falla de disociación se produzca lo más cerca posible del grano individual para que no haya tallo u otro material vegetal capturado con el grano.
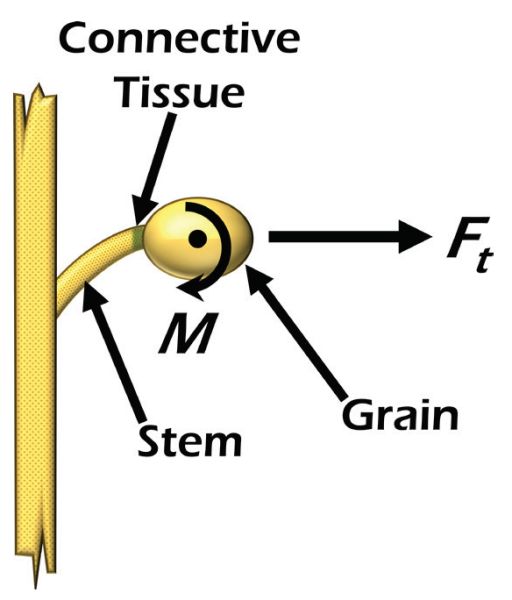
La falla por tracción es el modo en el que el grano se tira directamente del vástago hasta que falla la conexión. La fuerza de tracción lineal induce esfuerzos en el tejido conectivo que se pueden calcular mediante la siguiente ecuación:
\[ \sigma_{t} = \frac{F_{t}}{A} \]
donde σ t = tensión de tracción en el tejido conectivo medida en fuerza por unidad de área (N m −2)
F t = fuerza de tracción que actúa sobre el tejido conectivo (N)
A = área transversal del tejido conectivo (m 2)
La falla de flexión ocurre cuando el grano se gira en relación con el tallo induciendo tensión de flexión en el tejido conectivo. La fuerza de flexión o el momento (M) también se puede considerar como un par de rotación aplicado al grano. La tensión de flexión se describe mediante la siguiente ecuación:
\[ \sigma_{b} = \frac{M_{y}}{I} \]
donde σ b = esfuerzo de flexión en el tejido conectivo medido en fuerza por unidad de área (N m −2)
M = fuerza de flexión que actúa sobre el tejido conectivo medida en fuerza × distancia (N m)
y = distancia perpendicular al eje neutro (m)
I = área momento de inercia de la sección transversal del tejido conectivo en unidades de longitud a la cuarta potencia (m 4)
El momento de inercia es una cantidad que se basa en la forma de la sección transversal del miembro y se utiliza para caracterizar la capacidad del miembro para resistir la flexión.
La tensión de flexión es un poco más complicada que la tensión de tracción porque la tensión en el miembro no es constante a través de su sección transversal. Las fibras más alejadas del eje neutro de flexión experimentarán un mayor estrés, lo que en realidad puede mejorar la disociación.
Uno de los desafíos al describir matemáticamente el fracaso de los materiales vegetales es la amplia variabilidad que puede ocurrir. La fuerza del tejido conectivo se ve afectada por tres factores principales basados en las propiedades biológicas de la planta. El primer factor es el tamaño de la planta. Algunas plantas dentro de un solo cultivo pueden crecer más grandes que otras y pueden tener más tejido conectivo entre el tallo y el grano. Esto correspondería a mayor área y momento de inercia en las Ecuaciones 3.3.7 y 3.3.8, lo que requeriría más fuerza para alcanzar la tensión final.
El segundo factor que afecta a la fuerza del tejido conectivo es la madurez vegetal. La mayoría de las plantas perderán sus granos de forma natural cuando alcancen la madurez como mecanismo de propagación. Matemáticamente, esta disociación natural se describe por una reducción en el límite elástico del tejido conectivo. Muy a menudo, este estado de madurez natural corresponde con el tiempo óptimo para la cosecha del grano; sin embargo, no siempre es posible cosechar en ese momento exacto. Por lo tanto, la resistencia a la falla podría variar significativamente en función del tiempo real de cosecha.
El tercer factor que afecta la resistencia del tejido conectivo es el contenido de humedad. Las propiedades de resistencia del material vegetal varían mucho con el contenido de humedad. Los ingenieros necesitan comprender una serie de propiedades biológicas de la planta ya que se ven afectadas por el contenido de humedad. Por ejemplo, la presión de turgencia en una planta es la presión ejercida sobre las paredes de las celdas dentro de la planta por la humedad en las celdas. A medida que disminuye la presión de turgencia, lo que es causado por una reducción en el contenido de humedad, las plantas se vuelven menos rígidas. En algunas plantas, esto podría debilitar la estructura de la planta, facilitando la disociación, pero en otras podría dificultar la disociación de un grano porque el material vegetal sería más elástico. Dependiendo de las condiciones climáticas y de la intensidad solar, la presión de la turgencia puede variar mucho a lo largo de un solo día, afectando la disociación del cultivo.
Complicando aún más la representación matemática de la fuerza de la planta es el hecho de que puede haber una variabilidad significativa del tamaño de la planta, madurez y contenido de humedad entre diferentes regiones de un campo, entre diferentes plantas e incluso entre diferentes granos en una sola planta. Los ingenieros necesitan desarrollar mecanismos que se adapten a esta variabilidad y brinden a los operadores de la máquina la flexibilidad para adaptar la máquina a las diversas condiciones.
Separación
Una vez que los granos se disocian de la planta, deben separarse del resto del material vegetal y cualquier otro material indeseable. Este material indeseable se denomina material distinto del grano (MOG). El rendimiento de separación de una máquina cosechadora se cuantifica por la pérdida de separación (L s), que es la cantidad de grano libre que no se puede separar de la MOG expresada como porcentaje de la cantidad total de grano que fue disociado de las plantas por la máquina.
Hay dos principios principales que se suelen utilizar para separar el grano del MOG. El primero es la separación mecánica mediante tamizado. Un tamiz es simplemente una barrera con orificios de un tamaño correcto que permite que las partículas deseadas pasen a través mientras evita que las partículas más grandes pasen, o viceversa, permiten que pasen partículas indeseables más pequeñas mientras retienen las partículas deseadas. Algunos mecanismos de tamizado de granos dependen de las fuerzas gravitacionales sobre las partículas para hacer que pasen hacia abajo a través de las aberturas del tamiz; otros utilizan fuerzas centrípetas de mecanismos giratorios para forzar las partículas hacia afuera a través de los tamices. La mayoría de los mecanismos de tamizado gravitacional inducen un movimiento de sacudida o rebote sobre el material para mejorar el proceso de separación al facilitar el movimiento de las partículas hacia abajo a través de la estera de material, así como causar el movimiento del material a través del tamiz.
Considere la placa de tamiz conectada a las barras giratorias paralelas como se muestra en la Figura 3.3.3. Este es un mecanismo clásico de varillaje de cuatro barras. La placa de tamiz se mueve en un patrón circular manteniendo su orientación horizontal. Si el diseño de la longitud de los brazos giratorios junto con la velocidad de rotación es correcto, el material rebota lateralmente a través de la placa. A medida que rebota, los granos se mueven hacia abajo a través de la estera de material, luego a través de agujeros del tamaño apropiado en la placa. El MOG viaja a través de la placa y se deposita fuera del extremo del tamiz.
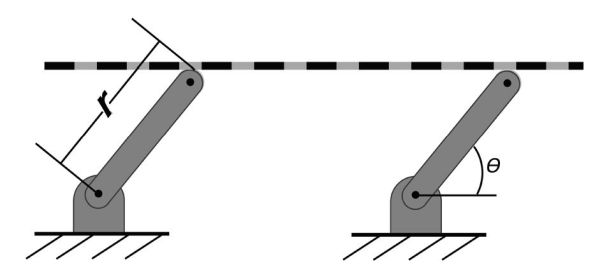
La velocidad de la placa de tamiz (v) se puede calcular a partir de la siguiente ecuación:
\[ v = r\omega \]
donde v = velocidad de la placa de tamiz (m s −1)
r = longitud del soporte giratorio, o brazos de conexión (m)
ω = velocidad de rotación de los brazos (radianes s −1)
La velocidad de la placa de tamiz es en realidad la velocidad tangencial de los brazos de soporte giratorios. La dirección de esta velocidad cambia sinusoidalmente a medida que las barras giran. Los componentes vertical (v v) y horizontal (v h) de la velocidad se pueden describir con las siguientes ecuaciones:
\[ v_{v} = v\ cos\theta \]
donde θ = la posición angular de los brazos.
El movimiento de rebote de una partícula se analiza considerando el momento de la partícula en relación con la placa que se mueve hacia arriba, pero desacelerando, para determinar si y cuándo la partícula saldrá de la placa.
El segundo principio que se utiliza para separar granos de MOG es la separación aerodinámica. Muy a menudo, las partículas de grano son más densas y tienen propiedades aerodinámicas significativamente diferentes a las del MOG, especialmente las partículas de hoja y casco más claras. Estas diferencias se explotan para separar el MOG del grano.
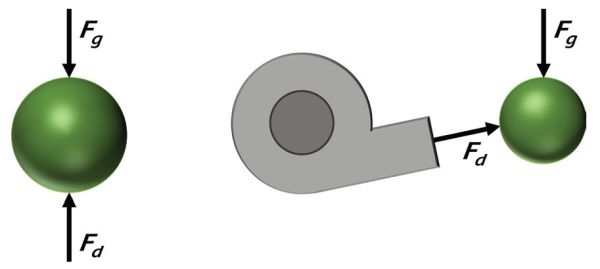
Una partícula que se mueve a través de cualquier fluido, incluido el aire, se somete a la gravedad y a las fuerzas de arrastre (Figura 3.3.4). La gravedad actúa hacia abajo sobre la partícula y produce la fuerza representada por:
\[ F_{g} = mg \]
donde F g = fuerza gravitacional (N, o m kg s −2)
m = masa de la partícula (kg)
g = constante gravitacional en unidades de longitud por unidad de tiempo al cuadrado (9.81 m s −2)
La fuerza de arrastre actúa en la dirección opuesta al movimiento de la partícula en relación con el aire. La fuerza de arrastre se calcula por:
\[ F_{d} = 0.5\rho_{air}v^{2}_{part}C_{d}A_{part} \]
donde F d = fuerza de arrastre (N, o m kg s −2)
ρ aire = densidad del aire en unidades de masa por unidad de volumen (kg m −3)
v part = velocidad de la partícula con respecto al aire en unidades de longitud por tiempo (m s −1)
C d = coeficiente de arrastre sin unidad de la partícula
Una parte = área característica de la partícula (m 2).
El movimiento de la partícula está determinado por la suma vectorial de las dos fuerzas y la ecuación de movimiento fundamental:
\[ a = \frac{F_{r}}{m} \]
donde a = aceleración de la partícula en la dirección de la fuerza resultante (m s −2)
F r = fuerza resultante sobre la partícula (N, o m kg s −2)
La trayectoria de la partícula se puede describir matemáticamente integrando la ecuación de aceleración una vez para obtener la ecuación de velocidad, luego una segunda vez para encontrar la posición en función del tiempo.
El coeficiente de arrastre es una función de muchos factores de partículas, incluyendo su forma y textura superficial. Muchas partículas MOG, como las cáscaras de semillas y las partículas de tallo, tienen una forma y textura superficial más irregulares que los granos y, por lo tanto, tendrán un coeficiente de arrastre más alto. La separación aerodinámica se produce al capitalizar estas diferencias de arrastre así como las diferencias de masa entre el grano y las partículas MOG. Las partículas se pueden separar si una corriente de aire se dirige a través de la estera de grano y MOG de tal manera que el MOG se dirige en una trayectoria diferente a la de los granos.
Considere una corriente de aire creada por un ventilador que sopla directamente hacia arriba en una partícula que cae. Si la velocidad del aire se incrementa hasta el punto en que la fuerza de arrastre es igual a la fuerza de gravedad, la partícula quedará suspendida en la corriente de aire. La velocidad del aire en este punto es, por definición, la velocidad terminal de la partícula. Si aumenta la velocidad del aire, la partícula se moverá hacia arriba; si disminuye la velocidad del aire, la partícula se moverá hacia abajo.
Considera que una mezcla de partículas de grano y MOG se deja caer a través de una corriente de aire dirigida como se ilustra en la Figura 3.3.4. Si la velocidad del aire se establece ligeramente por debajo de la velocidad terminal de los granos, su trayectoria se alterará un poco hacia la derecha, pero continuarán moviéndose hacia abajo. Las partículas MOG que tienen una fuerza de arrastre mucho mayor y una velocidad terminal correspondientemente menor serán transportadas más hacia arriba y hacia la derecha por la corriente de aire que las mueve fuera del flujo de grano.
Transporte
Una vez que el grano está disociado y separado del MOG, debe ser transportado a una estación receptora. Esto generalmente se logra en varias etapas o etapas usando una variedad de mecanismos. Se utilizan diversos tipos de transportadores para mover el grano de una parte de una máquina a otra o de una máquina a otra. En diferentes etapas del proceso, el grano puede almacenarse o transportarse en varios contenedores a granel.
Los principios involucrados en el diseño o análisis de contenedores de almacenamiento o transporte a granel son principalmente la resistencia de los materiales. El diseñador primero necesita determinar qué fuerzas se producirán en la estructura por el grano. Se analizan diagramas de cuerpo libre para determinar la magnitud y dirección de todas las fuerzas. Un desafío en el diseño de maquinaria para cosechar granos es que las máquinas suelen ser móviles. A medida que las máquinas se mueven a través del terreno accidentado que normalmente se encuentra en campos agrícolas, se inducen fuerzas dinámicas a medida que rebota la carga de grano Los diseñadores suelen utilizar una variedad de técnicas para predecir las cargas dinámicas máximas que podrían inducirse en una estructura.
Una vez conocidas las fuerzas, el diseñador determina entonces qué tensiones son inducidas en cada miembro estructural por la carga de grano. La tensión (σ) describe la cantidad de fuerza (F) que se transporta por unidad de área (A) de un miembro estructural dado:
\[ \sigma = \frac{F}{A} \]
donde σ = esfuerzo en unidades de fuerza por unidad de área (N m −2)
F = fuerza en el miembro (N)
A = área característica del miembro (m 2)
El esfuerzo en cualquier parte de un miembro estructural no puede exceder el límite elástico del material o se incurrirá en daños permanentes (deformación). Pero incluso si no se induce una deformación permanente en un miembro estructural, los ingenieros aún deben preocuparse por cuánto se flexiona o desvía un miembro estructural. La deflexión en un miembro se calcula a partir de la deformación, que es:
\[ \epsilon = \frac{dL}{L} = \frac{\sigma}{E} \]
donde ε = deformación (adimensional)
L = longitud del miembro (m)
E = módulo de elasticidad reportado en fuerza por unidad de área (N m −2)
La tensión y la deformación están relacionadas por el módulo de elasticidad, también conocido como módulo de Young. Cuanto menor sea el módulo de elasticidad, más deflexión causará una fuerza dada en un miembro. Alguna desviación puede ser buena en una estructura, especialmente cuando están involucradas fuerzas dinámicas, porque ayuda a absorber energía sin causar altas cargas pico. En el caso de una máquina que se mueve a través de un campo accidentado, por ejemplo, alguna desviación en la estructura puede absorber parte de la energía causada por el terreno irregular y evitar fallas estructurales.
Para el transporte de menor distancia, se pueden emplear varios dispositivos de transporte diferentes. Al diseñar dispositivos de transporte, el diseñador se preocupa principalmente por la capacidad del dispositivo y la potencia requerida para transportar el material. Algunos de los dispositivos de transporte más simples utilizan paletas o cubos conectados a cadenas (Figura 3.3.5) para arrastrar o transportar el grano. La capacidad de los transportadores de paletas, que es el caudal de material a través del transportador, se calcula simplemente por la cantidad de material transportado por cada paleta y el número de paletas que pasan un punto en una cantidad de tiempo determinada:
\[ Q_{a} = Vn \]
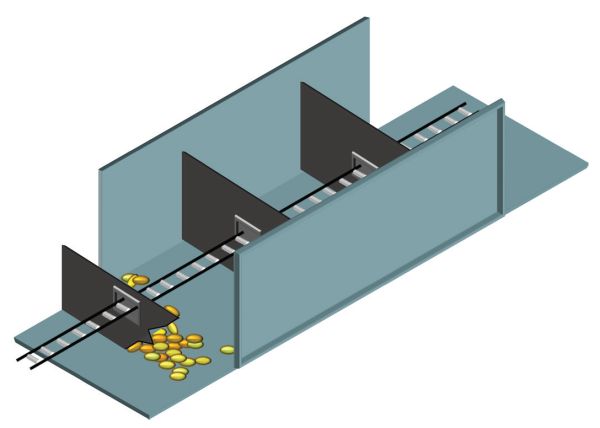
donde Q a = caudal real en volumen por unidad de tiempo (m 3 s −1)
V = volumen de material transportado por una sola paleta (m 3)
n = número de paletas que se descargan por unidad de tiempo (s −1)
El volumen de material que puede ser transportado por las paletas se ve afectado por una serie de parámetros. Las propiedades del grano como la forma de las partículas, el tamaño, la fricción superficial y el contenido de humedad afectan la forma de la pila de grano en cada paleta. La pendiente del transportador limita el tamaño de las pilas antes de que el grano pase sobre la parte superior de la paleta y vuelva a bajar por el transportador.
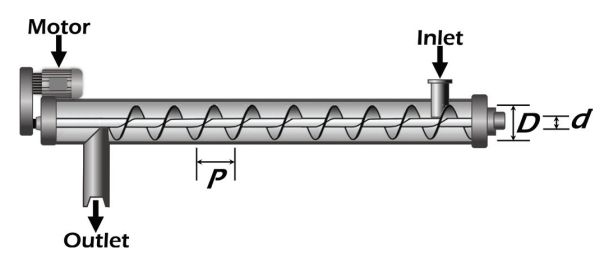
Otro dispositivo de transporte comúnmente utilizado en la cosecha y manejo de granos es un transportador de tornillo, comúnmente conocido como barrena (Figura 3.3.6). Los transportadores de tornillo utilizan una placa helicoidal continua, llamada vuelo, unida a un eje giratorio. La capacidad de un transportador de tornillo horizontal que está completamente lleno de grano es el volumen desplazado por una sola rotación del eje multiplicado por el número de rotaciones en una unidad de tiempo dada, que puede calcularse mediante:
\[ Q_{t}=\frac{\pi}{4} (D^{2}-d^{2})P\omega \]
donde Q t = caudal teórico en volumen por unidad de tiempo (m 3 s −1)
D = diámetro exterior del vuelo (m)
d = diámetro del eje (m)
P = longitud de paso del vuelo (m)
ω = velocidad de rotación del eje (radianes s −1)
Cuando el transportador está inclinado, el vuelo ya no estará lleno ya que el grano tenderá a deslizarse hacia abajo alrededor del vuelo. El caudal volumétrico real (Q a) puede calcularse mediante:
\[ Q_{a}= Q_{t} \eta_{v} \]
donde η v es la eficiencia volumétrica del transportador. Predecir la eficiencia volumétrica puede ser muy difícil porque se ve afectada por numerosos factores, incluyendo la pendiente del transportador, la velocidad de rotación, el contenido de humedad del grano, el tamaño de partícula, la fricción de partícula a transportador y la fricción de partícula a partícula. Debido a esta complejidad, la predicción matemática generalmente se logra con relaciones empíricas.
La potencia requerida para transportar el material se ve afectada por las fuerzas gravitacionales y de fricción. Si el grano se levanta a cualquier distancia vertical, el transportador debe superar la fuerza gravitacional que se opone a ese levantamiento. La potencia se define como una fuerza aplicada sobre una distancia dada en una cantidad de tiempo determinada (fuerza × distancia/tiempo). Los componentes de fuerza y tiempo del cálculo de la potencia gravitacional provienen del caudal del grano a través del transportador expresado en unidades de peso por unidad de tiempo. La densidad del grano se puede utilizar para convertir el caudal volumétrico en un caudal ponderal. El componente de distancia de potencia es simplemente la distancia vertical en la que se levanta el grano. El componente gravimétrico de la potencia es:
\[ P_{q} = Q_{a}\rho_{grain}h \]
donde P g = potencia requerida para superar la gravedad (W o J/s)
Q a = caudal volumétrico real del grano (m 3 s −1)
ρ grano = densidad del grano (kg m −3)
h = altura a la que se levanta el material (m).
El componente de fricción de la potencia puede ser más complicado de calcular. En el caso de un transportador de paletas, el grano debe deslizarse a lo largo de la parte inferior de la superficie del transportador. Esta fuerza de fricción a veces se puede predecir bastante bien a partir del coeficiente de fricción entre los granos y la superficie del transportador. Si ese coeficiente de fricción es demasiado grande, las fuerzas debidas a la fricción en los granos en la interfaz entre la pila de granos y la superficie del transportador harán que los granos dentro de la pila comiencen a moverse uno con relación al otro. En este punto, se hace más difícil describir matemáticamente la energía necesaria para superar estas fuerzas de fricción internas así como la fricción superficial.
Las fuerzas de fricción en los transportadores de tornillo son similares. El grano en un transportador horizontal completo se desliza a lo largo de la pared exterior del tubo transportador así como el vuelo, pero no se mueve tanto dentro de la masa de grano. A medida que el transportador está inclinado y ya no está completamente lleno, la cantidad de movimiento dentro de la masa de grano aumenta y se vuelve más crítica para la evaluación.
Aplicaciones
La máquina más común utilizada para la cosecha de granos es la cosechadora moderna de granos (Figura 3.3.1). Las cosechadoras suelen tener un accesorio intercambiable en el frente llamado encabezado que engancha el cultivo y pasa ciertas fracciones de esa planta a la cosechadora. Luego, el material pasa a través de un mecanismo de trilla que disocia los granos de los tallos de la planta y también realiza cierta separación de grano de MOG. Luego, el grano y MOG se pasan a través de diversos mecanismos de separación y limpieza. El MOG generalmente se pasa longitudinalmente a través de la máquina y se expulsa por la parte posterior. El grano limpio generalmente se mueve hacia abajo a través de la máquina hasta un depósito de captura en la parte inferior. A partir de ahí, se mueve hacia arriba con transportadores de paletas y/o tornillo a un tanque de retención en la parte superior de la máquina. Luego se usa un transportador de tornillo grande para vaciar periódicamente el contenido del tanque de retención en un camión u otro vehículo, que transporta el grano a una estación receptora.
Compromiso
Los accesorios de cabecera se utilizan para enganchar el cultivo. Los dos tipos más comunes de accesorios de cabecera en las cosechadoras de grano son la mesa de grano y la cabeza de maíz o fila. Las tablas de granos (Figura 3.3.1) se utilizan típicamente en cultivos de granos pequeños como el trigo y la soya. Por lo general, incluyen un gran carrete de recolección para enganchar el cultivo y tirar de él hacia el encabezado. Un mecanismo de corte, típicamente una barra de hoz, corta la planta a medida que se introduce en el cabezal para obtener el control mecánico del grano. Dado que las mesas de grano pueden tener 12 m de ancho o más, los transportadores transversales mueven el material de cultivo desde los extremos del cabezal hasta el centro donde se alimenta a la cosechadora.
La altura del corte depende del cultivo y de la práctica cultural de la operación. Los procesos de trilla y separación en la cosechadora son más eficientes cuando se minimiza el MOG que ingresa a la cosechadora. En la soya, por ejemplo, las vainas de semillas pueden crecer muy bajas en el tallo de la planta; por lo tanto, el cultivo debe cortarse cerca del suelo para evitar pérdidas. En cultivos como el trigo donde los granos crecen en una cabeza en la parte superior del tallo de la planta, la altura de corte podría ser lo suficientemente baja como para capturar toda la cabeza pero minimizar la cantidad de MOG que pasa a la máquina. En algunos sistemas de producción, sin embargo, el MOG podría ser utilizado para camas de animales o bioenergía. En estos casos, el cabezal se opera más bajo para que se recoja más MOG, se pasa a través de la cosechadora y se deposita en una línea estrecha, llamada hilera, detrás de la cosechadora. La hilerera puede ser recolectada fácilmente por otra máquina cosechadora de biomasa en una operación separada. Ocasionalmente, el MOG es recogido por otra máquina, como una empacadora, unida directamente a la cosechadora (Figura 3.3.7).
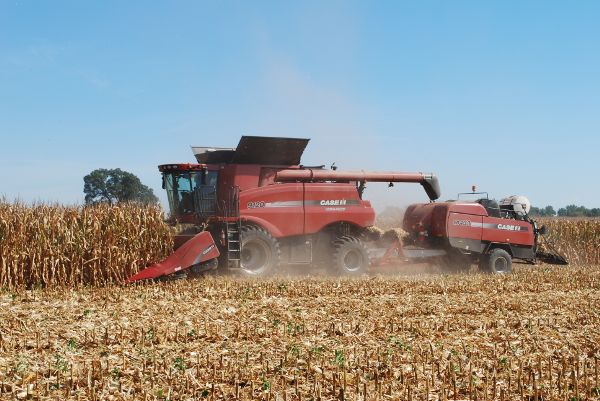
En el maíz (maíz), los granos se producen hacia la mitad de la planta. Cortar la planta para capturar las mazorcas para trillar significaría la introducción de grandes cantidades de MOG en la corriente de cosecha, dificultando el desempeño de trilla y separación. Dado que el maíz se cultiva típicamente en hileras espaciadas 0.5—0.75 m, las cabezas de maíz se construyen con dedos que pasan entre las hileras para que cada fila de maíz se pueda enganchar individualmente (Figura 3.3.8). Rodillos largos y paralelos a cada lado de la fila agarran los tallos de las plantas debajo de la oreja y los tiran hacia abajo a medida que la máquina avanza. Las placas decapadoras por encima de cada rodillo están espaciadas de tal manera que las plantas pasan entre ellas, pero las mazorcas de maíz no lo hacen. A medida que las plantas son arrastradas hacia abajo, las orejas son despojadas de las plantas. Idealmente, todo el material vegetal se tira hacia abajo a través del cabezal y no pasa a la cosechadora. Dependiendo de la condición del tallo, se producirá alguna rotura del tallo y remoción de hojas, y ese MOG tendrá que ser separado en la cosechadora. Las cadenas con los dedos por encima de cada placa decapadora mueven las orejas y MOG de nuevo al cabezal. Luego, los transportadores cruzados mueven el material desde el borde del cabezal hacia el centro donde se alimenta a la cosechadora.
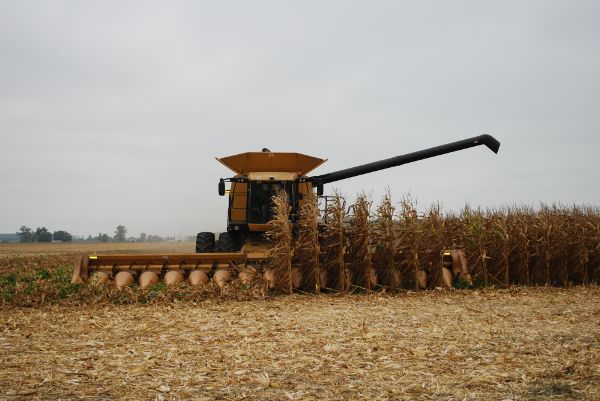
Una de las medidas de desempeño de cualquier encabezado es su efectividad en la recolección de todo el grano del campo en la cosechadora. Este proceso de compromiso se complica por el hecho de que los granos tienden a caerse naturalmente de las plantas más fácilmente cuando el cultivo se encuentra en sus óptimas condiciones de cosecha. Las pérdidas por el encabezado se denominan pérdidas por rotura (L sh). Se cuantifican como porcentaje del rendimiento potencial (y p), es decir, el rendimiento disponible de las plantas.
Las pérdidas por rotura se ven afectadas por las condiciones del cultivo, incluida la madurez y el contenido de humedad. También se ven afectados por el diseño y operación de la cabecera. Por ejemplo, la velocidad del carrete de recolección en las mesas de grano debe coincidir con la velocidad de avance de la máquina. Si la velocidad del carrete es demasiado alta, las plantas son golpeadas agresivamente, lo que hace que los granos se caigan de las plantas antes de que puedan ser capturados en la plataforma de cabecera. Si la velocidad del carrete es demasiado lenta, las plantas podrían ser empujadas hacia adelante, volcando nuevamente los granos al suelo antes de que entren al cabezal. Dependiendo de las condiciones del cultivo, la velocidad tangencial del carrete generalmente se opera al menos 25-50% más rápido que la velocidad de avance de la cosechadora para tirar de las plantas hacia el cabezal. Algunas máquinas utilizan sensores y controles electrónicos para ajustar automáticamente la velocidad del carrete para que coincida con la velocidad de avance de la máquina.
Disociación
La función de disociación en las cosechadoras generalmente se logra mediante cilindros giratorios llamados cilindros trilladores. Existen dos configuraciones básicas de cilindros trilladores, que se distinguen por la dirección en que el material se mueve a través del cilindro. Algunos cilindros están montados con su eje de rotación horizontal y perpendicular al eje longitudinal de la máquina. El material entra por un lado del cilindro y sale por el otro (Figura 3.3.9). Barras orientadas a lo largo del exterior del cilindro frotan el material vegetal contra la carcasa estacionaria alrededor del exterior del cilindro, que se llama cóncavo. La acción de frotamiento afecta la disociación del grano de las plantas. Los agujeros en el cóncavo facilitan una acción de tamizado para separar parte del grano del material vegetal más largo.
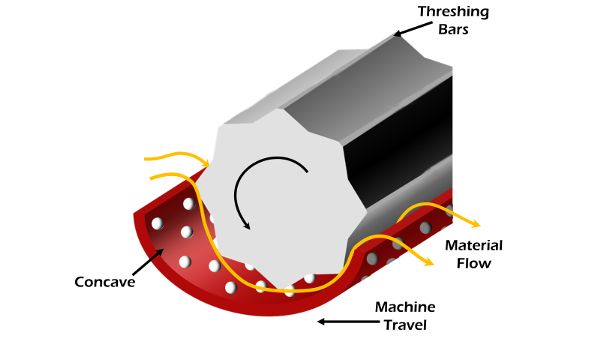
La otra configuración de trilla común tiene el cilindro de trilla giratorio montado paralelo al eje longitudinal de la máquina. El material ingresa al extremo del cilindro y se mueve en un patrón helicoidal alrededor y más allá del cilindro (Figura 3.3.10). Estructuras cóncavas similares alrededor del cilindro proporcionan resistencia al flujo para inducir las funciones de disociación y separación.
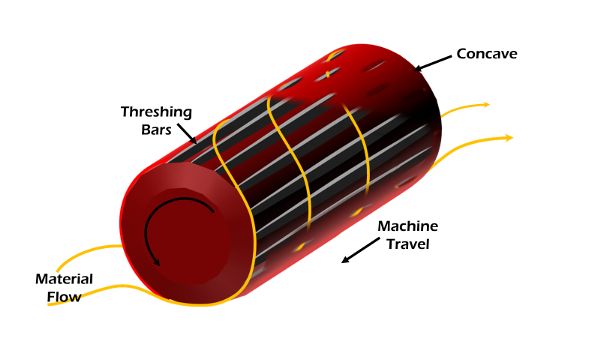
La efectividad de trilla se mide por el porcentaje de granos que se disocian de las plantas, el porcentaje de granos que se dañan durante el proceso de trilla y la cantidad de ruptura de MOG. Las cantidades excesivas de partículas pequeñas de MOG pueden dificultar la eficiencia de la separación, ya que pueden ser indistinguibles de los granos en el proceso de separación. La eficiencia de trilla y el daño del grano se ven afectados por las propiedades de la planta, el diseño del cilindro y cóncavas, y los ajustes operativos. Los operadores de máquinas a menudo tienen control en tiempo real de la velocidad del cilindro, así como la holgura entre el cilindro y la cóncava.
Separación
Hay dos tipos diferentes de sistemas de separación utilizados en las cosechadoras de granos que generalmente están asociados con los dos tipos de dispositivos de trilla. Los cilindros de trilla orientados lateralmente generalmente alimentan la corriente de material sobre una plataforma separadora vibratoria comúnmente llamada andador de paja. La placa oscilante es esencialmente un tamiz que permite que las partículas más pequeñas, incluidos los granos, caigan a través del tamiz a medida que el MOG se mueve hacia atrás a través de la máquina.
En cosechadoras con cilindros trilladores orientados axialmente, esta última porción del cilindro y cóncava logran la separación inicial. Estos separadores rotativos utilizan fuerzas centrípetas para separar los granos hacia afuera a través de aberturas cóncavas.
Independientemente de la configuración inicial del separador, la mayoría de las cosechadoras pasan la corriente de grano capturada de la unidad trilladora y la unidad de separación inicial a través de un tamiz de limpieza adicional de varias etapas También se aplica separación neumática en estos tamices para mejorar la separación de grano de MOG.
Transporte
La corriente de grano limpio se transporta desde la parte inferior de la cosechadora a un tanque de retención en la parte superior de la máquina usando una combinación de paletas y transportadores de tornillo. Los tanques de retención varían en tamaño con el tamaño de la máquina. Dependiendo del cultivo y las condiciones de operación, el tanque combinado podría llenarse en tan solo 3—4 minutos. En algunas operaciones, la cosechadora es conducida al borde del campo cuando el tanque está lleno para que pueda vaciarse en un camión para su transporte a una estación receptora. Esto a menudo se considera un uso ineficiente de una máquina cosechadora muy costosa. La productividad de la operación de recolección se maximiza si la cosechadora se puede operar lo más cerca posible de manera continua.
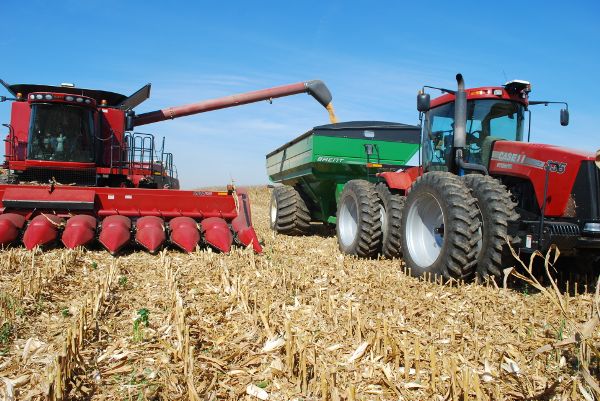
Las cosechadoras pueden descargarse mientras cosechan si se puede conducir un vehículo receptor junto a la cosechadora. Por lo general, los camiones de carretera no se utilizan para esta operación debido a sus llantas relativamente pequeñas. La tracción en condiciones de suelo potencialmente blando limita su movilidad. También, existe una preocupación con respecto a la compactación del suelo en el campo. Las cargas pesadas en llantas pequeñas compactarán el suelo debajo de las llantas causando daños que afectarán el rendimiento de futuros cultivos en el campo.
El transporte de grano en campo a menudo se realiza con un carro de granos (Figura 3.3.11). Los carros de grano son grandes tanques de transporte típicamente tirados por tractores agrícolas grandes. Tanto el carro como el tractor estarán equipados con llantas grandes u orugas para reducir la presión sobre el suelo.
Con el uso de carros de grano, surge un desafío logístico en torno a la mejor manera de alejar el grano de la cosechadora para mantenerlo cosechando. Muchas operaciones utilizan múltiples cosechadoras en un campo simultáneamente. Los gerentes deben decidir cuántos carros de grano se necesitan, qué tan grandes deben ser esos carros y cuántos camiones se necesitan para sacar el grano del campo. Operacionalmente, la programación de vehículos es un desafío de anticipar que las cosechadoras en una flota de cosechadoras múltiples deben vaciarse para que no se llenen y se vuelvan improductivas.
Ejemplos
Ejemplo\(\PageIndex{1}\)
Ejemplo 1: Combinar eficiencia de cosecha
Problema:
Una forma de evaluar la eficiencia de cosecha de una cosechadora es medir las pérdidas que ocurren a medida que una cosechadora se mueve por el campo. Esto se puede hacer reuniendo y contando físicamente o pesando los granos que se encuentran en diferentes ubicaciones en el espacio de operación de la cosechadora.
Considera la cosechadora en la Figura 3.3.12 que se detuvo al cosechar un cultivo muy uniforme de trigo. Las mediciones de campo se tomaron en tres ubicaciones diferentes como se muestra. En cada punto se seleccionó un área cuadrada de 1 m como área de prueba representativa. En el punto A frente a la cosechadora, todas las plantas en pie en el área de prueba se cortaron cuidadosamente y se cosecharon a mano para determinar la cantidad de grano disponible en el campo. Después de eso, se recolectaron y pesaron los granos que estaban depositados en el suelo en esa zona de prueba. En el punto B, se recolectaron y pesaron todos los granos encontrados dentro del área de prueba. En el punto C, que está más allá de la trayectoria de descarga del material que se expulsa del dorso de la cosechadora cuando se detuvo, todos los granos fueron recolectados y pesados por separado por los que aún estaban adheridos a las plantas y los que estaban libres. Los siguientes son los datos recopilados en cada ubicación.
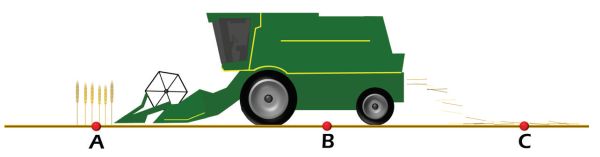
- Punto A:
- 335 g de grano no cosechado
- 15 g de granos libres (granos tendidos en el suelo)
- Punto B:
- 40 g de grano libre
- Punto C:
- 63 g de grano libre
- 14 g de grano adherido a la planta
Determinar las eficiencias de recolección, trilla y separación de esta operación de cosecha.
Solución
El rendimiento teórico o potencial, y p, del cultivo es el grano cosechable que aún se adhiere a las plantas cuando la cosechadora lo engancha. En este ejemplo, el rendimiento potencial se basa en la semilla no cosechada en el punto A.
\( y_{p} = \frac{0.335 \text{ kg}}{\text{m}^{2}} \cdot \frac{10000 \text{ m}^{2}}{ \text{ha}} = \frac{3350 \text{ kg}}{\text{ha}} = \frac{3.35 \ T}{\text{ha}} \)
Se puede realizar una conversión de unidad simple para convertir el rendimiento métrico en unidades de rendimiento comunes de EE. UU. de bu/acre como:
\( y_{p} = \frac{3350 \text{ kg}}{\text{ha}} \cdot \frac{1 \text{ bu}}{27.22 \text{ kg}} \cdot \frac{1 \text{ ha}}{ 2.47\text{ acre}} = \frac{49.8 \text{ bu}}{\text{ha}} \)
Tenga en cuenta que el cálculo del rendimiento potencial no considera los granos que habían caído de las plantas antes de que la máquina los activara. En este ejemplo, la pérdida de rendimiento pre-cosecha, y ph, fue:
\( y_{ph} = \frac{0.015 \text{ kg}}{\text{m}^{2}} \cdot \frac{10000 \text{ m}^{2}}{\text{ ha}} = \frac{150 \text{ kg}}{\text{ha}} \)
Como porcentaje del grano total disponible, la pérdida de rendimiento previo a la cosecha fue:
\( L_{ph} = \frac{150}{3350 + 150} \cdot 100 = 4.3 \text{%} \)
El grano que se recolectó en el punto B debajo de la cosechadora incluye las pérdidas por rotura así como las pérdidas previas a la cosecha. Las pérdidas previas a la cosecha se restan del grano total en el punto B para determinar la pérdida de grano cuando la cabecera se involucró con el cultivo. La pérdida por rotura, L sh, se calcula como porcentaje del rendimiento teórico de la siguiente manera:
\( L_{sh} = \frac{(40 \text{ g}-15 \text{ g})}{335 \text{ g}} \cdot 100 = 7.5 \text{%} \)
La pérdida por trilla es una cuantificación de los granos que no se disociaron de la planta. Estos granos se encuentran en el punto C aún adheridos al material vegetal. El porcentaje de pérdida por trilla se basa en el grano total que realmente ingresa a la cosechadora. En este ejemplo, la pérdida por rotura se elimina del grano total disponible en el cálculo de la pérdida por trilla, L th, de la siguiente manera:
\( L_{th} = \frac{14 \text{ g}}{(335 \text{ g}-25 \text{ g})} \cdot 100 = 4.5 \text{%} \)
La pérdida de separación es el grano trillado que no se retira de la corriente MOG y se pierde por la parte posterior de la cosechadora. El grano libre recolectado en el punto C incluye la pérdida por separación, así como las pérdidas por rotura y rendimiento. Por lo tanto, la pérdida debida únicamente a la separación, L s, es:
\( L_{s} = \frac{(63 \text{ g} - 15 \text{ g} - 25 \text{ g})}{(335 \text{ g} - 25 \text{ g})} \cdot 100=7.4 \text{%} \)
La pérdida total de cosecha, L h, se basa en todo el grano perdido por la cosechadora, que sería:
\( L_{h} = \frac{63 \text{ g} + 24 \text{ g} - 15 \text{ g}}{335 \text{ g}} \cdot 100 = 19\text{%} \)
El rendimiento real cosechado, y a, entonces, es:
\( y_{a} = \frac{3.35 \ T}{\text{ha}}- \frac{0.19(3.35 \ T)}{\text{ha}} = \frac{2.71 \ T}{\text{ha}} \)
La eficiencia de cosecha es (Ecuación 3.3.6):
\( E_{h} = 1 -L_{h} = 1-0.19 = 0.81 \)
Esto se puede verificar mediante la Ecuación 3.3.4:
\( E_{h} = \frac{y_{a}}{y_{t}} = \frac{2.71 \ T}{\text{ha}} \cdot \frac{\text{ha}}{3.35 \ T} = 0.81 \)
El gerente prudente examinaría estos números de eficiencia de cosecha para determinar si se ameritan mejoras. Para la cosecha de trigo, estas pérdidas probablemente serían consideradas bastante grandes. El gerente puede considerar ajustes y/o cambios operativos a la cosechadora que podrían reducir las pérdidas de cosecha.
Ejemplo\(\PageIndex{2}\)
Ejemplo 2: Velocidad del carrete
Problema:
Una de las causas de la pérdida por rotura con las mesas de grano es la velocidad inadecuada del carrete. Los diseñadores de una mesa de grano necesitan proporcionar una amplia capacidad de ajuste en la velocidad de rotación del carrete para que el operador pueda compensar las condiciones de cosecha y la velocidad de avance. Específicamente, el diseñador necesita determinar el rango de velocidades que el diseño debe ser capaz de lograr. Considera la tabla de grano en la Figura 3.3.13 que tiene un carrete de 1.3 m de diámetro. Determine el rango de velocidades de carrete que el diseño debe ser capaz de lograr.
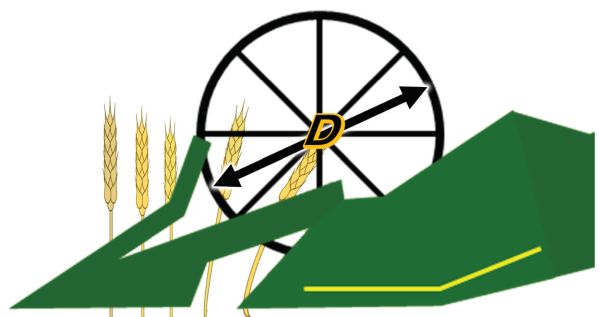
Solución
Como se mencionó anteriormente, la velocidad tangencial de los dispositivos de acoplamiento en el extremo del carrete debería ser típicamente 25— 50% mayor que la velocidad de avance de la cosechadora, v f. La norma ASAE D497.7 es un gran recurso para los parámetros operativos de la maquinaria agrícola común. El Cuadro 3.3.3 de esa norma (reimpreso en parte como Cuadro 3.3.2 de este capítulo) indica que la velocidad típica de avance de una cosechadora autopropulsada oscila entre 3.0 y 6.5 km/hr. La velocidad mínima de rotación del carrete se produciría con la velocidad tangencial del carrete 25% mayor que la velocidad de avance más lenta de 3.0 km/hr. Por el contrario, la velocidad máxima ocurriría al 150% de 6.5 km/hr. La velocidad tangencial, v t, se calcula utilizando la Ecuación 3.3.9:
Eficiencia de Campo | Velocidad de Campo | |||||
---|---|---|---|---|---|---|
Máquina Cosechadora | Rango% | % Típico | Rango mph | Típico mph | Rango km/h | Típico km/h |
Recolector de maíz desgranadora |
60—75 |
65 |
2.0—4.0 |
2.5 |
3.0—6.5 |
4.0 |
Combinar |
60—75 |
65 |
2.0—5.0 |
3.0 |
3.0—6.5 |
5.0 |
Combinar (SP) |
65—80 |
70 |
2.0—5.0 |
3.0 |
3.0—6.5 |
5.0 |
Segadora |
75—85 |
80 |
3.0—6.0 |
5.0 |
5.0—10.0 |
8.0 |
Segadora (rotativa) |
75—90 |
80 |
5.0—12.0 |
7.0 |
8.0—19.0 |
11.0 |
Segadora-acondicionador |
75—85 |
80 |
3.0—6.0 |
5.0 |
5.0—10.0 |
8.0 |
Segadora-acondicionador (rotativo) |
75—90 |
80 |
5.0—12.0 |
7.0 |
8.0—19.0 |
11.0 |
Hileradora (SP) |
70—85 |
80 |
3.0—8.0 |
5.0 |
5.0—13.0 |
8.0 |
Rastrillo de entrega lateral |
70—90 |
80 |
4,0-8,0 |
6.0 |
6.5—13.0 |
10.0 |
Empacadora rectangular |
60—85 |
75 |
2.5—6.0 |
4.0 |
4,0-10,0 |
6.5 |
Empacadora rectangular grande |
70—90 |
80 |
4,0-8,0 |
5.0 |
6.5—13.0 |
8.0 |
Empacadora redonda grande |
55—75 |
65 |
3.0—8.0 |
5.0 |
5.0—13.0 |
8.0 |
Cosechadora de forraje |
60—85 |
70 |
1.5—5.0 |
3.0 |
2.5—8.0 |
5.0 |
Cosechadora de forraje (SP) |
60—85 |
70 |
1.5—6.0 |
3.5 |
2.5—10.0 |
5.5 |
Cosechadora de remolacha azucarera |
50—70 |
60 |
4,0-6,0 |
5.0 |
6.5—10.0 |
8.0 |
Cosechadora de papa |
55—70 |
60 |
1.5—4.0 |
2.5 |
2.5—6.5 |
4.0 |
Recogedor de algodón (SP) |
60—75 |
70 |
2.0—4.0 |
3.0 |
3.0—6.0 |
4.5 |
\( v_{t} = r \omega \)
A la velocidad mínima de rotación, la velocidad tangencial debe ser:
\( v_{t} = v_{f}(1.25) \)
Combinando las ecuaciones, la velocidad mínima de rotación es:
\( \omega = \frac{v_{t}}{r} = \frac{v_{f}(1.25)}{r} = \frac{3 \text{ km}}{\text{hr}} \cdot \frac{1.25}{1} \cdot \frac{2}{1.3 \ m} \cdot \frac{1000 \ m}{\text{km}} \cdot \frac{1 \text{hr}}{60 \text{ mins}} \cdot \frac{1 \text{hr}}{2\pi} = 15.4 \ \text{rpm} \)
Se deduce, entonces, que la velocidad máxima de rotación es:
\( \omega =\frac{v_{t}}{r}=\frac{6 \text{ km}}{\text{ hr}}\cdot \frac{1.5}{1} \cdot \frac{2}{1.3 \ m} \cdot \frac{1000 \ m}{\text{km}}\cdot \frac{1 \ hr}{60 \text{ min}} \cdot \frac{1 \text{ rev}}{2\pi} = 36.7 \ rmp \)
Las unidades de revolución se suman a los cálculos señalando que los radianes se consideran sin unidades, y hay 2π radianes en una revolución completa. La conclusión es que el sistema de accionamiento para el carrete en esa mesa de grano debe ser capaz de alcanzar velocidades que varían de 15.4 a 36.7 rpm, por lo que el mecanismo de accionamiento para el carrete debe diseñarse en consecuencia.
Ejemplo\(\PageIndex{3}\)
Ejemplo 3: Cargas por eje
Problema:
El diseño de la estructura de un vehículo se basa en gran medida en comprender los efectos de todas las fuerzas en la máquina. Considere un carro de grano de dos ruedas tirado por un tractor como se muestra en la Figura 3.3.14. La tarea es calcular el tamaño requerido (diámetro) de los ejes cilíndricos para soportar el conjunto de la rueda del carro. Supongamos que la carga de grano se distribuye uniformemente en el tanque del carro y que el tanque es lateralmente simétrico, lo que significa que las cargas se distribuyen uniformemente entre las ruedas izquierda y derecha del carro. Además de las dimensiones que se muestran en la Figura 3.3.15, un fabricante da los siguientes datos para un carro muy similar:
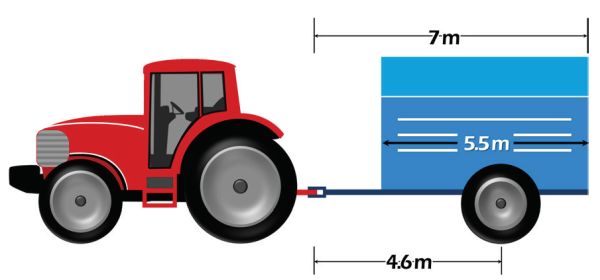
- Capacidad del carro: 850 bushels de maíz (maíz)
- Peso del carrito vacío: 54 kN
- Peso de la lengüeta del carrito vacío: 11 kN
Solución
Debido a la simetría izquierda/derecha del carro, el análisis de cuerpo libre se puede realizar en dos dimensiones mirando al costado de la máquina (Figura 3.3.15). Las dos ruedas del carro tendrán cargas idénticas. Dado que el tractor soporta 11 kN del peso del carro vacío desde la lengüeta en el punto de enganche (F ct), el resto del peso del carro vacío, que es de 54 kN — 11 kN = 43 kN, debe ser soportado por las ruedas del carro (F cw). Dadas las suposiciones de simetría y carga uniforme, el centro de gravedad de la carga de grano estará en el centro geométrico del contenedor en el carro. La distancia desde el punto de enganche hasta el centro de gravedad del grano, x g, es:
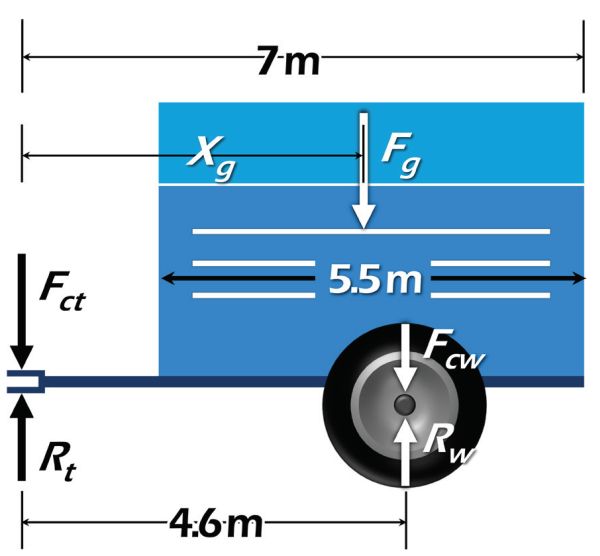
\( x_{g}= 7 - \frac{5.5}{2}=4.25 \ m\)
El peso del grano es:
\( F_{g}=\frac{850 \text{ bu}}{1} \cdot \frac{25.4 \text{ kg}}{\text{bu}} \cdot \frac{9.81 \text{ N}}{\text{ kg}} = 212 \text{ kN} \)
El carro y el grano deben ser soportados por las ruedas del carro y por el tractor en el punto de enganche. Estas fuerzas se representan como fuerzas de reacción Rw y Rt (Figura 3.3.15). R w es el peso total que deben soportar las ruedas y los ejes del carro, que se puede calcular sumando los momentos sobre el punto de enganche entre el carro y el tractor. Si la rotación en sentido antihorario es positiva, esa ecuación de momento es:
\( R_{w}(4.6) - F_{cw}(4.6) - F_{g}(4.25) + F_{ct}(0)-R_{t}(0) = 0 \)
Tenga en cuenta que debido a que la carga de la lengüeta y la fuerza de reacción pasan por el punto de enganche; sus distancias de brazo de momento son cero y caen fuera de la ecuación. La ecuación de momento ahora está resuelta para R w:
\( R_{w} = \frac{F_{cw}(4.6 \text{ m}) + F_{g}(4.25 \text{ m})}{4.6 \text{ m}} = \frac{43 \text{ kN}(4.6 \text{ m}) + 212 \text{ kNn}(4.25 \text{ m})}{4.6 \text{ m}} = 240 \text{ k} \)
Dado que hay dos ruedas, cada rueda debe soportar 120 kN.
Con la carga conocida, es posible calcular el diámetro del eje cilíndrico requerido para soportar la rueda. El eje (Figura 3.3.16) es una configuración en voladizo ya que está rígidamente fijado al bastidor en un extremo. La configuración simplificada del eje (Figura 3.3.16) muestra que la fuerza de reacción de la rueda se aplica a 30 cm de la base del eje. La fuerza hacia abajo del carro y el grano en la base del eje y la fuerza de reacción hacia arriba del neumático causarán tensión de flexión en el eje. El momento de flexión es:
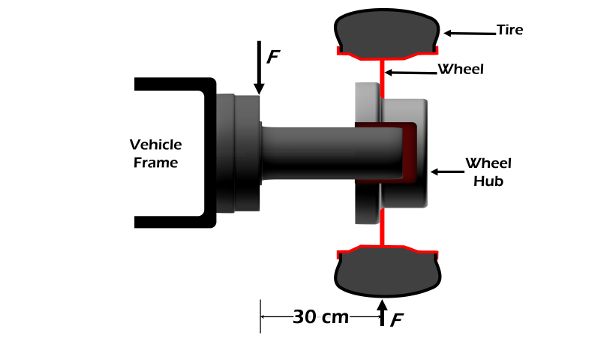
\( M=Fd=120,000 \text{ N }\cdot 0.3 \text{ m}= 3600 \text{ Nm} \)
El esfuerzo máximo en el eje no puede exceder el límite elástico del material, lo que provocaría una deformación permanente en el eje, comprometiendo su funcionalidad y resistencia. El diseñador necesita saber qué material se utilizará para fabricar el eje y luego determinar el límite elástico para ese material en particular. Se pueden consultar varios manuales de ingeniería de materiales y otros recursos para encontrar el límite elástico de diferentes materiales. Para este ejemplo, supongamos que se utilizaría acero dulce. El límite elástico para el acero dulce (σ y) se puede encontrar a partir de una serie de recursos que es de 250 MPa. Tenga en cuenta que un Pa se define como un N/m 2. El esfuerzo de flexión en el eje es (Ecuación 3.3.8):
\( \sigma_{b} = \frac{My}{I} \)
Tenga en cuenta que y es la distancia desde el eje neutro, que es el centro del eje circular. El esfuerzo máximo ocurrirá en la parte superior e inferior del eje. Las ecuaciones para el momento de inercia para diferentes formas transversales se pueden encontrar en una serie de manuales de ingeniería o libros de texto de fuerza de materiales. Para una sección transversal circular, el momento de inercia es:
\[ I = \frac{1}{4} \pi r^{4} \]
Sustituyendo la Ecuación 3.3.21 en la Ecuación 3.3.8, la ecuación de esfuerzo de flexión se convierte en
\( \sigma_{b} = \frac{4My}{\pi r^{4}} \)
Dado que el punto crítico de falla estará en las fibras más externas de la sección transversal circular, la tensión se calculará en y = r. Además, la tensión en esas fibras más externas no debe exceder la tensión de fluencia; por lo tanto,
\( \sigma_{y} = \frac{4M}{\pi r^{3}} \)
Ahora soluciona para r:
\( r^{3}=\frac{4M}{\pi \sigma_{y}} \ \cdot \frac{3600 \text{ Nm}}{1} \ \cdot \frac{m^{2}}{350 \times 10^{6} \text{ N}} \)
El radio mínimo calculado es de 2.6 cm.
Cualquier número calculado o salida de computadora siempre debe ser examinado para asegurarse de que representa una conclusión razonable. En este caso, un ingeniero experimentado debería preocuparse de que un eje de 2,6 cm de radio parezca inusualmente pequeño para un carro de grano grande. Existen varios factores que no fueron considerados en el análisis. Primero, la carga sobre el eje era el peso estático del carro y el grano. No hubo consideración para las cargas dinámicas máximas que se inducirían a medida que el vehículo se desplazaba por el terreno de un campo agrícola. El análisis dinámico también necesitaría considerar la tensión de fatiga en el material debido a la carga repetida. No se consideró factor de seguridad para compensar las inconsistencias en las propiedades materiales del eje o la sobrecarga del carro por parte del operador. Dependiendo del método de fijación del eje al bastidor, podría haber concentraciones significativas de tensión en esquinas afiladas o soldaduras. Estas concentraciones de estrés generalmente se identifican con un análisis de elementos finitos de la estructura. Pero aunque no ocurriera una falla catastrófica en el mecanismo, el ingeniero debería considerar los efectos de la elasticidad del eje. En este caso, una desviación elástica excesiva en el eje podría provocar que la llanta se desalinee, lo que podría provocar un seguimiento adverso del carro o un desgaste inaceptable de la llanta. Habría que abordar todos estos factores para lograr un diseño final que evite fallas y asegure un correcto funcionamiento.
Créditos de imagen
Figura 1. Stombaugh, T. (CC Por 4.0). (2020). Combine típico de grano.
Figura 2. Stamper, D. & Stombaugh, T. (CC Por 4.0). (2020). Fuerzas que actúan sobre el grano.
Figura 3. Stamper, D. & Stombaugh, T. (CC Por 4.0). (2020). Mecanismo de tamiz simple.
Figura 4. Stamper, D. & Stombaugh, T. (CC Por 4.0). (2020). Fuerzas de arrastre.
Figura 5. Stamper, D. & Stombaugh, T. (CC Por 4.0). (2020). Transportador de paletas.
Figura 6. Stamper, D. & Stombaugh, T. (CC Por 4.0). (2020). Transportador de tornillo.
Figura 7. Stombaugh, T. (CC Por 4.0). (2020). Combine y empacadora.
Figura 8. Stombaugh, T. (CC Por 4.0). (2020). Cabezal de cultivo en hilera.
Figura 9. Stamper, D. & Stombaugh, T. (CC Por 4.0). (2020). Cilindro de trilla convencional.
Figura 10. Stamper, D. & Stombaugh, T. (CC Por 4.0). (2020). Cilindro de trilla giratorio.
Figura 11. Stombaugh, T. (CC Por 4.0). (2020). Combine y carrito de grano.
Figura 12. Stamper, D. & Stombaugh, T. (CC Por 4.0). (2020). Combine ubicaciones de prueba.
Figura 13. Stamper, D. & Stombaugh, T. (CC Por 4.0). (2020). Carrete de recolección.
Figura 14. Stamper, D. & Stombaugh, T. (CC Por 4.0). (2020). Tractor y carro de grano.
Figura 15. Stamper, D. & Stombaugh, T. (CC Por 4.0). (2020). Fuerzas en el carro de grano.
Figura 16. Stamper, D. & Stombaugh, T. (CC Por 4.0). (2020). Configuración del eje.
Referencias
Estándares ASABE. (2015a). ASAE EP496.3 FEB2996 (R2015): Manejo de maquinaria agrícola. San José, MI: ASABE.
Estándares ASABE. (2015b). ASAE D497.7 MAR2011 (R2015): Datos de manejo de maquinaria agrícola. San José, MI: ASABE.
Srivastava, A. K., Goering, C. E., Rohrbach, R. P., & Buckmaster, D. R. (2006). Principios de ingeniería de máquinas agrícolas (2da ed.). San José, MI: ASABE.